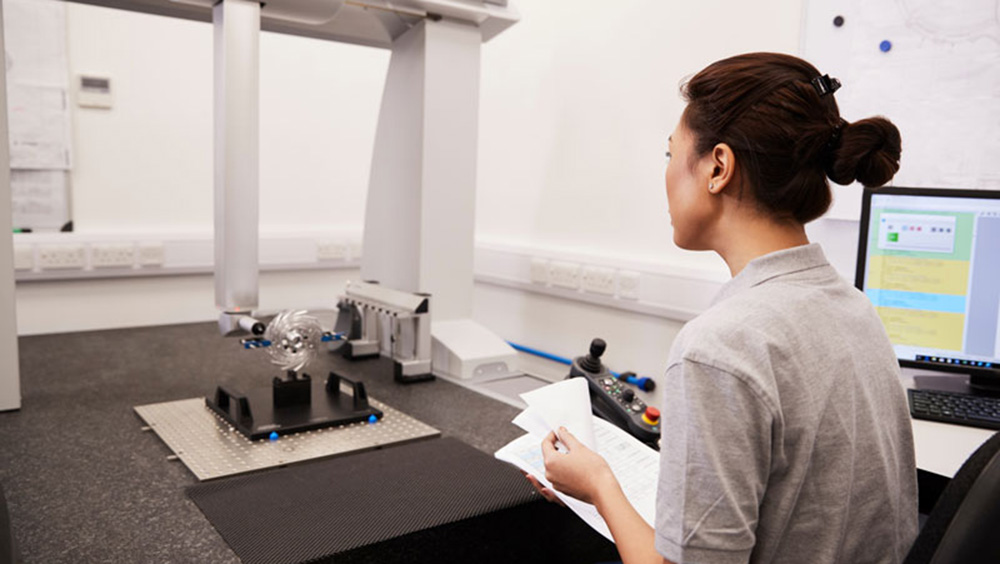
Credit: Creaform
Quality control (QC) teams need reliable results they can trust to make informed decisions and address manufacturing challenges. This is why they rely on the coordinate measuring machines (CMMs). However, a CMM’s speed is often a limitation, making the idea that routine quality control can be performed solely on a CMM more idealistic than realistic.
ADVERTISEMENT |
Reality: QC with a CMM is labor-intensive
Although CMMs are highly accurate, they operate slowly and require skilled operators for setup and use. This limits accessibility and efficiency, ultimately extending inspection times, especially for complex parts.
Reality checks with a CMM
Increased inspection time: Using the CMM for routine inspections can significantly extend inspection times, delaying production schedules and creating bottlenecks in the manufacturing process—especially when multiple parts are awaiting inspection.
…
Add new comment