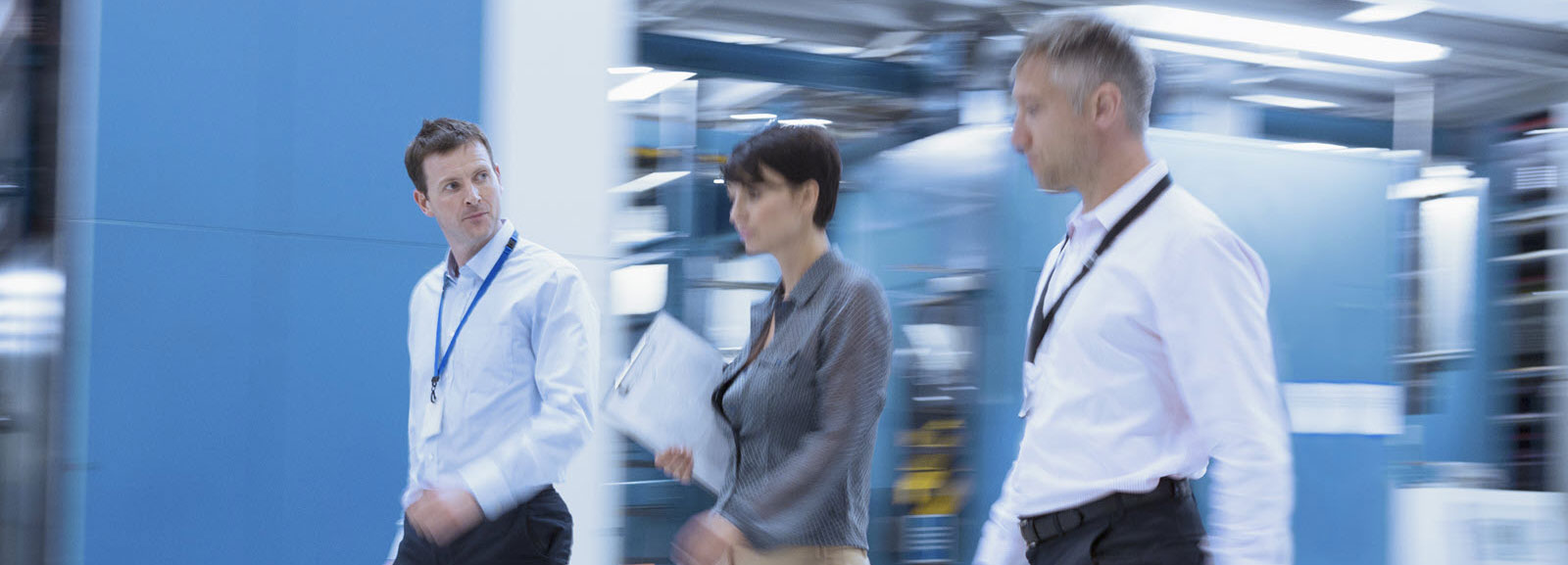
The Covid-19 pandemic has hit every industry with a barrage of challenges. The impacts on the manufacturing sector are already extending far beyond factory walls. And for now, the depth of those impacts and the expectation for recovery are unknown.
Fortunately, manufacturers are a highly adaptable breed, and many have found ways to pivot quickly to continue to provide the vital products we all need. Some organizations are even retooling and repurposing their production lines to produce entirely new products. Perfumers and distilleries are producing hand sanitizer. T-shirt makers are switching to face masks. Automakers are now producing ventilators.
These companies stepped up early and responded quickly. And we are grateful.
But for many manufacturers, regardless of their grit and preparation, the situation has thrown into sharp relief the need for technology solutions that enable faster, broader access to information about their operations—and better support for both onsite and remote workers.
A sudden shove toward digital transformation
Manufacturing organizations have embraced many aspects of Industry 4.0. However, the transition has happened at different levels for different organizations. Many companies have held on to legacy systems, especially in the realm of quality management.
What does a legacy quality management system look like? For many organizations, it’s a conglomeration of disparate on-premises systems, kept in place as facilities were acquired or added, and acting autonomously. For other organizations, it’s a giant set of spreadsheets, meticulously updated by quality and plant managers—typically long after the data are usable. And for some, it still means paper checklists, diligently completed by operators and filed in a drawer.
Those types of legacy systems create a level of data inaccessibility that is a serious roadblock in the current circumstances. And it’s creating an imperative for organizations to find alternative technology solutions that better support a geographically dispersed organization—fast.
Fortunately, the solutions they need already exist.
Accelerating digital transformation with cloud-based quality management software
Cloud-based software-as-a-service (SaaS) solutions are ubiquitous in our everyday lives, giving us the ability to use our smartphones to manage our bank accounts, order groceries—and support our favorite local restaurant by staying at home and ordering takeout.
For manufacturers, cloud-based quality management can enable that same level of connectivity and accessibility, something they may not have at the moment and truly need.
How? By providing a way to centralize and standardize data—from any device, line, or facility—so that workers at every level can get the information they need in real time.
Supporting plant-floor operators
Operators are at the front line of production, so providing the support they need to do their jobs safely—while maintaining product quality and compliance standards—is at the top of the list for most manufacturers that are dealing with:
Reduced workforce. Social distancing rules may mean fewer workers on the plant floor and staggered shift start times. In addition, workers may be stepping up to cover jobs when their colleagues aren’t able to be at work due to illness or quarantine.
Product changes. Onsite operators and supervisors may need to deal with new processes and products, and may need to do jobs they aren’t fully familiar with or work on a line they don’t normally run.
Cloud software enables the creation of customized dashboards for presenting role- and task-based information. Dashboards help workers maintain accuracy and quality even when producing an entirely new product and help keep them focused by eliminating a barrage of information they don’t need. Dashboards can be customized to visually display:
• Timed data collections
• Guided data collections and workflows
• Quality and safety checklists
• Alerts and notifications
Supporting quality professionals
Quality professionals are highly essential to the smooth operation of your plant. However, their presence on the plant floor may be considered “optional,” so plant-level quality managers may be doing their work from home—many for the first time.
Whether these quality professionals are onsite or working remotely, a cloud-based quality management solution provides:
• Real-time access to centralized data for fast analysis and responses
• Dashboard-based analysis tools that leverage traditional statistical process control (SPC) methodology while enabling dynamic, graphical views of information
• Flexible reporting capabilities that enable quality professionals to produce reports and respond to audits on demand for a variety of stakeholders
Supporting executives
With changes coming daily from inside and outside the organization, company executives are working to maintain strong leadership and messaging—while making data-based decisions to adapt and optimize operations.
The power of centralized data truly delivers for these leaders, giving them the ability to aggregate and analyze data from across all their facilities, and see information in ways they might not have thought possible. A big-picture view of organizational data can help leaders:
• Ensure policies and best practices are standardized and consistent across all sites
• Quickly determine site potential yields and adjust output
• Spot opportunities for optimizing operations quickly
If not now, when?
Right now, collecting data isn’t a problem. Getting the right information to the people who need it to do their jobs is a bigger challenge. Cloud software solutions are proven, secure, surprisingly affordable, and designed for quick rollout. For manufacturers facing a long period of crisis—and potentially a longer recovery—now may be the perfect time to embrace digital transformation.
At InfinityQS, we understand that we all face some challenging and tumultuous times ahead. But we face them together. For the days and weeks to come, we wish all our manufacturing colleagues the very best. Feel free to visit our website to learn more about how our software solutions can help your organization in immediate and practical ways. Stay safe—and let us know how we can help you.
Add new comment