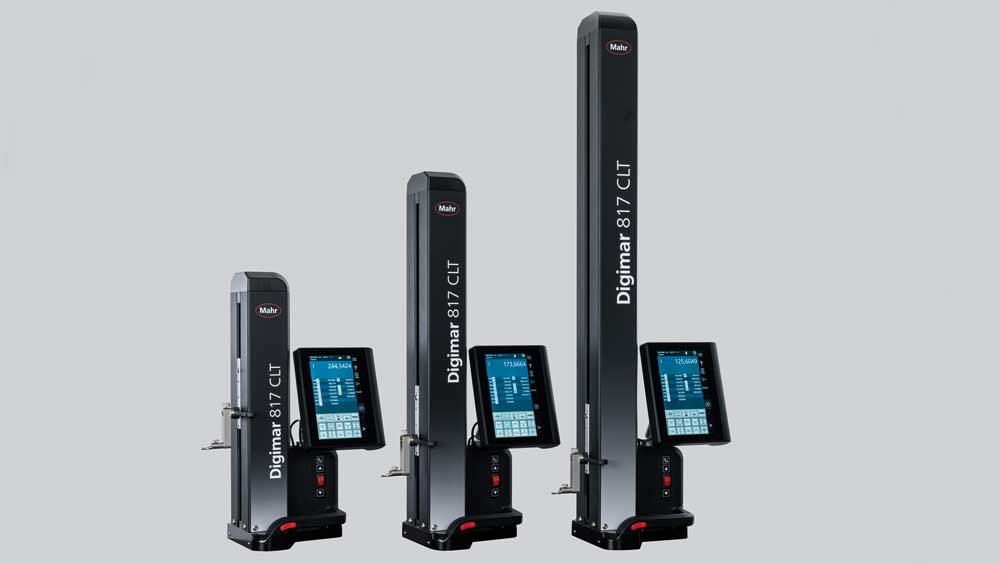
Mahr Digimar 817 CLT height gages: 350 mm, 600 mm and 1,000 mm
The need for long-range height measurements has been around since the principles of layout work became a fundamental requirement in machine shops.
ADVERTISEMENT |
The first step in the manufacturing process is to lay out a piece by transferring a design or pattern to a workpiece. This is performed in almost all small shops, large manufacturing plants, and even by home hobbyists. The process may be used to begin a prototype piece or an emergency replacement part. The common tools for layout work include a surface plate, a surface gage with scriber or dial indicator, and a long-range height gage.
As with most inspection, the surface plate provides a reference plane for the part and the height gage. Height gages are used to set and mark a certain height on the workpiece, or to measure the piece after it has been machined.
…
Add new comment