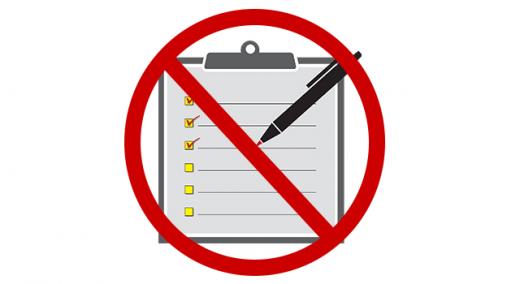
Do layered process audits drive real improvement in your organization? Or are they just another hoop to jump through for customers like General Motors and Fiat Chrysler?
ADVERTISEMENT |
A layered process audit (LPA) is composed of quick checks of high-risk processes. LPAs can prevent defects by identifying when people aren’t working to standard. Although each audit lasts only about 10 minutes, they also take place daily, creating an administrative burden that leads many manufacturers to simply treat them as busy work.
This “check the box” attitude creates its own avalanche of problems.
Completion rates are low, delivering little data. People pencil-whip audits, passing every item blindly—a problem for nearly half of respondents in our State of LPA survey. Completed checklists become an overflowing pile of unfinished paperwork, waiting for someone to enter and analyze the findings. When auditors do uncover problems, they may not receive the proper follow-up, sending the message that management doesn’t actually care.
…
Add new comment