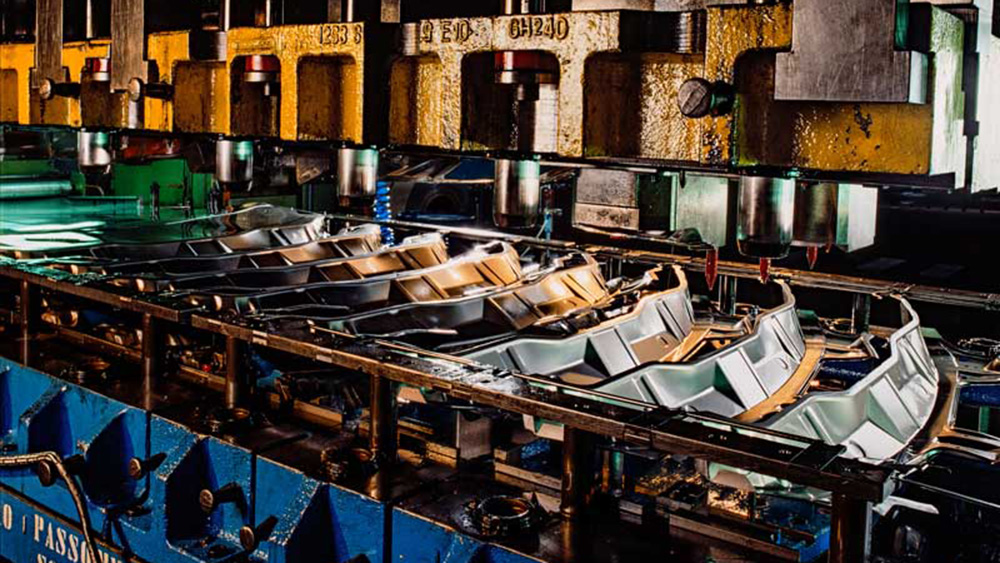
Each type of part presents its own set of inspection challenges. This is especially true for sheet metal parts that are made of various entities, each with different positioning and dimensioning tolerances, and variable thickness gauges and sizes. These features can be inherently laborious to inspect regardless of the measurement technique.
ADVERTISEMENT |
The material’s thin edges and flexible nature, its complex geometries with intricate bends and punched holes, and large components like automotive body panels all add to the complexity. These challenges are further compounded by variations introduced through the manufacturing process, like stamping and bending.
This article outlines the key factors operators must consider when inspecting sheet metal, depending on the technique used—whether it’s a coordinate measuring machine (CMM), checking fixtures, gray value features, or 3D scanners.
What to be aware of when measuring sheet metal parts with the CMM
Accurate and repeatable, but...
In the automotive and aerospace industries, sheet metal inspection is still widely covered with the CMM. By physically touching the sheet metal surface with a precision stylus, touch-probing technology ensures highly accurate and repeatable data collection with minimal uncertainty.
It’s slow
However, the process is inherently slow because each feature is measured individually, requiring multiple contact points to assess flatness, holes, edges, and critical dimensions. These sequences take time, extending the overall inspection process and reducing efficiency when multiple sheet metal parts are waiting for measurement.
Complicated to program and set up
Programming an efficient probing sequence is crucial to minimizing unnecessary movements, avoiding collisions, and reducing errors. The touch probe must carefully navigate around features, which increases measurement time. Skilled operators may also need to adjust setups, recalibrate probes, or verify results, adding manual steps that further slow the inspection process.
Limited coverage
Because point-based probing captures only discrete dimensions, it’s well suited for inspecting critical features. But it may miss surface variations and warping. Without complete surface data, evaluating overall geometry and comparing deviations against nominal CAD models becomes challenging. In industries where surface integrity and form accuracy are essential, relying solely on point probing can result in undetected defects, potentially affecting assembly and functionality.
As a result, while the CMM excels at high-precision tasks, the slow speed and complexity of touch probing make it less suitable for high-throughput inspections.
Stamping departments produce hundreds of sheet metal parts per day. But the slow pace of CMM inspection prevents them from thoroughly checking each part and identifying issues on the production line. The combination of high production volumes and stringent tolerance requirements inevitably creates bottlenecks in the manufacturing process.
Consequently, the automotive and aerospace industries are actively seeking faster sheet-metal inspection solutions that can be deployed closer to the production floor and provide 100% inspection coverage.
What to know before investing in a checking fixture for inspecting sheet metal parts
Fast and repeatable, but...
Checking fixtures offer fast, repeatable, and operator-friendly inspections, making them ideal for high-volume production. They ensure consistent quality control by providing go/no-go verification with minimal training. Operators can easily place the part in the fixture and check for deviations, streamlining inspections without complex equipment or software.
Not versatile
Checking fixtures are designed for specific parts, meaning each new sheet metal design requires a new fixture. This lack of versatility adds time and cost to product changes, because any modification to a part renders its fixture obsolete or in need of an update.
Expensive to design, store, and maintain
Fixtures can wear over time, leading to inaccurate inspections if not properly maintained or calibrated. Their bulky nature also demands significant storage costs. Additionally, designing and manufacturing custom fixtures is expensive, especially for short production runs, making them less cost-effective when frequent design changes are expected.
As a result, checking fixtures are highly effective for high-volume production when no design changes are expected. However, professionals in the automotive and aerospace industries may benefit more from a solution that’s just as fast and repeatable while also providing greater versatility for design changes. This approach will lead to savings in initial investment, maintenance, and storage costs.
What to watch when inspecting sheet metal quality using gray-value features
Accurate if...
Operators must correctly adjust various acquisition and inspection parameters such as camera angles, fit zones, and exposure time. These settings ensure that the images have optimal contrast and clarity to highlight differences in surface textures and detect potential defects. But, as even minor deviations can lead to inaccurate measurements, the overall method becomes heavily dependent on the operator’s skills and experience to navigate these adjustments.
Slow and complicated workflow
The inspection process becomes complex when incorporating photogrammetry, because this method requires capturing a large number of images from various angles. This, combined with the need to fine-tune multiple parameters, significantly slows down the workflow. Both the setup and data acquisition times are extended because each shot requires precise calibration and alignment.
Sensitive to environmental conditions
The image-based inspection method performs optimally only under controlled lighting conditions. Even slight variations in ambient light, part color, or background can alter contrast (or gray values), affecting how the part appears in its environment. These inconsistencies can interfere with image capture, potentially distorting the distribution of gray levels and compromising defect detection.
As a result, gray value features provide detailed sheet metal analysis only under controlled lighting conditions, requiring stable lighting and backgrounds for accurate results—difficult to achieve in a shop-floor environment. Even then, their effectiveness relies on precise parameter adjustments, making the process complex and highly operator-dependent. To optimize sheet metal inspection, the automotive and aerospace industries might find greater value in a solution independent of both the operator and the environment.
What to know about edge-based feature extraction
Sensitive to mesh structure and resolution
This technique is sensitive to the mesh structure and resolution because it relies on the accuracy and density of the 3D scan data to extract edges and geometric entities effectively. A low-resolution scan produces a coarse mesh, causing edges to appear jagged or incomplete, and making it difficult to extract precise lines and curves. Similarly, if the mesh isn’t well structured, edges may appear fragmented or uneven, negatively affecting feature extraction.
Slow with higher resolution
Increasing the resolution to capture finer details can improve entity extraction accuracy. A denser mesh provides smoother, more continuous edges, but it also slows down the scanning process, reducing inspection efficiency. This trade-off makes high-resolution scanning impractical for high-throughput inspections such as those required for sheet metal parts.
Results too dependent on operators and parameters
When results depend on resolution settings and extraction parameters, it becomes easier to question the reliability of the data and equipment rather than address potential manufacturing defects. This issue is especially critical for complex sheet metal parts that require accurate data acquisition and thorough analysis. Similarly, different operators may extract different results depending on their judgment, experience, and parameter choices, further adding variability.
As a result, quality departments must eliminate ambiguity and variations originating from the equipment or the measurement method. Again, professionals in the automotive and aerospace industries need a reliable inspection method—one that’s independent of mesh structure and scan resolution, and unaffected by environmental conditions or operator skill levels.
Ideal method for inspecting sheet metal parts
If each inspection technique presents its own set of challenges, is there an ideal method for inspecting sheet metal parts? This is the initiative the Creaform team has undertaken in collaboration with major automotive manufacturers.
Operator-independent for optimized accuracy
Creaform developed a new sheet-metal inspection solution capable of capturing 2D entities without relying on the operator’s skills to adjust complex extraction parameters or needing to consider mesh structure or scan resolution. The method involves visual indicators to ensure optimal data acquisition and intuitive data validation, confirming that all necessary information for accurate inspection is collected. It’s a 3D scanning solution with a simple, intuitive interface that provides step-by-step guidance, resulting in fewer parameters needing adjustment during acquisition. This minimizes operator influence on measurement variability and ensures exceptional accuracy in any conditions.
Fast, versatile, and shop floor-ready
This sheet metal inspection solution is five times faster than a CMM, capturing comprehensive part data in a single scan while extracting additional information such as surface profiles. An innovative technique that remains unaffected by environmental conditions, it’s easily deployable on the production floor, adapts seamlessly to design changes, and measures various part shapes and sizes—all with the same scanning device.
In short, it’s a sheet metal inspection solution that addresses all the weaknesses previously stated.
Published March 11, 2025, by Creaform.
Add new comment