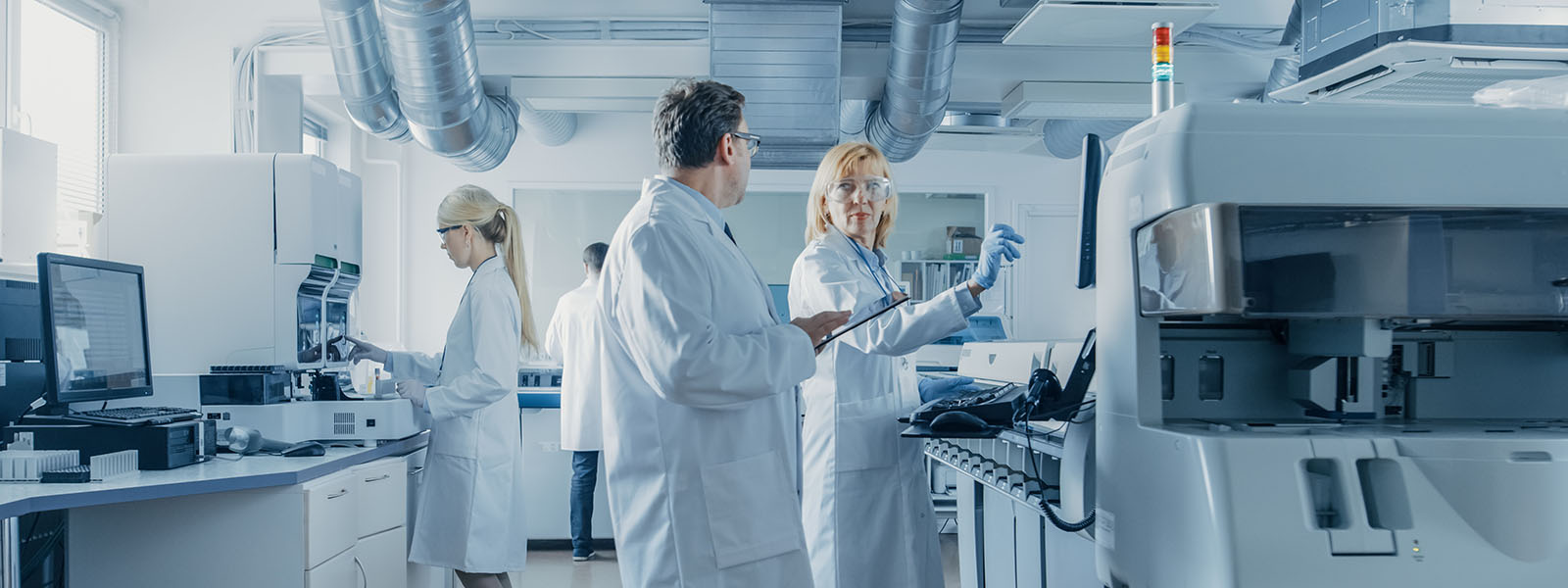
The ideal of proactive quality has been the holy grail of chief quality officers in the life sciences industry for at least five years, but few, if any, have realized the vision. Industry has since set out a clear definition of the milestones a medical product manufacturer would need to meet in order to achieve proactive quality as a differentiator. Many of those are cultural, but the majority require quality technology and innovation to reach the disruptive levels they have today.
Quality 4.0 is defined as the application of Industry 4.0’s advanced digital technologies to enhance traditional best practices in quality management. With the advent of such innovations as AI and IoT in the quality management ecosystem, the promise of proactive quality is finally a reality. Today the industry faces unprecedented challenges but also opportunities to serve patients like never before; both require innovation in business and product as well as in how companies approach quality.
This article highlights just one of these key challenges and opportunities: the increasing complexity and diversity of the supply chain itself. It emphasizes the reasons why recognizing and embracing bimodality is so vitally important, and how quality technology is a critical enabler for life sciences companies under these unique pressures.
Regardless of their niche within life sciences or their company size, all quality leaders share five key imperatives: product quality, product efficacy, patient safety, continuity of supply, and compliance. And, while these five things are front and center of the quality professional’s mind every hour of the day, increasingly over the past five years they have been faced with a bimodal challenge. Mode 1 is about operational stability, predictability, efficiency, and incremental continuous improvement, often characterized by the need to drive down total cost of quality (TCoQ). Mode 1 is risk-averse and focused on prevention. Mode 1 can be defined by those five imperatives.
Now, there is growing and competing tension with Mode 2. Mode 2 is exploratory. It is about innovative, creative out-of-the-box solutions. Mode 2 is about speed and big-step changes. It is risk-tolerant and proactive, where fast failure is allowed. Digital transformation and Industry 4.0 epitomize Mode 2. For quality, Mode 2 can be characterized by seven macro-industry trends:
• Process complexity and variability
• Pace of innovation
• Industry 4.0
• Novel medical product
• Patient-centricity
• Supply chain complexity
• Total cost of quality (TCoQ)
While our tireless quality leaders are buried under existing and mounting pressures of complex change controls, customer complaints in the thousands, product recalls, inspections and audits at multiple manufacturing sites at any given time, and increased and diversified suppliers, now the head of R&D is asking for unique quality system capabilities to support the development of an amazing novel product that will have far-reaching patient benefits. Meanwhile, the head of engineering is in her office needing quality system innovation for the digital “factory of the future” that was recently approved.
Furthermore, their business unit president is projecting double-digit growth, which, although a great problem to have, everyone knows will not be accompanied by double-digit increase in head count in the complaint-handling unit. The chief quality officer and chief financial officer have estimated total cost of quality at more than 20 percent of operations and set a target to reduce it below 10 percent within the next three years.
These challenges and disruptions are many and varied in scale and impact. They certainly vary more based on the scope or nature of a given business. For example, is it a large medical device manufacturer or a small, biotech firm? But, in general, we’ve defined this set of seven key macro-challenges or disruptions as those having the most significant relevance and impact, especially through the lens of quality and compliance.
Supply chain complexity
I’ve had the opportunity to witness an enormous increase in supply chain complexity since starting my career as a quality professional almost 30 years ago. Then, businesses were smaller—in revenue, scale, portfolio, and market share—and their supply chains were generally simpler, siloed, and decentralized.
Quality leaders were concerned with what raw material arrived at the dock at one end of the factory, and what left the warehouse at the other. Their world was primarily between those four walls. Even much of the distribution was under their control.
These past three decades have seen significant change even in the level of internal supply-chain complexity within a single company itself. For many reasons, legal entity structure has multiplied. Of course, most global regulators treat one legal entity as a supplier to another, even if those entities share a quality management system (QMS).
As businesses grew over the years, more manufacturing or R&D sites were added to the footprint. Consequently, the quality and compliance hurdles of product and technology transfer began to rise as well.
During the past decade, many in life sciences watched as the pendulum swung, and plant rationalization or asset reduction became a key cost containment strategy. This only added to the quality system challenges of product transfer and scale-up.
Today the giant, global third-party logistics companies and those previously considered as distributors are playing an increasingly vital and very different role in patient service. Many now manage shipping, storage, and bidirectional distribution, frequently under increasingly stringent temperature and environmental controls. They also are accountable for postponement and finishing, kitting, and multilingual labeling. In doing so, they have become both a distributor and manufacturer. Many have struggled with the quality management needs of such a mission-critical change in accountability.
The ever-increasing reliance life sciences has on e-commerce also brings both value and emerging challenges.
The level of outsourcing to contract manufacturing organizations (CMOs) is higher than it has ever been.
Some data suggest that industrywide, upward of two-thirds of the supply chain is now external. Not only is the amount of outsourcing high and increasing, but also the nature of the companies to which that outsourcing is going is changing—sometimes radically. Ventilator medical device manufactures have outsourced production to automotive or even vacuum cleaner manufacturers in the fight against the Covid-19 pandemic.
Such partnerships may be necessary and highly successful, but they can’t occur without increased levels of risk and QMS complexity and reliance. It will be interesting to see if this kind of outsourcing will endure and become yet another instance of our “new normal.”
Another significant contributor to supply chain complexity is the unprecedented level of mergers and acquisitions. McKinsey & Co. states that 50 to 60 percent of the growth strategy industrywide is now inorganic, with growth and product being bought into a business. If a company isn’t buying, it’s being bought—or selling and divesting in order to buy. In the case of an acquisition, QMS integration is either planned for or often intentionally set aside. A business acquiring a business is inevitably acquiring yet another QMS.
Sometimes such an integration is perceived as being too difficult to be feasible. Even if tackled, integration is always a costly challenge laden with risk.
It is well documented that a lack of supplier control is a major contributor to product recalls and field actions in life sciences. Therefore, it should come as no surprise to see that problem continues to persist. Here again is where the differentiating capabilities that proactive quality solutions bring positively disrupts the paradigm.
Whether it’s managing thousands of suppliers or facilitating an acquisition or divestiture, the ability to virtualize the QMS out to the external nodes of the supply chain and collaborate directly at the data level is a game changer. Still too often today, even the biggest and brightest medical product manufacturers rely on manual communication methods—email, phone calls, and even faxes—that result in limited ability to trace, control, and report on supplier-related quality issues. In a 2016 study by KPMG, a staggering 43 percent of manufacturers reported having limited or no visibility into their supplier network, with only 13 percent having “complete” visibility past their tier one suppliers.
Across manufacturing industries, the companies that win in the 2020s will be those that use digital to redefine the meaning of quality excellence.
And what about the supplier or the CMO? Their lives are no less complicated as they serve an increasingly large and complex number of customers. They must deal with myriad associated QMS of every shape and level of capability. They, too, can only benefit from improved integration and collaboration, increased efficiency and effectiveness, improved quality and compliance risk reduction, and ultimately, stronger competitive differentiation.
Great supplier quality management starts with supplier evaluation, selection, and onboarding, followed by ongoing performance measurement, performance control, and effective, efficient, and holistic issue and incident management. The ability now to manage supplier-related corrective and preventive action (CAPA) or supplier-related product, process, and equipment changes—collaboratively, at the data level in the host QMS—will bring much-needed relief to this growing, challenging, and vitally important industry trend.
In conclusion
Understanding and embracing bimodality, and seeing how it impacts businesses and their quality management ecosystems, has never been so important in the life sciences industry. Balancing the quality needs of today in Mode 1 with those from Mode 2 already with us or rapidly approaching is a vital act to master.
Digital transformation appears to be moving in a global wave from North America through Europe and out to the Asia–Pacific region. Digital transformation of QMS may not be a 2021 imperative for all businesses, but it is an inevitable event they will face in the coming years. It’s not a matter of if, but when and how.
Understanding all of these trends and their interplay with the QMS is important in many ways, perhaps none more so than in enabling a quality organization and its IT partners to win the inevitable: internal competition for project funding within their business.
A business’s relationship with the QMS solution and the provider of that solution should, similarly, be a long-term one. It is imperative that businesses invest both for today and tomorrow, however uncertain that future may look. Better understanding these trends helps a business develop a short-, medium-, and long-term strategy for their QMS and all the vital interconnections that QMS has throughout the broader supply chain architecture.
In my experience, quality leaders may not even be privy to the potential impacts these trends could have on their businesses. R&D pipelines as well as mergers, acquisitions, and divestitures are always confidential below the C suite. However, quality leaders don’t need to know exactly what the product or acquisition is to know that it will impact their quality and compliance landscape.
Digital transformation is not about software; it’s about data, process, people, talent—with technology as an enabler. The most important skills for driving the overall success of a digital quality transformation are the so-called “soft skills” such as communication, teamwork, and change management.
Be bimodal. Keep your finger on the pulse of the industry. Understand these and other impactful trends. Strive to realize the promise of proactive quality and embrace the inevitable digital quality transformation. There’s nothing more rewarding for quality leaders than the opportunity to show up as true business leaders who can demonstrate the value of their quality organization and its impact on the health and wellness of the global population.
Add new comment