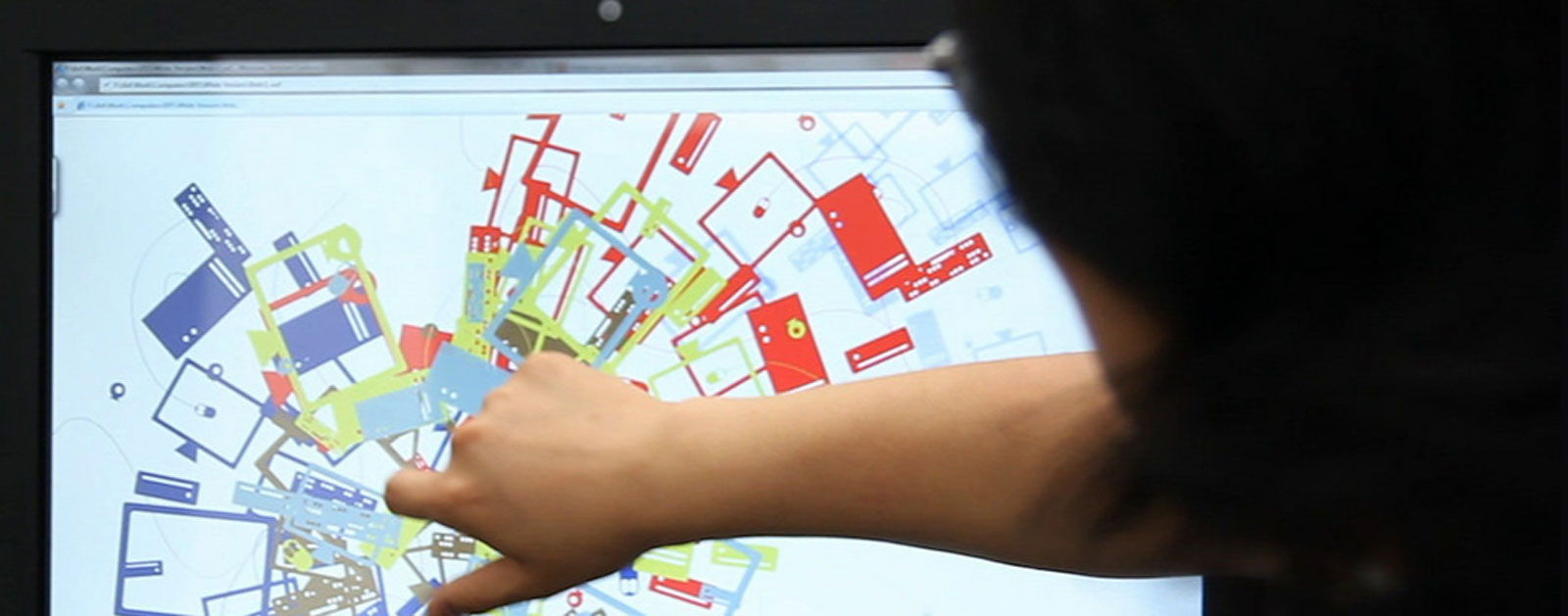
There’s a big problem for companies within industry these days: the inability to monitor statistical process control (SPC) in real time. This issue manifests itself in several ways, and its effects are filled with risk for enterprises of all shapes and sizes. However, practical solutions are available in the form of tools to help automate many of the manual processes currently being endured by too many companies.
This article offers a case study showing how one organization achieved this ambitious goal. Read on to find out what they did, and how, along with steps you can take to follow their example and achieve improved manufacturing outcomes for yourself.
The company
A global manufacturer of security devices consolidated and integrated four manufacturing sites into a single, purpose-built facility. The transition into the new facility offered a golden opportunity to modernize and fine-tune the facility’s quality control procedures.
Before moving operations, the company’s separate manufacturing facilities had relied on manual, pencil-and-paper processes and data gathering. The legacy systems didn’t provide real-time monitoring or quality control for the production lines. Investigating and mitigating issues required heavy reliance on manual data records and alerts from the floor operators.
Those legacy manual processes didn’t provide the flexibility to add internal specs for different customers or products, and operators had no real-time out-of-control spec alerts. Often, by the time someone noticed a process deviation, it was already too late, and a lot of product had to be scrapped.
To be responsive to quality demands and customer requirements, the organization needed access to real-time data.
The solution
The launch of the new site offered a rare opportunity to bring in new people, modernize technology, and improve processes—a chance to change the manufacturing company’s direction and culture. To garner management buy-in and ensure a successful rollout of the new quality management solution, site leaders decided to launch an automated data-collection and -analysis pilot program on one process. The first process to be transitioned was a core step that required collection of approximately 50 data points in each “batch” and balancing at each step.
The result
The application helped the team transform this highly concerning and poor yielding core process to one offering extreme consistency.
Automation enabled the standardization of a legacy process-area database and allowed the team to more efficiently sift the data it housed. Then, they expanded the solution to automate data collection across the process. From there, they integrated measurement systems, in-process collections, and end-process inspection. They now have live monitoring and end-to-end visibility across the entire process.
Other notable improvements included:
• A 24-percent reduction in scrap at finishing visual inspection in the first year
• A 32-percent reduction in operator variation
• Reduction in the time it takes engineers to generate analyses and reports
• Adoption of more paperless systems
The successful rollout has also helped create a strong, data-driven team environment, empowering line operators—and everyone else—to take part in improving quality. Operators and engineers throughout the enterprise can now control the process rather than questioning where the data came from. The team can also create standardization in procedures and disseminate those new standard operating procedures to the rest of operations.
And that solid, accessible data is a major proof point that has helped management understand the value of modernizing processes across the entire company. From the initial process area, the team is now rolling out automated solutions to a new line every few months.
The shift has given this manufacturing facility the opportunity to build a truly modern solution that can be reproduced successfully across the rest of the company—an outcome that is sure to continuously improve quality well into the future.
Discover how best-in-class tools can help you automate and unleash the power of SPC. Click here to register for the free whitepaper, “Moving Away from Manual Processes” |
Add new comment