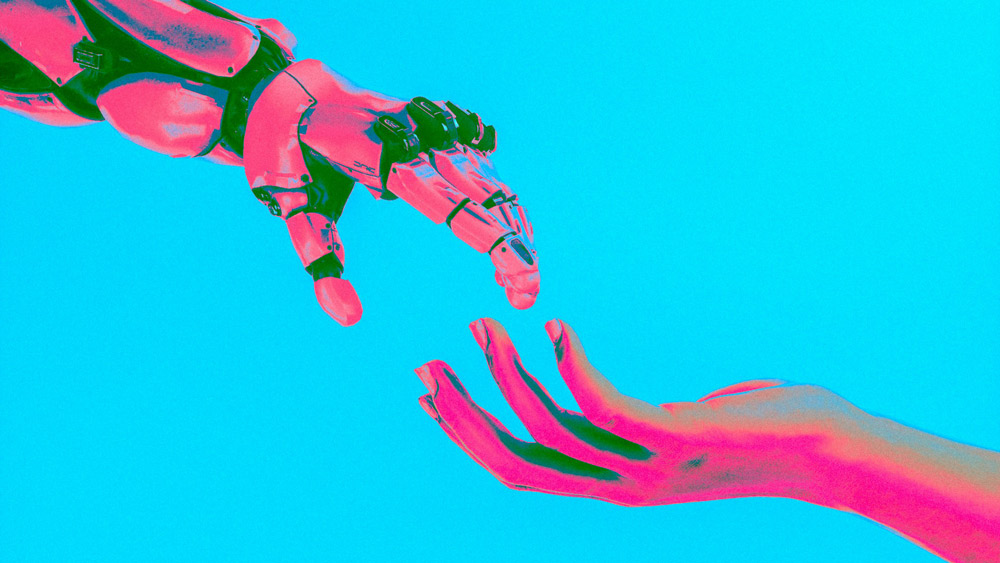
AI tools can boost and support human achievement. Photo by Cash Macanaya on Unsplash
Body
Hexagon is frequently at the fore of innovation. Like many in its industry, part of the company’s initiative to succeed is rooted in the constant push to automate tedious processes that take up valuable time, eat up resources and personnel, and delay production and delivery of products. Tools like ESPRIT EDGE software and
…
Want to continue?
Log in or create a FREE account.
By logging in you agree to receive communication from Quality Digest.
Privacy Policy.
Add new comment