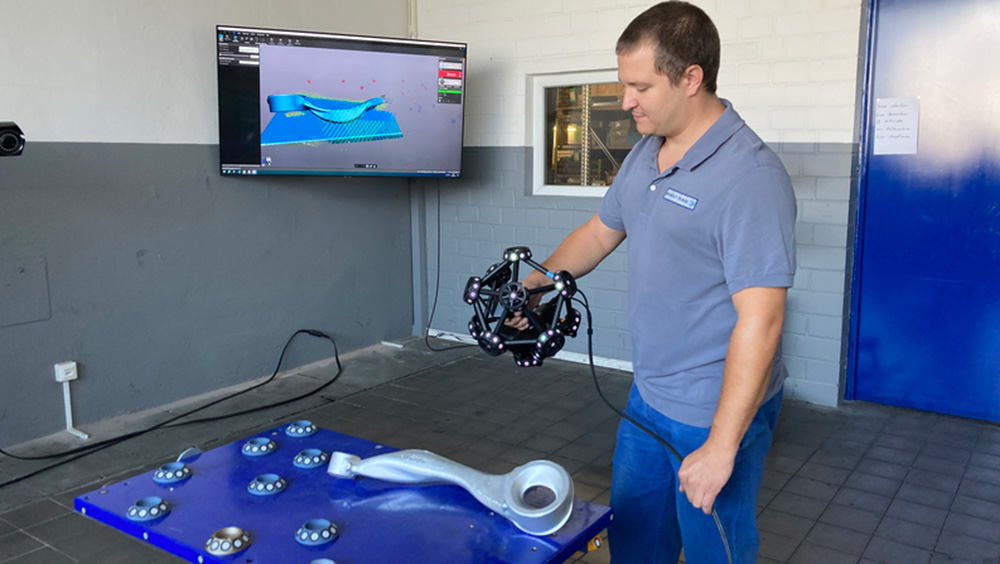
Bharat Forge CDP Gmb employee uses the MetraSCAN 3D optical CMM scanner to capture 3D measurements on a metal part.
For 185 years, Bharat Forge CDP has been a hallmark of expertise and craftsmanship in metal forging and forming. The German company is known worldwide as an innovative leader and trusted supplier to a wide range of industries, including automotive, rail transportation, and mechanical engineering sectors. As a manufacturer of chassis components for passenger cars and commercial vehicles, Bharat Forge maintains the highest standards of safety, precision, and innovation.
ADVERTISEMENT |
The challenge: Outgrowing traditional 3D measurement methods
With its long-standing tradition of being ahead of the curve in metal-forming and forging technologies, the company decided it needed to invest in new solutions to proactively meet customer demands.
“As a supplier of safety-critical components, we must measure parts multiple times throughout the production process to ensure the utmost quality and comply with project specifications,” says Florian Heimbeck, inspection planner of metrology at Bharat Forge. “We simply can’t afford inaccuracies or delays in our 3D measurement processes.”
…
Add new comment