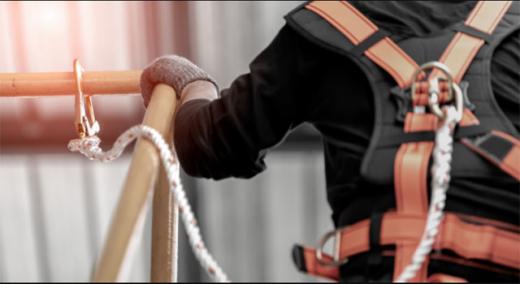
Safety managers have a multitude of safety strategies to protect the health and safety of their workforce. Guidelines for personal protective equipment (PPE), lockout/tagout (LOTO) programs, fire exit signage—the list is endless. However, to get the most out of your employees and resources, companies must look at all aspects of the organization that affect safety. Indirect ways of improving safety on the plant floor are often overlooked, and a missed opportunity.
ADVERTISEMENT |
Employees tend to do their job well when they have a solid safety culture. Research suggests about 49-percent more accidents and 60-percent more errors happen when employees are disengaged, and safety is less of a priority. This results in lower production, profitability, and career growth.
Does your supervisor acknowledge you on your job when you point out safety risks or suggest improvements? Does your company reward its employees when they have proven their excellence when it comes to safety? If the answer is “no,” then your company's safety culture has room for improvement.
…
Add new comment