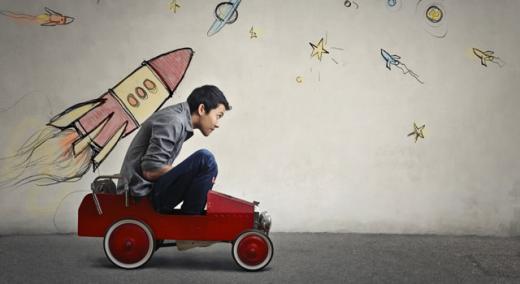
‘Why are our changeovers taking so long?”
ADVERTISEMENT |
If you’ve asked this question on the shop floor, more than likely you were met with blank stares by your employees. Open-ended questions like this are overwhelming, so employees try to find quick answers that don’t really address the problem. They don’t have a starting point to form an answer.
But what if you asked a question with a specific, achievable goal, such as:
“What steps can we take to reduce changeover time by 15 minutes?”
You’ve then provided your employees with a measurable goal in the form of a question. Your workers may feel empowered to answer with some hands-on suggestions for incremental changes, such as reducing setup steps or combining workstations. This in turn could not only reduce changeover time, but also significantly eliminate wait times and inventories.
This approach is often described as kaizen, or “continuous improvement,” which serves as the backbone for lean manufacturing. Kaizen uses the plan, do, check, act (PDCA) problem-solving cycle to encourage manufacturers to use small ideas to solve big problems, such as costly, time-intensive changeovers.
…
Add new comment