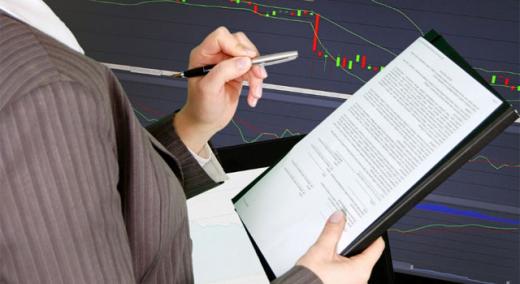
When a customer asks to see your layered process audit (LPA) documentation, will you be ready? For many manufacturers, the answer is no.
ADVERTISEMENT |
Instead of having proof of an effective audit process, many companies are left scrambling for data that show low audit compliance and few actual results. Unfortunately, poor audit processes are enough to fail a customer audit, which could put your key contracts at risk.
Make sure this doesn’t happen to you by taking a deeper look at your auditing practices from the customer’s perspective. To help you get there, we’ve put together a checklist of seven critical LPA mistakes to fix before your customer knocks on your door.
1. Lack of management participation
One common problem with LPAs is low management participation. Plant managers and other layer-three auditors should conduct monthly audits. Quarterly audits simply aren’t enough, and send a clear signal that you don’t have the right commitment to LPAs.
|
…
Add new comment