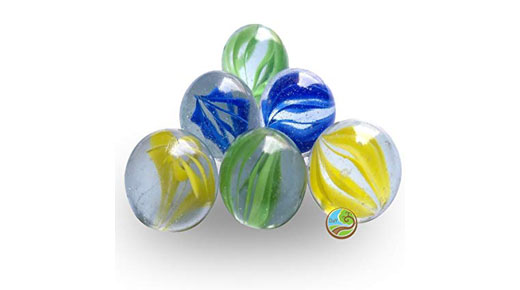
Implementing 6S, the lean strategy for reducing waste and optimizing efficiency in a manufacturing environment, is more than just creating work protocols that people must follow. Because that’s the thing about people: If they don’t know the “why,” they are less likely to buy in to any initiative, especially one that requires significant changes in the way they work and think, simply because they “must.”
ADVERTISEMENT |
Building a culture around 6S is the key to preventing it from becoming the latest flavor-of-the-month workplace initiative. But the question is, how? It turns out, the answer is right in front of you.
What is 6S?
Don’t be fooled by the new name. Like 5S, 6S is a system of workplace standardization and organization that originated in Japan. Its purpose is to create a clean and well-ordered workplace in order to minimize error and reduce waste. But, of course, there’s more to it than that.
…
Add new comment