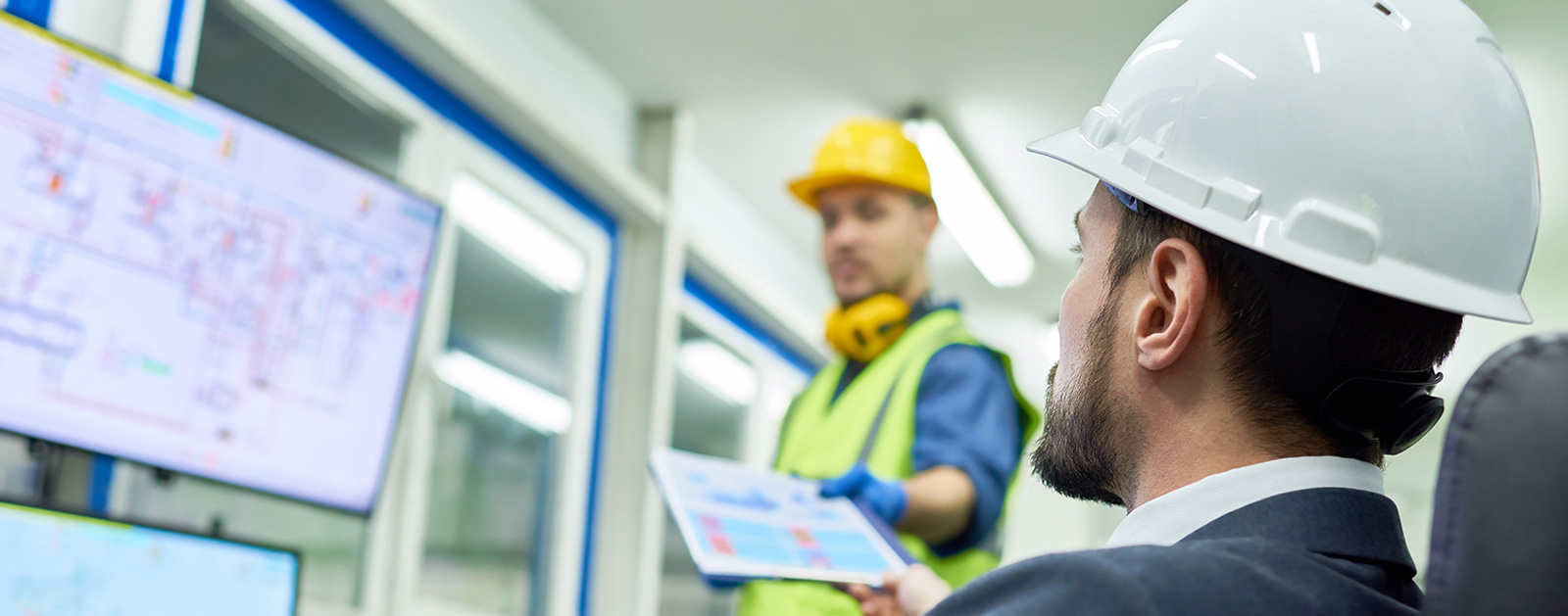
A few months back, I was reading a really good article from The Wall Street Journal, titled “Stop Using Excel, Finance Chiefs Tell Staffs.” Even though it was geared toward accounting and corporate operations, the message of the article struck home: Excel shouldn’t be used as an enterprisewide financial platform. That’s as true for the manufacturing quality world as it is for finance.
One quote from the article stuck with me. An executive working on cutting Excel out of the process at his firm stated “I don’t want financial planning people spending their time importing and exporting and manipulating data, I want them to focus on what is the data telling us.” And I thought, “That’s what manufacturing organizations need to start thinking.” Manufacturers need to stop juggling spreadsheets and paper and start focusing on the information that can be found in the data they collect.
Before Excel, there was paper. For decades, organizations in the manufacturing industry relied on paper for collecting and storing their quality data. And the practice continues today. I’ve heard reasons like “It’s cheaper to use paper” (it’s not, as I show below) and “It’s worked for us this long, we’ll stick with it” (that’s just a habit). It’s time for companies to modernize.
Your paper checklists might seem to provide more control for your operations staff. Or you may hate change (actually, we all do). In fact, the risks of paper-based data far outweigh the potential benefits:
• Data written on paper may be illegible or misinterpreted
• Data might be misread from the paper
• Numbers could be accidentally transposed
• The paper might be lost or damaged
• If transferring data from paper to an electronic system like spreadsheets, numbers might be misread or entered incorrectly
Money, money, money
The paper habit not only leaves you open to error, but it is also expensive. I once worked with a manufacturer whose quality system generated so much paper that they employed three librarians—one for each shift—just to manage it all.
Once the on-site library filled up, they’d pack it all up and ship it to their warehouse, where it was organized with the millions of other pieces of paper already there. Librarians, paper, warehouses, transportation, and more... you can see how paper systems can, indeed, be expensive. If you are using paper for collecting manufacturing and quality data, I’m here to tell you that you’re throwing money away, and you may not even know it.
Check out the Top 5 Benefits of SPC here. Find out how instantaneous feedback and actionable information from SPC can minimize cost of quality and prevent costly issues downline. |
And reporting is no picnic either
How do you generate summarized reports from paper-based systems? Well, first you’ve got to find the right paper with the right data on it. Just finding the right paper can be a huge challenge. But if you find it, cross your fingers and hope that you can read the data. If so, then you need to transfer the data to some other medium, such as spreadsheets. It’s a time-consuming, laborious process fraught with error.
If you don’t go through the drudgery of transferring paper-based data to another system for analysis, then the data is trapped. It is forever imprisoned on paper and unable to be used to benefit your manufacturing operations. Reporting shouldn’t be so difficult. But wait, there’s more. Paper is not the only problem, there are lots of issues with spreadsheets, too.
The problem with spreadsheets
At some point, organizations become tired of all the paper. When inundated with paper, there is naturally a push towards a more electronic means of data capture and analysis, usually involving spreadsheets.
Although spreadsheets are fantastic tools in many situations, they are unwieldy and challenging for operators and inspectors to work with. They are also very difficult to manage and organize. And when the time comes for monthly reporting, get ready for a headache because of how spreadsheet systems are typically organized.
Many companies I have worked with have organized their systems by placing data for a unique part number in a single spreadsheet. The conventional wisdom is that organizing this way makes it easy to find the files when data needs to be entered or evaluated.
But if a company makes hundreds or thousands of part numbers, then they will need to create hundreds or thousands of spreadsheet files. So, consider a manager who wants a summarized quality report for the plant, but only for the part numbers that were actually run in the current month.
How would you even know which part numbers were manufactured and which spreadsheets to access? And, what if that same manager wants to know which part numbers are generating the most problems, or summarize the percentage of all products that didn’t conform to specifications in the month? How would you manage this? Well, it’s ugly. Someone would need to open every spreadsheet, analyze the data, and then create yet another report file for the data.
Juggling spreadsheets is not just tough, it’s nearly impossible. And yet, the information contained within and across those spreadsheets is exactly what managers need to make informed, intelligent decisions about their operations.
The point here is that if you’re using paper or spreadsheets, then the critical information you need to better manage your plants is difficult to access at best. Worse, that information is unable to be leveraged for improvement. But there is hope.
![]() |
SaaS can help
A robust software-as-a-service (SaaS) SPC solution can simplify and streamline data collection, help you kick the paper habit, and eliminate all those spreadsheets. While doing so, SaaS products can make reporting simple, easily enabling data roll-up and summarization and giving you access to the information you need to manage and improve.
|
Modern data collection and analysis features
When you’re looking to break from paper, make certain that the software you use to collect data has the flexibility to mimic data collection on your shop floor. What I mean is this: It should be configurable enough to support data collection the way operators expect to collect data.
Your SPC software should make data capture much faster than when an operator writes on paper. And it should allow operators to easily enter traceability fields, quality data, and other information found on paper forms and spreadsheets—while automatically noting the time, date, shift, and operator name.
|
With a SaaS system, reporting should also be simple. Look for the ability to summarize information across part numbers, production lines, plants, and regions. Those reports should be easily accessible and powerfully communicate summarized information that you can use to take action, reduce defect levels, and improve profitability across your enterprise.
In closing, spending money on paper and spreadsheets is throwing good money after bad. It’s no way to manage a quality system. It doesn’t work for Wall Street, and it sure doesn’t work in manufacturing.
Look for software that has a simple, friendly, and intuitive interface, data-collection flexibility, and powerful data summarization features to help you transform your company’s quality performance. Visit the Enact page on the InfinityQS website and see what I mean.
Add new comment