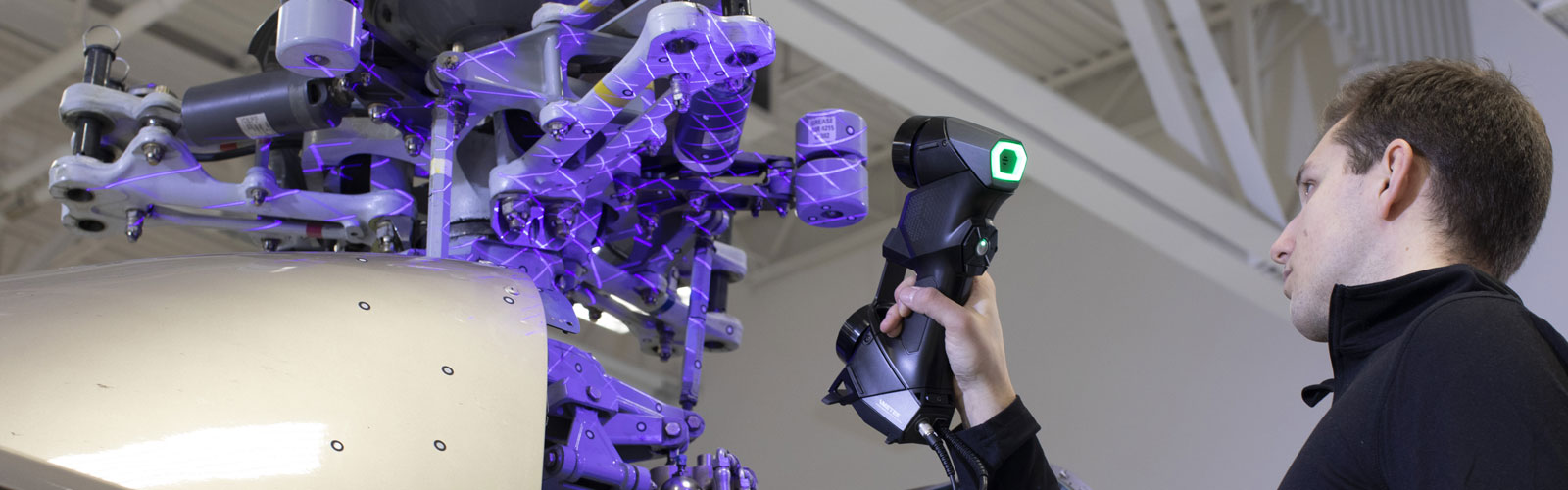
The aerospace industry is known for manufacturing parts with critical dimensions and tight tolerances, all of which must undergo demanding inspections. Given the scale of the controls to be carried out on these parts, it is hardly surprising that quality people in the industry prefer to turn to coordinate measuring machines (CMMs). However, directing all inspections to the CMM may cause other problems: CMMs are hyper-loaded and can generate bottlenecks during inspections, slow down manufacturing processes, and cause production and delivery delays.
Is it possible to unload CMMs so that they are fully available for the final quality controls? How can we improve manufacturing processes to produce more parts faster, and above all, of better quality? In the event of a quality issue occurring during production, is it possible to identify the root cause more quickly to minimize the delays that could impact schedules and production deliveries?
This article aims to explain how important players in the aerospace industry have managed to unload their CMMs and improve their manufacturing processes without ever neglecting the quality of parts with critical dimensions and tight tolerances, such as castings, gears, pump covers, stators, and bearing housings. Solutions developed by the aerospace industry can serve as a guide for other industries.
Challenges
Bottlenecks at the CMMs
Aerospace companies, and many other industries, require that manufactured parts be inspected with a CMM because they have full confidence in the accuracy of its measurements. This exclusive trust, however, creates certain challenges. Indeed, the CMM is a highly accurate metrology tool that is often used to inspect noncritical dimensions, leaving little availability for final inspections and important dimensions. Therefore, quality controls are delayed due to these bottlenecks at the CMMs. Moreover, the CMM is a measuring instrument that requires a specialized workforce to build and execute the programming. If the company does not have the human resources to do the inspection programs, the parts will accumulate as they wait to be inspected. Buying more CMMs will not solve the bottleneck issue; what is needed is the specialized manpower to operate them. But that is not easy to find these days.
Quality problem detected at the end of the manufacturing process
Too often, manufacturing companies wait until the end of the manufacturing process to perform quality controls on manufactured parts. Not only are critical dimensions inspected at the CMM, but also all other dimensions, which lengthens the process and often results in delivery delays. What happens if a quality problem is detected only at the end of the manufacturing process? The quality assurance team must then go through the whole process to investigate and find the root cause. This analysis may generate downtime and production delays, which will impact the part delivery and customer satisfaction.
Solution
Incorporate an alternative measurement method to detect quality problems faster
Rather than inspecting all dimensions at the CMM, which requires long programming time and involves qualified resources, the aerospace industry uses a faster and simpler alternative measurement method to inspect less critical dimensions. This alternative method is a metrology-grade 3D scanner called the HandySCAN BLACK, which is produced by Creaform, an ISO/IEC 17025-accredited company.
Metrology-grade 3D scanner
The HandySCAN BLACK excels due to its scan quality, accuracy, and measurement reliability. The HandySCAN BLACK has an accuracy of 25 μm and is in compliance with German standard VDI/VDE 2634 Part 3. Using a safety factor of 5X (i.e., five times more accurate than the smallest tolerance to be measured), the aerospace industry uses the HandySCAN BLACK for inspecting features with tolerances starting at 125 μm (5 × 25 μm) or more.
Speed
With its 11 blue laser crosses, combined with high-resolution cameras and custom optical components, the HandySCAN BLACK can perform up to 1,300,000 measurements per second in addition to generating an automatic and instant mesh. This means that, unlike a cloud file, the generated mesh is already lightened and processed, which reduces the need for data filtering and lessens the variability on data processing. Thus, the aerospace industry retains the same confidence it has in a CMM because the data obtained with the HandySCAN BLACK are consistent and repeatable.
Portability
Because the HandySCAN BLACK is a portable device, it can be moved to any stage of the manufacturing process to perform an intermediate check without having to move parts. For example, it allows a pump to be inspected before machining to ensure that there is enough material, as well as after machining to validate that the dimensions are accurate. The HandySCAN BLACK can also be used to check the dimensions of gears before and after their heat treatment. Only a portable metrology tool enables quality and production teams to perform these intermediate checks quickly and easily during the manufacturing process.
Benefits
Unload the CMMs for the final quality controls
CMMs will always be the preferred measuring instruments for final inspections. However, these highly accurate devices must be available to perform the final quality controls. In other words, they must not be loaded down by all kinds of intermediate inspections during the manufacturing process, or by various investigations while troubleshooting production issues. This is precisely what the HandySCAN BLACK is doing for the aerospace industry: unloading the CMMs by diverting less critical inspections to an alternative measurement tool. One in-house survey quantified that 50 percent to 90 percent of the dimensions could be measured with the HandySCAN BLACK, allowing the CMMs to be available and used to their full potential and full accuracy for critical dimensions with tighter tolerances.
Improve manufacturing process
The more often parts are inspected during their manufacturing process, the less tedious the final inspection will be. Indeed, if the parts—whether pumps, gears, or casting—have already been inspected before and after their machining and before and after their heat treatment, the risk of detecting unexpected problems is lessened. The final inspection on the CMM, now widely available, will serve only to control the critical dimensions because all other features will already have been validated during the manufacturing process. These intermediate checks, performed during production not only accelerate the manufacturing process, but also improve the quality of parts while producing parts in higher quantity. The same in-house survey quantified that intermediate checks with the HandySCAN BLACK improved the manufacturing process by 30 percent, either by producing 30-percent more parts during the same production time, or by producing the same number of parts 30-percent more quickly.
Find the root cause in quality assurance
Finally, the HandySCAN BLACK turns out to be the secret element to identifying the root cause of quality issues that arise during production. Because the scanner is accurate, fast, and portable, it can find the source of problems faster and minimize delays that could impact schedules and production deliveries.
Conclusion
The aerospace industry values the CMM for quality controls because of its high accuracy and repeatability. However, aerospace companies agree that the performance of the HandySCAN BLACK positions this alternative method as a must to optimize its manufacturing processes. This fast, portable, metrology-grade measurement tool is increasingly proving itself to be an indispensable tool for performing quality controls during the manufacturing process in order to unload the CMMs and detect problems more quickly. Both the CMM and the HandySCAN BLACK are valuable metrology tools for the aerospace industry, each having its dedicated applications and objectives.
Add new comment