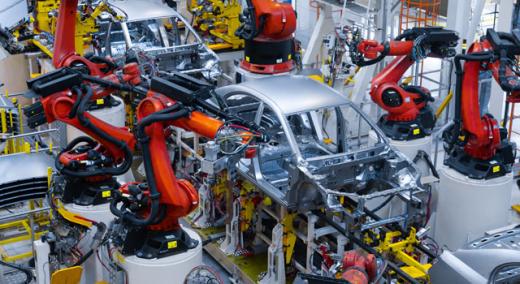
Corrective action and preventive action (CAPA) is probably the most important process in any quality management system because so much else depends on it. This includes not only its traditional role as a response to defects, nonconformances, customer complaints, and audit findings, but also outputs of the management review. It can even address all seven Toyota production system wastes if we redefine as a “nonconformance” any gap between the current state and a potential or desirable future state. AIAG’s CQI-22, Cost of Poor Quality Guide1, recommends that we compare “the ideal state for how work processes should perform” against “the current reality.”
ADVERTISEMENT |
Inadequate CAPA is a leading source of ISO 9001:20152 and IATF 16949:20163 findings, and FDA Form 483 citations.4 “Five Signs Your Company Is in Dire Need of Root Cause Analysis and Corrective Action Training” reinforces this point even further.5 While ISO 9001:2015 doesn’t have a specific requirement for preventive action, one could argue that clause 6.1.1 (c), “prevent, or reduce, undesired effects,” constitutes an implied requirement.
…
Add new comment