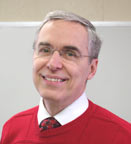
You manufacture a part that must be within design tolerances to work properly, so you need to measure it. It costs to:
- Buy the measuring device
- Provide a space and/or utilities for it
- Develop fixtures or part-holding accessories
- Make sure people are trained to do the measurements
- Develop a system for collecting and analyzing the measurement data
- Schedule service and maintenance of the measuring device
- Arrange routine calibration
These costs are then amortized across all the parts that go through this measurement process. Like any process step, there is an associated cost. Even parts sitting in a bin waiting for the next process incur costs—inventory costs, in this case. With so much emphasis on cost reduction, it might be tempting to do away with the measuring process completely. What are the risks?
Don’t do it!
A knee-jerk reaction might be to skip the measurement step and take your chances. Machine tools are very accurate. If the part is set up properly, it should come out as expected. Or take the minimalist approach—mic the part while it’s on the machine tool (use a micrometer, an inexpensive hand gauge to measure a diameter). Close enough might be good enough.
…
Add new comment