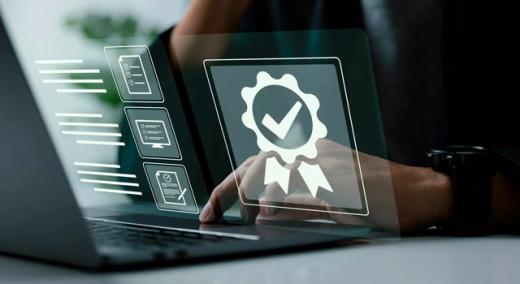
Mistakes around standard operating procedure (SOP) management are widespread and costly, especially given the pace of change in manufacturing today.
ADVERTISEMENT |
Consider, for example, an electronics manufacturer that introduces a new product model with updated features and components. This new model requires a specific voltage tolerance test for one of the new components, but the quality control SOP only covers testing steps for the previous model.
During assembly, an operator unaware of the new requirements performs the voltage tolerance test incorrectly. As a result, faulty products are shipped to customers, leading to defects, complaints, and ultimately, a recall.
This scenario highlights the risks of ineffective SOP management, and why manufacturers must regularly review and update SOPs to protect quality.
With that in mind, this article discusses common SOP management mistakes, best practices, and how an enterprise quality management system (QMS) can help you implement them.
Infrequent review is perhaps the biggest mistake manufacturers make when it comes to SOP management. Information and requirements can change throughout the product development cycle, making it essential to review SOPs regularly.
…
Add new comment