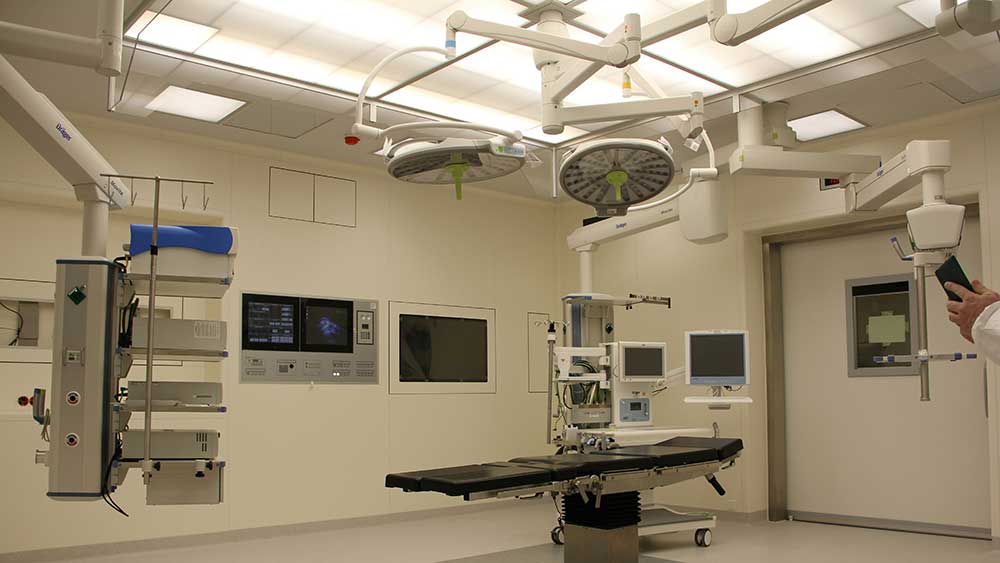
Photo by Marcel Scholte on Unsplash
Have you ever wondered what your medtech company looks like from the point of view of a U.S. Food and Drug Administration investigator? Well, this is your chance to find out.
ADVERTISEMENT |
Greenlight Guru invited Vincent Cafiso, a former FDA investigator, to the Global Medical Device Podcast to share his experiences from three decades of working in medtech. After leaving the FDA, Cafiso worked as a quality engineer and then moved into consulting. His current role is director of quality and regulatory services at Creo Consulting, so it’s fair to say he’s just about seen it all.
It’s worth listening to the entire conversation, but here we’ve pulled out three major pieces of advice that Cafiso would give any medtech company from his wealth of experience.
…
Add new comment