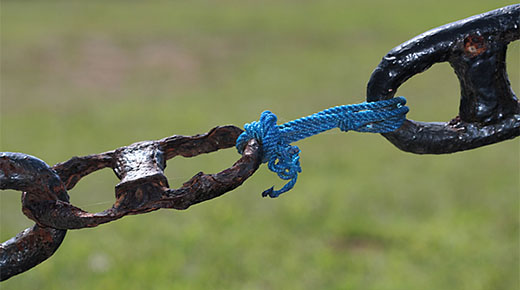
Body
I would like to share with you a tale from the real world. It’s an extract from the book Michael McLean and I wrote, Manufacturing Money (Amazon Digital Services LLC, 2015). It offers an example of the “Five Focusing Steps” to improvement, especially “Step 1: Identify the constraint,” and “Step 2: Maximizing the constraint’s output.” This was a situation where I looked at a problem for months before I finally figured out where the constraint was.
ADVERTISEMENT |
…
Want to continue?
Log in or create a FREE account.
By logging in you agree to receive communication from Quality Digest.
Privacy Policy.
Comments
Listen to what the machine is telling you
I suspect that the sound of the system also changed. It always is a good idea to become familiar with the sound of the system. A good operator will often become aware of a problem in his machine just by a subtle sound shift. In a former position, I had two major issues that were resolved by sound alone. In both instances, it was the "rhythm" of the system that was the clue. Every shop is a symphony and a critical ear can discern that one flat note or tempo error.
Sound
That's true. When you work in a shop long enough you know how it "sounds." If the sound changes, you might not know why it changed, but you know that something is up.
It's kind of like your car. You immediately know if it doesn't sound or feel right. A shop is just a car engine that you work inside of.
Add new comment