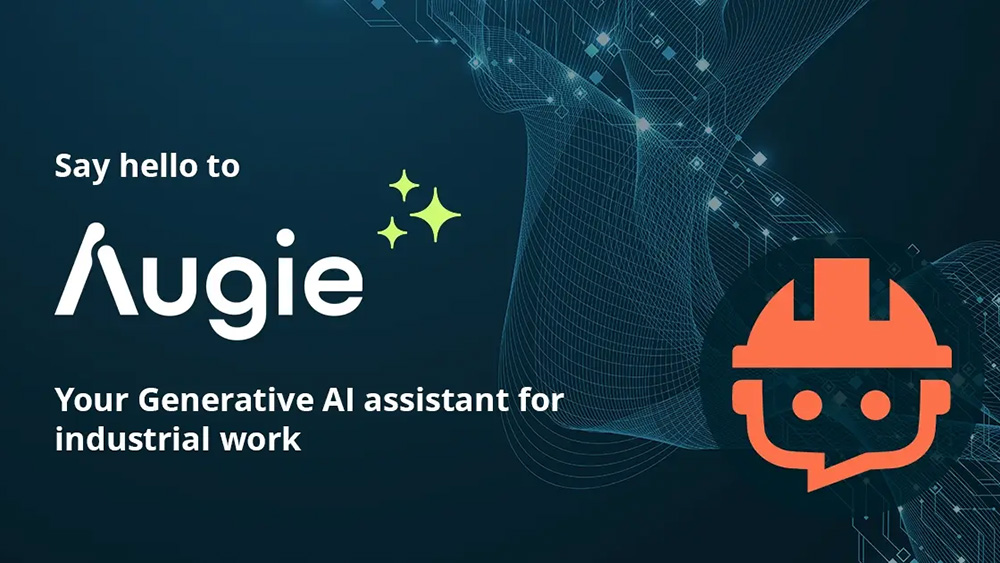
Augie, Augmentir’s industrial generative AI assistant, is designed to enhance manufacturing operations. Unlike standard AI-powered helpers, Augie relies on real-time operational data, workforce insights, and training records to deliver solutions that integrate smoothly into daily workflows. It considers job roles, skill levels, and the equipment a worker handles to provide valuable and specific guidance to the task at hand.
ADVERTISEMENT |
In this Q&A, Quality Digest spoke candidly with Augie about customizing AI-generated insights, preserving industry knowledge, protecting sensitive data, and supporting a global workforce while addressing concerns about AI adoption in manufacturing.
Quality Digest: How does Augie ensure that the AI-generated solutions and insights are tailored to each manufacturing environment’s challenges and unique workflows?
…
Add new comment