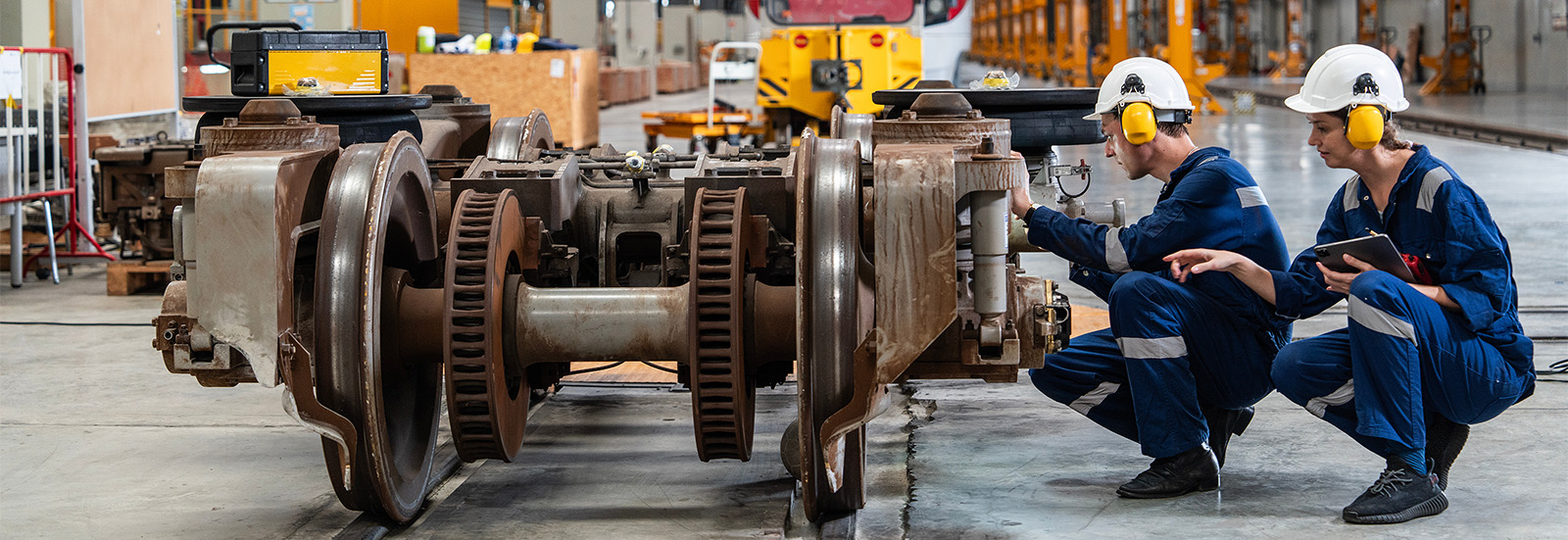
Quality control workflows are only as effective as the machinery they rely on. Ensuring functionality requires understanding what to test and how to measure these factors. Consequently, choosing appropriate material testing equipment is a crucial—if overlooked—step in the quality assurance process.
The importance of thorough material testing
Many professionals think of quality testing in terms of end-of-line equipment. While final product inspections are a critical part of thorough assurance, reliable testing begins with the raw materials. Rising costs impact 85.7% of American manufacturers, so facilities must use these resources carefully to minimize waste and keep expenses manageable.
Failing to catch flaws in materials before production means that even if end-of-line tools highlight defective products, waste has already occurred. However, finding issues earlier lets you avoid building something from subpar resources, preventing this waste and the related costs.
Testing resources before production is also vital to ensuring suppliers are reliable. Repeated issues may suggest you need another source to maintain high standards, and such improvements are only possible when you can recognize the need to change.
How universal testing machines improve material testing
![]() Thwing-Albert’s QC-3A UTM upholds the standards of the quality control line while adding the functionality of an RS-232 interface, a digital load controller, and enhanced software. Ideal for tensile, compression, coefficient of friction, and peel analysis, the QC-3A is a flexible, cost-effective testing system. The single-screw frame provides up to 1,100 lb (5 kN/500 kg) tensile force with extremely accurate control throughout the entire load range. The digital load controller ensures accurate, reliable test data. |
Making the most of material testing starts with understanding the types of equipment available. While such assets come in many forms, universal testing machines (UTMs)—like those from Thwing-Albert Instrument Co.—typically offer the most value. Using a UTM over single-purpose tools offers several important advantages for manufacturers.
Versatility
As the UTM name suggests, the equipment performs a wide range of tests within a single asset. Thwing-Albert’s UTMs can measure tensile strength, puncture resistance, compressive strength, flexibility, the coefficient of friction, and more.
Which specific tests a UTM includes can vary between models and original equipment manufacturers (OEMs). However, all cover multiple areas, especially the most commonly tested characteristics, like tensile and compressive strength. Many are also modular, allowing you to customize capabilities to suit the tests most relevant to your needs.
Testing requirements and material types can vary widely between products, so supporting all variations in the same machine helps manufacturers remain productive while increasing flexibility. It also reduces costs, because one piece of equipment can replace multiple alternatives. Single-station machines account for 17% of total manufacturing spending—more than any other equipment category—so this consolidation can yield considerable savings.
Test data reliability
UTMs’ versatility also results in more reliable material testing data. Many conventional alternatives measure just one characteristic, but product design must almost always consider multiple factors.
Analyzing a material across a wider range of criteria results in more comprehensive insights about its reliability. A piece of metal may have strong tensile strength, but if its coefficient of friction is too low, it may still be unsuitable for some moving parts. Several traits must be considered to determine a resource’s quality, and UTMs enable you to do so.
Performing multiple related tests can minimize measurement errors, too. Consequently, using a UTM gives you additional confidence in your QA’s reliability.
User friendliness
Modern material testing equipment is often highly automated, and UTMs are no exception. However, even a largely automated measurement requires a human worker for setup, initiation, and interpreting the results. As such, user friendliness plays a significant role in efficiency and accuracy.
UTMs are generally more user friendly because they reduce individual steps within a workflow. Instead of learning how multiple tools from varying OEMs work, employees must only understand one. Similarly, there is only one setup process for several testing types, reducing time spent and the likelihood of errors.
Quality concerns aside, between 70% and 90% of workplace accidents stem from human error. When such mistakes are less likely due to consolidated, more automated equipment, you’ll have fewer injuries and disruptions.
Efficiency
A high-quality UTM will also promote efficiency through these other advantages. Consolidating multiple testing phases into one asset reduces time spent switching between machines. Likewise, UTMs’ user friendliness leads to fewer error-related bottlenecks or delays from lengthy training.
Of course, not every UTM is equally efficient. In general, the more processes a solution can perform in a single pass, the more significant its impact on productivity. However, testing functionality is not the only concern.
A UTM’s software and usability are also worth considering. A highly functional but difficult-to-learn solution will have limited efficiency benefits. Similarly, the equipment’s data collection and reporting software must also consolidate multiple functions to maintain higher production speeds.
Additional testing tools and accessories to consider
Even the best material testing equipment is better when you use it with the right complementary systems. For example, grips and fixtures vary in effectiveness, depending on the types of resources you test and the kinds of analyses you perform. A reliable provider like Thwing-Albert can supply and support multiple variants to help you meet a wider range of needs.
Because UTMs are best when inspecting materials for multiple products and workflows, you likely need several of these accessories. Consequently, leading UTMs support different types, including pneumatic and mechanical grips. Modularity is also ideal, because it enables quick tooling changeovers when necessary.
Accompanying testing software can also be advantageous. Compatible software should streamline data collection and reporting, and automate much of the testing and documentation process. In addition to mitigating errors, automation helps address the 622,000-worker labor shortage manufacturing currently faces.
Sample cutters and other preparatory accessories are often necessary, too. These solutions ensure all samples heading to testing are consistent and meet your specific needs while keeping the overall workflow efficient.
Some UTMs include cutters and similar preparatory tools within the asset. These options are often a better deal, because they further consolidate work lines and minimize switching between machines.
How to choose the right material testing equipment
Selecting the optimal material testing tools is largely a matter of understanding what you need. Start by outlining the specific materials you test, the standards you must meet, and which factors you must measure regarding those benchmarks. Then you can understand which UTM best suits your goals.
What specific factors you need depends on the resources you’re testing and the purpose they’ll serve. However, the best UTMs are typically those that cover as many measurements as possible. Even if you don’t need some testing types now, conditions may change in the future.
When comparing OEMs, look at the industry standards they comply with. A versatile UTM must comply with multiple standards or regulations because there is a wider body of test types to consider.
Some companies—like Thwing-Albert—also provide installation and maintenance services. These may not be necessary but can keep costs manageable and ensure maximum uptime. A UTM may cost more than other, single-purpose equipment, so it’s often worth it to take on these additional services to get more out of your investment.
Reliable quality control starts with the right testing equipment
End-of-line quality inspections are essential, but testing raw materials before use is just as critical. The way to make the most of this process is to understand what material testing equipment is available and how to use it to meet your needs. Partner with a reliable UTM vendor today to prevent product defects while maintaining efficiency.
Add new comment