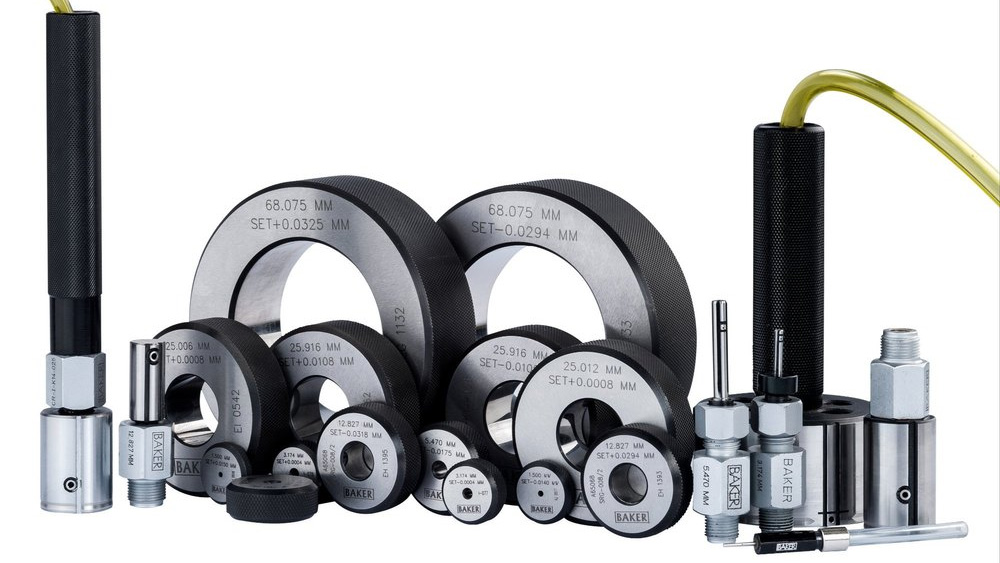
Examples of air plug gauges from Baker.
The jet in pneumatic dimensional (or air) gauging is the mechanical part of the sensing probe—air plug gauge, air ring gauge, air caliper gauge—through which compressed air is directed onto the part under measurement.
ADVERTISEMENT |
In its simplest form, we have two jets working in tandem facing in opposite directions (180°) to each other. Two are required to maintain a balance and to direct the air so that it impinges equally on the part surface. The back pressure created between the sensor and the part surface tells us whether the surface is farther away or nearer than required, i.e., whether the part is within its tolerance in comparison to a master part measured on the same equipment. The jets need to be central to the diameter. This is achieved by the jets’ placement in the body, which acts as guide. The central position is important to the accuracy of the gauge.
…
Add new comment