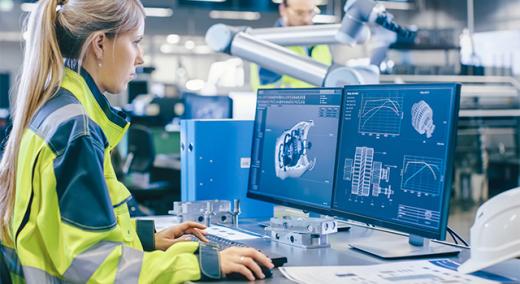
As we learned last month, the precision to tolerance ratio is a trigonometric function multiplied by a scalar constant. This means that it should never be interpreted as a proportion or percentage. Yet the simple P/T ratio is being used, and misunderstood, all over the world. So how can we properly make use of the P/T ratio?
ADVERTISEMENT |
The usual motivation behind the computation of the P/T ratio is a desire to determine if a measurement procedure is adequate for a given production process. And there are two ways that measurements support a production process: They can be used to scrape the burnt toast (inspection), or they can be used to learn how to stop burning the toast (process improvement). If the measurement system is adequate to allow us to improve the process, then we can often get to the point where we no longer have to depend upon inspection to ship conforming product. So, of these two ways that measurements support production, the role of process improvement is the more critical in the long term.
…
Comments
P/T and ICC
Actually, a good article.
1) It's a good basis to expand into using the Hotelling's T-square and multivariate QC. We tend to think in spec "boxes". Referring to your Figure with tthe ellipse: IF there is/are correlation(s) between two or more specs then the specifications should be based on the bivariate (or multivariate) distribution. Looking at the "box" specification region in your figure, and imagne a point in the upper left corner -- both specifications are "met" BUT, it is way off the line formed by the ellipse. The other case may be that the data values for x,y may be in the upper right corner and both values may be slightly outside the "square" specifications. Hence, the question about 'Acceptance' should be: Should I accept a product in the upper left corner (both specifications met, but way off the ellipse and the apparent line between the specs) OR the one in the upper right corner -- slightly OUT oF SPEC -- but well within the ellipse.
In other words, the one in the upper LEFT corner has an additional problem by being so far from the ellipse and the line formed by the correlated variables.
2) ICC. I used it as a first pass for gauge. Assume the variance of the final measurement is X, E is the variance of the measurement error, and T the product variance which includes all contributions such as operator-operator, test system-test system variance, etc. [(X = T + E)] . Then used the acceptance criteria you indicated for the ICC based on the measurment error E. If the gauge met your requirement -- accept and move on. IF not, of if you want, then can do the deeper analysis of the variance sources.
NOTE 1: Simulation: One can use a spreadsheet to simulate the total variance in the measurement (X). First set the "product" variance to 1 and set the Measurement Variance as a proportion to this -- kT -- where k can be varied from 0 (then X = T) to any value. Then X = T + kT = (1 + k) since T = 1. And then plotted the simulated variances of the final measurement 'X' versus "k".
What I found was the even with k ~0.4 the total variance in the final measurement was only about 10%! This is an alternate version of what you had been saying -- and reaffirms your suggestion that ICC ~ 0.8 should be considered acceptable -- and maybe we are overspecifying the gauge requirements based on the traditional methods.
NOTE 2: The Gauge capability should always be considered an 'experiment' and subjected to the routine of any DOE. Further, one should always review how the gauge is used in the process flow and adjust the requirements as needed. Maybe an ICC of 0.5 is ok at that specific point, because there are additional steps to catch the problem (and also may be cheaper to catch it later.)
--> The last issue of the AIAG standard I used was the 4th. Is the ICC method you propose being considered?
Thanks
Excellent article
I shared the link to this article on LinkedIn. Measurement systems analysis is an important subject, and it is not covered explicitly by ISO 9001. IATF 16949 is another matter as I recall.
Add new comment