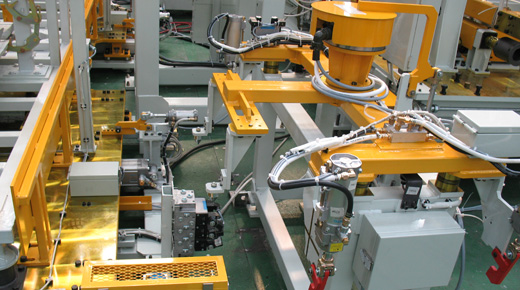
Equipment downtime gets expensive fast in automotive and aerospace manufacturing, a risk many companies try to mitigate by storing spare parts onsite. A machine breaks down, haul out the parts, and hopefully you’re back in business with minimal disruption.
ADVERTISEMENT |
The problem is, manufacturers get so wrapped up in hitting production targets that they don’t stop to ask why the machine went down in the first place.
The result? The equipment goes down again, whether two days, two weeks, or two months later, causing additional downtime because the “corrective” action was never designed to last.
To avoid backsliding after corrective action, companies must adopt a more proactive approach. A prevention focus, more frequent checks, and cross-functional collaboration can help, but only if management is willing to move beyond short-term solutions.
An ounce of prevention
The biggest reason corrective actions aren’t sustainable over time is because they aren’t real solutions to begin with: they’re just band-aids. Two of the most common mistakes in this category are blaming problems on operator error and stopping at containment.
…
Add new comment