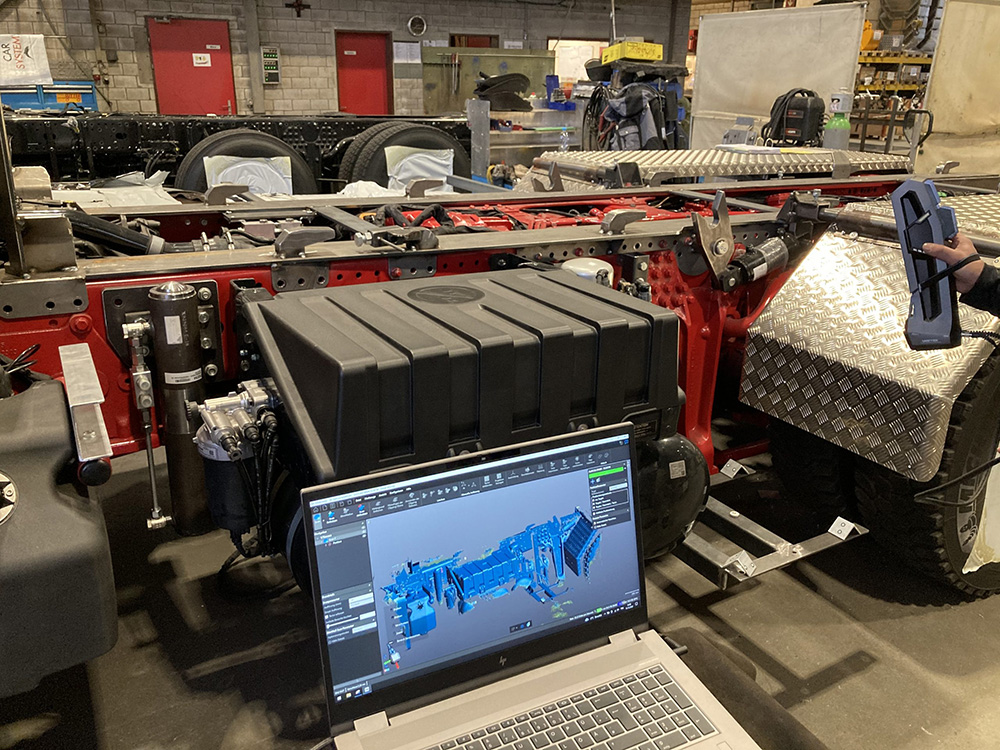
What started out in 1928 as a blacksmith and carriage smithy is now, 94 years later, a modern, customer-focused vehicle manufacturing company in the heart of Switzerland. These days, Sutter AG Lungern Fahrzeugbau specializes in the development and manufacture of three-side tippers of up to 40 tons, loading bridges for all trucks and vans, box bodies, tipping bodies, quick-change systems, special vehicles, as well as maintenance and repairs of bodies and trailers.
ADVERTISEMENT |
Before purchasing the Creaform 3D scanner, engineers at Sutter spent about 5% of their working time manually measuring certain components with complex geometries to fit them to vehicles. These are mainly aluminum covers, underride guards, crane-mounting elements, and other vehicle-mounted components tailored to the vehicle’s requirements or the customer’s wishes.
…
Add new comment