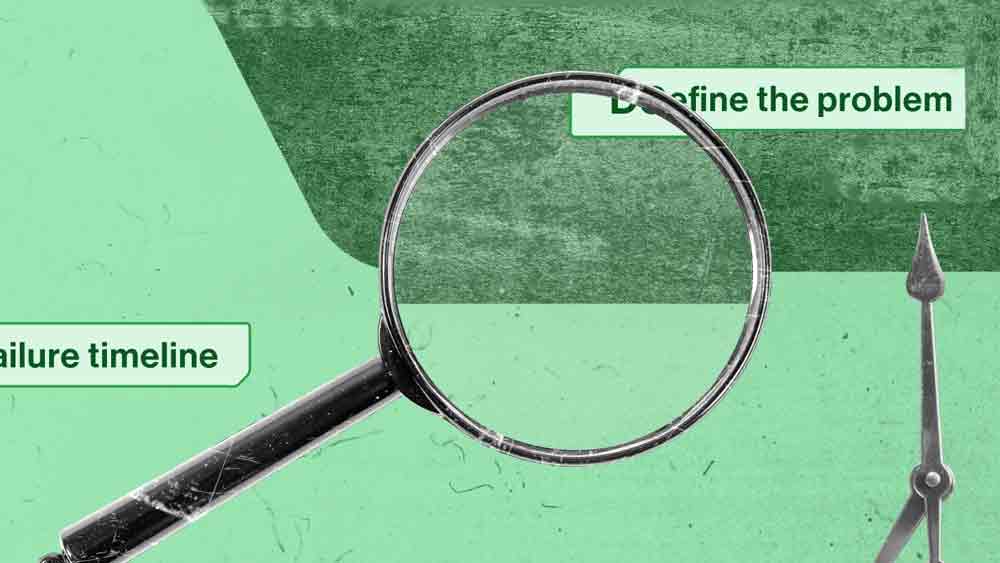
Failure analysis helps uncover the root cause of equipment issues so you can fix problems and prevent them from happening again. This guide outlines a clear, six-step process to conduct effective failure analysis and write a report that adds long-term value.
ADVERTISEMENT |
Failure analysis techniques vary widely based on the specific use cases. That being said, steps for conducting failure analysis follow the same pattern.
Step 1: Define the problem
A well-defined problem statement is essential for any deep analysis. Failure analysis requires engineers to define the problem as clearly and concisely as possible. The problem statement should contain details about:
• The failure that occurred
• The data that need to be collected
• The failure analysis technique to be used
• The expectations for the failure analysis (i.e., goals)
Step 2: Collect failure data
All relevant data have to be collected. This includes both quantitative and qualitative data.
Quantitative data refer to information such as operations data, maintenance data, and age of the machine. They can be obtained:
• From maintenance records
• From the CMMS database or any other tool used to monitor asset health and performance
• Through troubleshooting
• By performing a visual inspection (as a part of failure investigation)
Qualitative data can’t be easily quantified. Such data are obtained by interviewing machine operators, maintenance technicians, and operations managers. All relevant data concerning the failure should be collected.
Step 3: Create a failure timeline
Root causes result in a chain reaction that forms the surface-level failures we observe. The collected failure data can shed light on the event sequences that happened. With enough information, the team performing the analysis can create a failure timeline. This serves as a visual and mental aid to the analysis process.
Hopefully, the timeline will provide clarity into the cause-and-effect relationship between the events.
Step 4: Select useful data and discard the rest
The timeline created in the previous step is also used to identify useful data. Quantitative and qualitative data collected in Step 2 are mapped to the events in the timeline. The data that find a place in the timeline are useful for the final analysis.
The rest of the data can be discarded because they aren’t relevant to the events that caused the failure. This way, failure analysis teams won’t waste time and effort analyzing irrelevant information.
Step 5: Administer the chosen failure analysis technique
The next step is to conduct the chosen failure analysis technique. The method selected depends on the specific use case, industry, and the experience of failure analysis engineers conducting the analysis.
Step 6: Review results, test, and apply a solution
The result of failure analysis is studied in detail. In most instances, the purpose of failure analysis is to implement remedies that can prevent future failures. Different solutions proposed are tested, and the best solution is used to improve the system/machine.
How to write your failure analysis report
After you’ve done the analysis, it’s time to write the report. While administrative work is nobody’s favorite job, documenting used procedures, tested solutions, and found conclusions can be extremely useful for future failure analysis.
How exhaustive your failure analysis report is going to be will depend on the type and scope of the analysis you are performing.
For example, an in-depth field failure analysis performed after a product recall needs to have very detailed documentation. In this case, it’s recommended to slowly gather documentation and records as you go through the process. Later on, you can ask all involved teams to send over what they have, merge it, and finalize your failure analysis document.
In stark contrast, for a quick analysis performed to analyze the breakdown of conveyor belt No. 3, a single-page report might suffice.
What to include in the failure analysis report
There’s no universal report you can follow, because every organization has its own procedures and goals.
We recommend that you use good old common sense. When someone looks at the report 15 months later while troubleshooting a similar problem, what information will make their job safer, faster, or easier? Of course, the purpose of the report and how “official” it needs to be will also affect its structure and things that need to be included.
In general, plan to cover:
• Introduction (why the analysis was performed, the scope of the analysis)
• Problem description (what happened, the chronology of events that created the issue)
• General information (who performed the analysis, failure analysis techniques, and tests used to gather data and analyze the problem)
• Findings (the root cause, as well as any other notable findings that might not necessarily be related to the initial purpose of this investigation)
• Recommendations for corrective actions; a good report should focus on solutions and prevention more than assigning blame.
This might still sound rather abstract, so let’s look at some templates.
Failure analysis report examples
A sample of a basic failure analysis report. Source: Inpaspages
More comprehensive failure analysis report form. Source: Dexform
You can find many other examples on the web by searching for “failure analysis report” and taking a look at Google’s “Images” section.
Key takeaways
Failure analysis is a versatile tool that has many purposes. It can be used to investigate past failures, understand failure mechanisms, and predict the modes of future failures.
There’s no “one size fits all” solution to conducting failure analysis. The technique selection will depend on the goal of the analysis, available resources, access to relevant data, and what the failure analysis team knows and prefers to use.
Published March 21, 2025, by Limble.
Add new comment