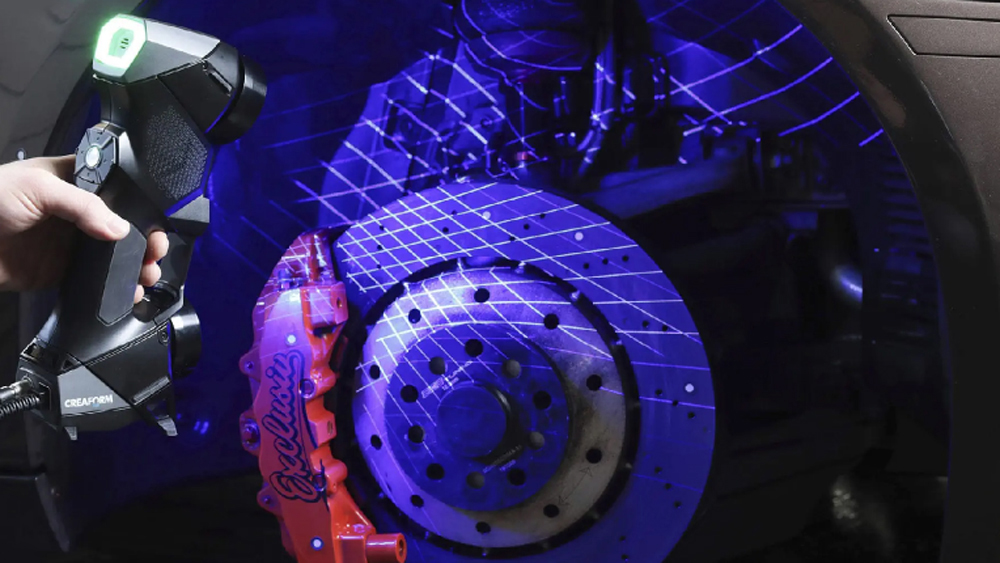
In today’s market, it seems like all 3D scanners have similar specifications, as if manufacturers look at their competitors’ data and use the same numbers. Data sheets, marketing videos, and even product appearances all look comparable, making it difficult to distinguish quality based on technical data alone.
ADVERTISEMENT |
So, when faced with multiple options, how can we identify a high-quality 3D scanner?
In this article, Creaform presents three practical tests that require no calibrated artifact to determine whether the performance claimed on technical specification sheets is achievable in real-life scenarios or just numbers without tangible value on paper. These tests are intended to help you identify which manufacturers have rigorously developed and tested their 3D scanners.
…
Comments
3D Scanning
"It's not how small a defect you can find that counts. It's how big a defect you can miss"
Add new comment