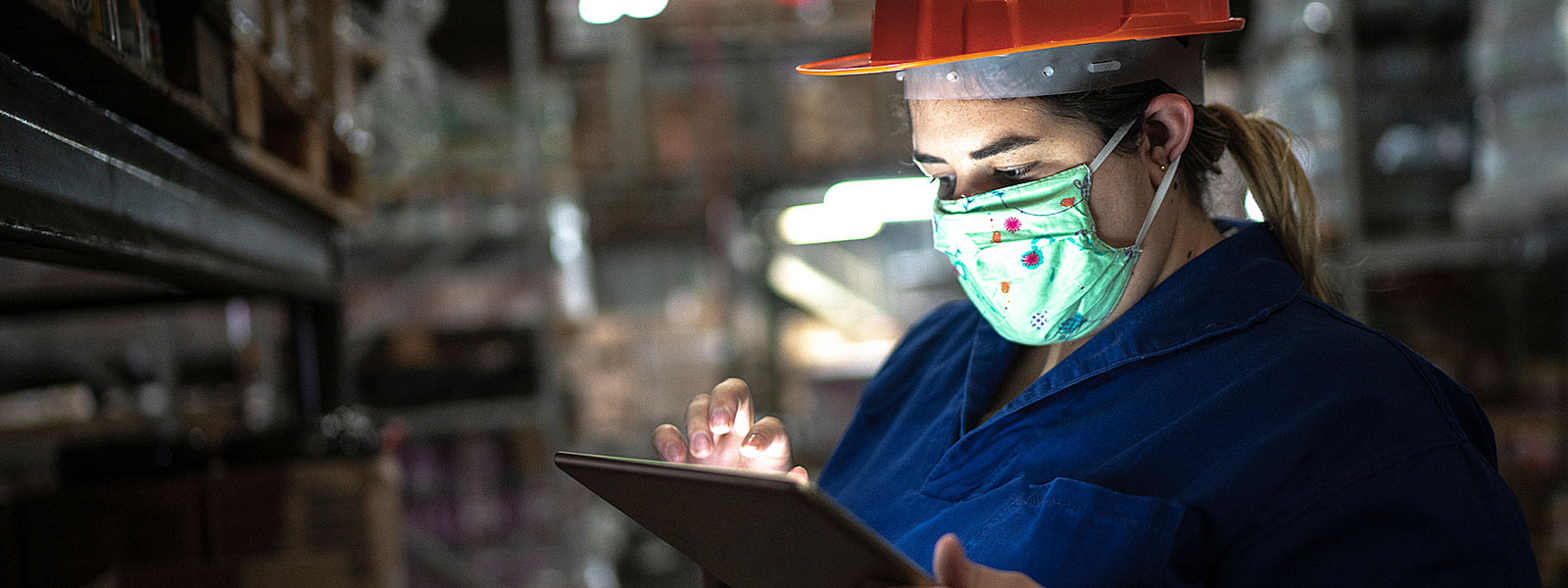
For manufacturers—as for all of us—the past few months have been a blur of fast adaptations and long periods of waiting. At the start of the pandemic, many manufacturers did what they have always done in the face of disruption: adapt and find the fastest workaround for the challenge at hand.
Manufacturers already know that rapid adaptation is an accepted cost of doing business. Uncertainty, risk, and volatility are not new for these seasoned organizations. However, the universal nature of this crisis, and the fact that it’s far from over, have highlighted areas in which complex quality management systems and procedures stand in the way of agile responses and effective operational optimization.
Many manufacturers have taken advantage of the opportunity to examine their operations with a fresh perspective, seeking proactive changes that will pave the way forward in a post-Covid-19 world.
A three-phase journey: survival, recovery, and resilience
Phase 1: Survival demands flexibility
During the current health crisis, manufacturing has been under immense pressure to maintain operational efficiency and uphold product quality and safety—in less-than-optimal conditions. Many organizations have had to reduce the number of employees working per shift, making social distancing easier but reducing production capacity.
Others moved staff deemed “nonessential” to plant-floor operations—such as quality professionals and plant managers—to home offices. For manufacturers that have relied largely on paper-based processes or on-premises software for quality management, this shift has made it extraordinarily difficult to provide those newly remote employees access to critical quality and process data.
In contrast, some companies have been able to pivot operations effectively to completely new product categories. Many quickly pitched in to provide essential goods for the fight against Covid-19. We saw breweries and distilleries switch to producing hand sanitizer, and other manufacturers retooling to produce personal protective equipment (PPE) for healthcare workers. These commendable efforts require manufacturing environments and quality procedures that can quickly adapt as necessary.
In all cases, flexibility is essential for manufacturers to survive in the current crisis. Now more than ever, manufacturers should consider the role that technology can play in enabling this flexibility—to support production processes, quality control, and employees.
• Organizations struggling with reduced plant-floor staff and remote teams can look to cloud-based quality management solutions that provide access to data from anywhere.
• For plant-floor operators who may be stretched thin at the moment, modern software solutions automate routine activities such as data collection, process monitoring, and reporting to help keep up with critical quality and safety checks.
• Remote quality teams can receive automated alerts about plant-floor problems—and even observe performance trends to ensure corrective actions are taken to prevent larger issues.
When standardized across multiple lines and sites, these solutions can also help company leaders run cross-plant analyses to identify opportunities for improvement. Centralized data analytics can help teams quickly align best practices across the entire enterprise, all safely from home.
Real-time access to quality data and the ability to analyze and respond to those data are all worthwhile investments that can help organizations survive the current situation and optimize operations as part of broader digital transformations for the future.
But survival is just the first step
Phase 2: Recovery demands strategy, not firefighting
Most organizations have recognized that recovery doesn’t mean a return to the way things were before. It means moving forward.
The impact of Covid-19 will be felt long after the dust settles. Some employees may end up working from home indefinitely. Sites may continue to run with reduced staff numbers on each shift. And supply-chain volatility may continue to challenge just-in-time planning. These issues won’t be solved with temporary fixes. Manufacturers need to make changes now that will enable the long-term transformation of their operations and adapt to the emerging “new normal.”
One of the first initiatives to consider is moving beyond “firefighting” tactics to more strategic responses. Many manufacturing organizations have historically taken a reactive approach to quality control and overall manufacturing operations. When issues arise, teams scramble to respond, only to have the same problems flare up repeatedly over time. This firefighting model is time-consuming and tiresome—not strategic or sustainable.
The way forward in recovery is for manufacturers to learn from the crisis and proactively identify pain points across their operations. These may include challenges in:
• Accessing data
• Quick decision-making
• Agile responses
When you understand your key pain points, it’s possible to work through sustainable, practical improvements to eliminate them.
Many issues can be addressed with the effective use of technologies. When seeking solutions, ask questions such as:
• Do we have the tools necessary for employees to work remotely?
• How are our technology limitations impacting productivity?
• Where are the gaps in our data?
• Are we able to understand our process performance?
• Where do we have operational blind spots within individual plants? Across the enterprise?
With answers to questions like these, organizations can build a vision for the future with a pipeline of short-term and long-term transformation opportunities.
Opportunities provide a path from recovery to resilience in the post-pandemic world
Phase 3: Resilience through digital transformation
Perhaps the biggest lesson to take away from Covid-19 is the imperative around digital transformation. Once a low priority on company budgets and agendas, it has suddenly been pushed to the forefront of investment. Manufacturers that learned how deficiencies in their technology and infrastructure impaired their ability to respond and pivot operations are placing particular urgency on updating their digital capabilities.
Manufacturers want to create nimble, flexible, and proactive manufacturing environments—driven by data. This is a remarkable shift from the investments in electro-mechanical automation seen during recent decades, which primarily focused on improving efficiency and productivity.
We now can do more than automate manufacturing. We can optimize processes, providing intelligent ways to understand what’s happening on the plant floor and make informed decisions. Dynamic, intuitive analytics help leaders drive enhancements and adjust operations to benefit everyone across the organization. The results are agility and resilience—which are exactly what we need to thrive now and long into the future.
Cloud technology dramatically simplifies quality management
Even in the midst of a global pandemic, product safety and quality remain critical. And manufacturers overall have done a remarkable job of adapting and maintaining their operations.
But a crisis like this is an open invitation for manufacturers to consider not just maintaining what they’ve had, but what they want to build going forward.
At InfinityQS, we understand that we all face some challenging and tumultuous times ahead. But we face them together. For the days and weeks to come, we wish all our manufacturing colleagues the very best. Feel free to visit our website to learn more about how our software solutions can help your organization in immediate and practical ways. Stay safe—and let us know how we can help you.
Add new comment