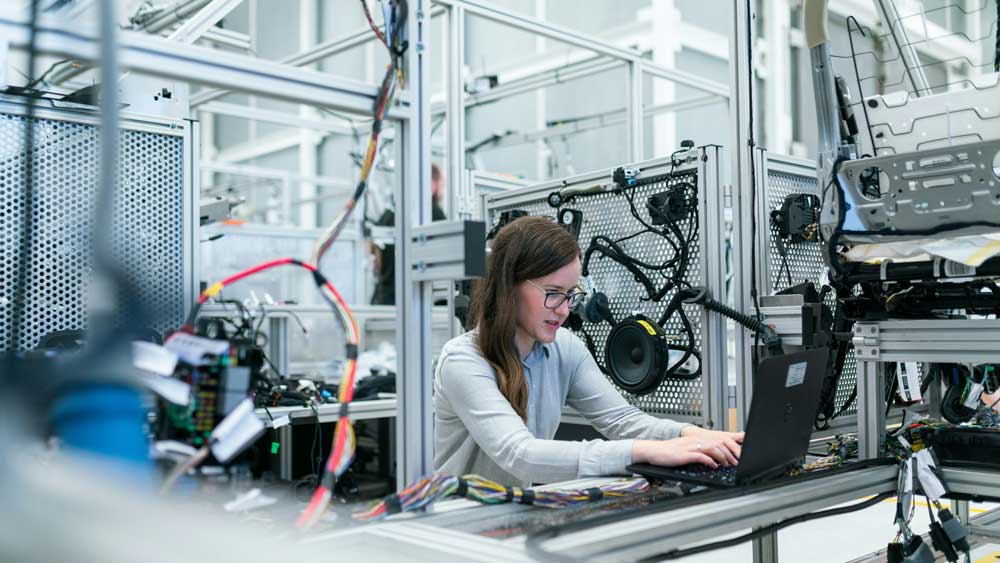
The global order is shifting under our feet, and America’s role in that order may evolve significantly over the next 50 years. Photo by ThisisEngineering on Unsplash
The state of American manufacturing is in dire need of improvement. For decades, the U.S. economy has been transforming into a service-based model while the manufacturing power we associate with the American postwar capacity of the 1950s and ’60s has dispersed offshore.
ADVERTISEMENT |
This slow degradation of U.S. manufacturing capacity is coupled with fears of a significant labor shortage. A recent study by Deloitte found that by 2033, U.S. manufacturers will need about 3.8 million new workers, and half of those jobs might go unfilled. As an industry, we can’t remain on the same path and risk falling behind to an irreversible degree.
A popular narrative right now is that automation and our advancements in machine learning will help mitigate the effects of this predicted labor shortage. However, with global competitors also making strides in these areas, the U.S. faces losing ground in the global landscape.
…
Comments
Integration of AI with existing workers
The statement "The companies that win will be the ones that figure out how to make humans and AI work together, not replace one with the other." caught my attention.
The principles of Lean Manufacturing and the TPS have proven that it is possible to join the two intelligently to create efficient production. At the heart of their success is a deep understanding of what people are good at and what machines (or AI) is good at. In the past it was generally viewed that humans were best at decisions. That is changing with AI. The discussion is not to a point of which decisions are workers best at and which is AI best at? And then the real magic is our ability to integrate both on the same production process.
It really does look like we are approaching exciting times.
Add new comment