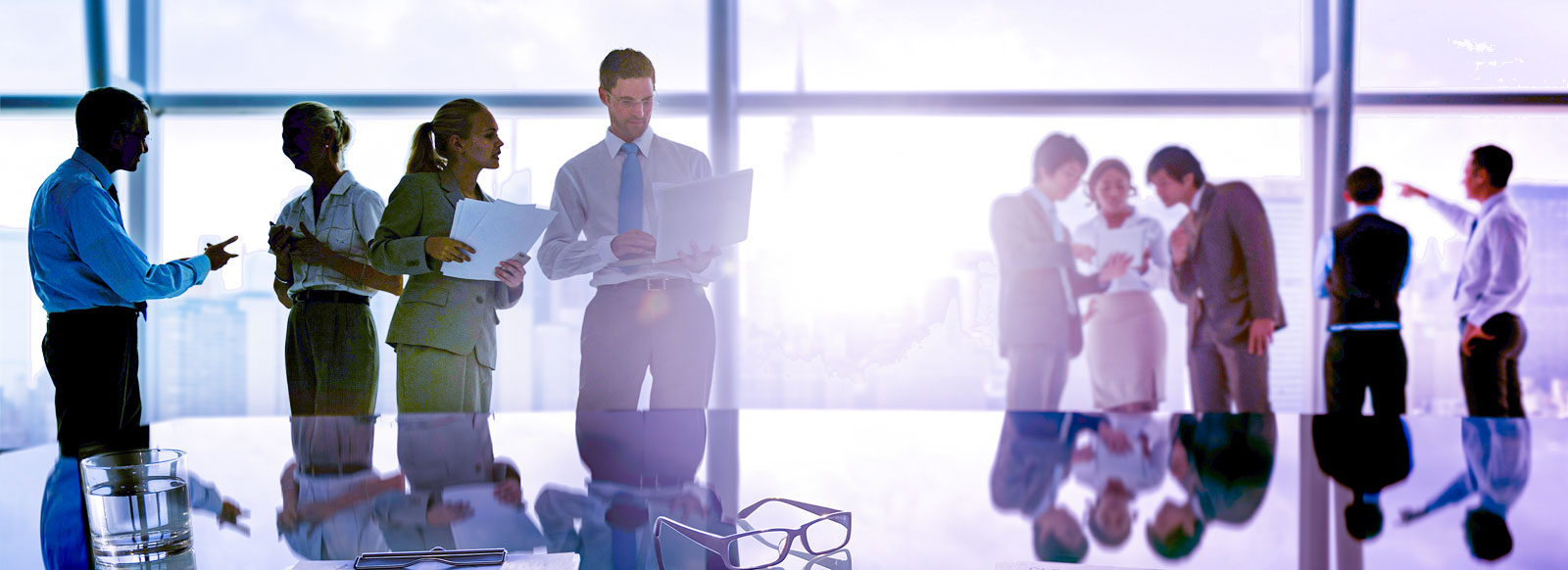
Change of any kind often requires a catalyst. This is particularly true in a business environment where the rule of thumb is to do things the way they’ve always been done. And when you’re working in a regulated industry, processes tend to get more locked in because compliance is at stake.
That was certainly the case when I worked in the medical device industry. The company I worked for used a paper-based system, and although I could see the benefits of digitizing, I wasn’t able to convince my superiors. It was only when we had a run-in with the U.S. Food and Drug Administration (FDA) and received a Form 483 that things started to change.
My experience is hardly unique. Change doesn’t happen until something comes along to disrupt the status quo. At MasterControl, we conducted research surrounding digital quality management in the life sciences. Our findings included information on what holds life sciences companies back from digitizing, and what pushes them forward. Cost, time, and disruption were the things that held companies back the most. One of the most common reasons they chose to move forward was because they received a warning letter from a regulatory body. Other reasons follow below.
|
Blockers to digital maturity in quality management
This table shows specific reasons companies cited for holding back. The first three reasons are all variations of a theme: letting short-term, negative consequences blind you to long-term benefits. That’s not to say those aren’t valid concerns. Yes, a new system will cost money. Yes, it will take time to transition. And yes, it does require a change in your business. However, focusing on these holdups completely ignores the benefits that digital systems bring. Digital systems cut costs in other areas, ultimately saving you more money than you spent on the system. The increased efficiency will more than make up for the disruption and time invested in the transition.
Anytime you want to try something new, you have to stop the old way of doing things. That means disrupting organizational momentum, which is very difficult. When processes in a company are moving, you need someone in senior leadership to make the call that things need to pause for digitization. In other words, you need to slow down to speed up. This doesn’t tend to happen unless something goes wrong. Then you realize that if you keep doing the same thing, the same problem will keep happening. In my company’s case, this was a Form 483, but it can be an error, deviation, or any other kind of problem.
Ideally, it wouldn’t take a problem to kickstart digital transformation. In our research, we did find that the No. 1 reason for increasing digitization wasn’t actually related to a problem.
|
Drivers for digital maturity in quality management
What’s pushing companies toward digitization the most is it’s a competitive advantage. This makes sense considering all the benefits that come with digital systems. It’s a competitive advantage to move faster while maintaining compliance. That’s a very difficult thing to do on paper. Anytime you need to change anything, it’s going to affect multiple employees and processes. Tracking that and making sure you don’t miss anything is problematic if you’re working on paper or using a Microsoft Excel spreadsheet.
Everything is so interconnected when it comes to quality and compliance. If you have a regulator show up and there’s a finding, you may need to change a standard operating procedure (SOP). If you change that, you have to make sure no older versions are still floating around the company in a binder somewhere or downloaded onto someone’s computer. Once you finish that, you have to make sure all necessary employees are trained on the new SOP. And, of course, you’re going to need to show that those employees have been trained at some point in the future. That’s all just a mess on paper, but in an electronic quality management system (eQMS), everything is connected automatically. That saves you so much time as you’re making these changes and ensures you don’t miss anything.
This doesn’t just apply to changes that come from inspections. It’s any change. That can be market forces, a new trend, or approval for a product. When things change, the organization that can keep up with that change is the one that has the advantage. That just reiterates my earlier point that you need to have senior leadership involved to overcome organizational momentum and make lasting change.
Getting started with digital maturity
When we talked to people about digital transformation, one of the things we had to keep in mind was that companies are at different stages of that journey. That’s going to affect what should be done in the immediate future. For example, a company that largely prints out paper and has filing cabinets full of quality documents is going to need to take steps to begin using a fully connected eQMS. And a company already using an eQMS is going to need to look into how advanced analytics and artificial intelligence (AI) can help them become even more efficient. Because digitizing revolves around technology, and technology is always advancing, this isn’t really a destination as much as a continual journey.
A lot of life sciences companies are already using technology to some extent. Maybe your organization is using an eQMS, but it doesn’t connect all your quality processes, or it’s not integrated with your other enterprise systems. When we conducted our research, we had to create a quality management maturity model to give respondents a concrete way to gauge their maturity and how they were doing in relation to their peers. We used this model to create an interactive assessment to help other life sciences companies figure out where they are and how to move forward.
You may feel like your company is too far behind for you to catch up. But it’s never too late to start, and you might not be as far behind as you think. We found that 61 percent of respondents use at least some digital systems, but they lack complete connectivity and integrations with other systems. Respondents also tended to overestimate the number of companies using AI in their quality management. Only three percent said they were using technology that advanced, but respondents thought that 14 percent were at that level. So, there’s no need to panic. But there is a need to act now.
To make the most informed decisions, you need all the information. The full report, “The State of Digital Quality Maturity in Pharma and Medtech,” is now available to help you see what’s possible in your organization.
Add new comment