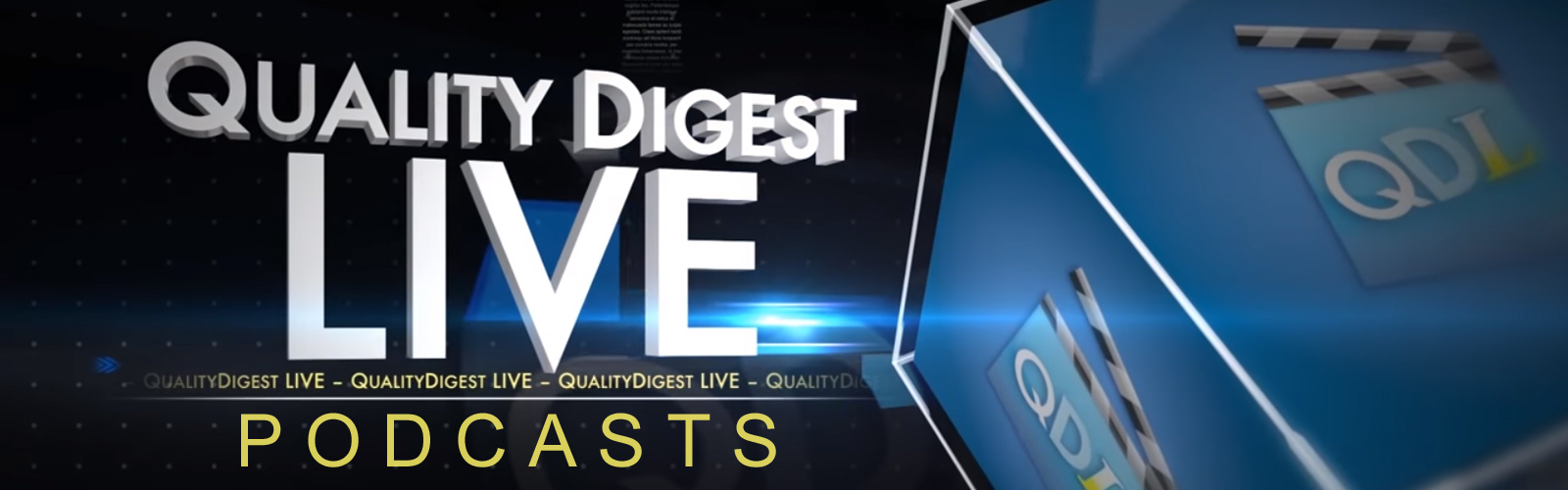
Most of us have heard of kaizen—continuous improvement of philosophy and methodology. In business, this involves all employees working to improve a company's processes to lean it out, to run with less waste. But most of us who are familiar with kaizen think of it as something you do.
Especially, we think of kaizen as something you apply to an existing operation or process, or in terms of mounting a “kaizen blitz.” We tend to think of it as is trying to fix something that’s already broken. But what if you applied kaizen principles before your organization was actually up and running?
“The ideal time to think about using kaizen, or continuous improvement, is really phase one, or the feasibility study of construction or building out an existing manufacturing facility,” explains Dan Chartier, managing director of Kaizen Institute North America. “It’s important to get involved as early as possible in the project. This helps in assessing the efficiencies of the plan before it gets designed and constructed.”
The whole idea is to look at the intended facility layout to determine if it will yield efficient processes once constructed as envisioned.
…
Add new comment