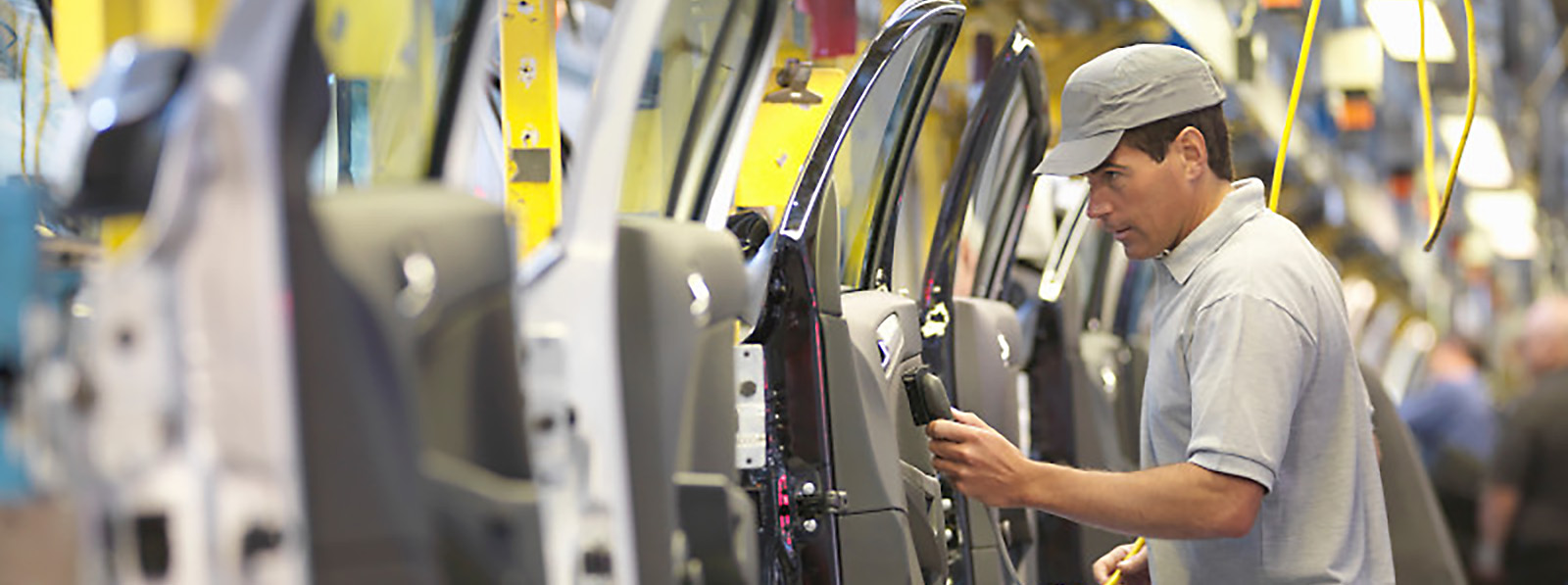
Knowing how to prepare for the certification process is essential. Credit: NSF
In a competitive manufacturing industry, meeting high standards is crucial to quality, sustainability, and safety. While it can be challenging to earn customer trust and establish a positive brand reputation, third-party certifications to standards such as IATF 16949: Automotive Quality Management System, ISO 9001: Quality Management Systems (QMS), ISO 45001: Occupational Health and Safety Management System (OHSMS), and ISO 14001: Environmental Management System (EMS) can help. Independent, third-party verification of an organization can help globalize operations and increase an organization’s competitive advantage.
ADVERTISEMENT |
Earning certification usually isn’t difficult for manufacturers that already run efficient and successful businesses. But knowing how to prepare for the certification process is essential. Knowing where to start, how to prepare, and how to integrate the practices beyond the certification audit process helps ensure a smooth process. By passing certification the first time and not needing a follow-up audit, manufacturers can more quickly prove the quality of their product and process to a wider market and earn lucrative deals.
Navigating multiple certifications
To take advantage of all the benefits that come from third-party certification, many organizations may want to earn multiple certifications to meet different management system standards. However, it can be overwhelming to decide which one to start with. It’s recommended that most manufacturers start with ISO 9001, and if they’re an automotive manufacturer, they should earn both ISO 9001 and IATF 16949. These both focus on quality management and consistency, proving first-class manufacturing practices.
Once manufacturers have become certified to ISO 9001 and IATF 16949, focusing on environmental management and occupational health and safety are great next steps. ISO 45001 and ISO 14001 help verify a business’s safety and sustainability while operating. All four of these standards are beneficial when striving to minimize risk, reduce overall costs, and increase a competitive advantage in the marketplace.
As manufacturers achieve certification, one thing is clear: Companies running sound business practices find the requirements for these standards achievable. Certification, therefore, acts as a validation of a robust system already in place, adding a powerful endorsement of quality and commitment.
Identifying gaps and building strong processes
It’s beneficial for manufacturers to familiarize themselves with the certification requirements of the standard they seek. When preparing for certification, a gap analysis of the standards sought can be a valuable tool for manufacturers to evaluate whether their current processes meet certification requirements, and areas that need improving before their audit. Specifically, they can use a gap-analysis checklist to stay organized and map requirements to their current processes. Missing elements or sections of the organization that don’t fully comply with requirements should be included as part of this exercise.
Running a gap analysis to the ISO 9001 standard requirements is helpful if a manufacturer is undecided on which certification to earn. It often serves as the foundation for the other standards, giving manufacturers an overview of their current standing.
To improve processes for the certification audit, manufacturers can take the identified elements that need to be adjusted and outline corrective actions with specific timelines and priorities. Regular team meetings will be beneficial to monitor progress before the audit date to ensure they’re fixed and compliant. For companies with robust processes already in place, this step can often illuminate only minor adjustments, positioning certification as an attainable next step.
While certification is a globally recognized way to demonstrate commitment to quality, it’s also an opportunity to refine operations to an international level through gap analysis. The automotive and industrial manufacturing industries may have voluntary standards, but the business impact is clear because efficiency and quality can be improved through meeting the standards’ requirements. Identifying the current state of processes and how they affect safety, environment, and quality is helpful as organizations begin to assess the areas of compliance they need to meet to earn certification.
Laying the foundation with team members
Policies and procedures are essential to creating an environment of safety, sustainability, and quality. However, creating and maintaining new processes requires a cultural shift to ensure that all team members operate under best practices outlined in the standards. To ensure this, which is imperative for audits, management must weave structure into daily operations. There are multiple ways to do this, including providing staff training, integrating best practices into the organization’s values and mission, offering incentive programs for team members who exemplify the standard, and having quality checks to ensure team members continue to operate at a high standard. A top-down approach will help shift a company’s culture and ensure that it continues beyond the initial certification audits. Whether an organization integrates one or multiple strategies to engage its employees, it’s critical to ensure that high standards for processes become a permanent part of an organization’s culture.
Competitive advantage in a crowded market
From competing for customers with global manufacturers to chasing the same talent, it’s increasingly difficult in the manufacturing industry to gain a competitive edge. Third-party certifications help manufacturers stand out across numerous categories, including customer satisfaction, market access, ESG, and efficient operations.
Customer satisfaction
Pursuing third-party certification demonstrates to customers that a manufacturer is proactive in achieving quality and excellence. Certification to standards like IATF 16949 and ISO 9001 verify that processes are in place to ensure that products meet quality requirements and consistently deliver that quality to the end consumer. This increases reliability to exceed customer expectations and improves customer satisfaction. As a result of higher trust levels, brand loyalty is built, enhancing reputation and attracting more customers.
Market access
Certification helps manufacturers earn global recognition, increasing market access and the ability to gain lucrative business across industries. This is particularly important for businesses operating in multiple regions. Certification is a requirement in some industries, like government, automotive, or manufacturing. Furthermore, certified manufacturers can be seen as less risky in supply chains than those without certification.
Sustainability and ESG
Organizations worldwide are striving for safer and more sustainable workplaces and products, making efforts in these categories nonnegotiable. ISO 14001 can help companies demonstrate and meet ESG goals that are presented to the board of directors, shareholders, and customers. It’s important for manufacturers to reduce their environmental impact to help meet stakeholder expectations and better attract business partnerships. ISO 45001 partners well with ISO 14001 certification because it demonstrates improved occupational health and dedication to employee well-being. This can help manufacturers reach quality and safety goals in addition to boosting team member morale and company loyalty to reduce employee turnover.
Efficient operations
To maximize profit margins, operating efficiently is imperative. ISO 9001 and IATF 16949 requirements help manufacturers operate at peak performance, reducing inefficiencies and waste. Maximizing efficiency helps organizations save money and optimize their resources to reach their organizational goals and commitments. Staying in line with regulatory and legal requirements is also necessary to reach these goals. Standards often align with legal requirements, helping certified companies avoid legal trouble that can come with safety incidents, environmental damage, or product failure liabilities.
From increasing customer satisfaction to improving market access, meeting ESG goals, and operating as efficiently as possible, industry standards help manufacturers across the board run the best business possible. Whether an organization decides to certify to one of the four core standards—IATF 16949, ISO 9001, ISO 45001, or ISO 14001—or all four in a cohesive strategy, certification demonstrates an organization’s unwavering commitment to the highest international standards in their industry.
Take the next step toward excellence
The choice to pursue certification shows customers and partners a proactive approach to excellence. Third-party certification is independent and objective, providing a credible evaluation of a company’s process and quality. NSF is a trusted partner in third-party certification, certifying companies to rigorous international standards. Certification demonstrates a manufacturer’s commitment to its management system as it meets elite international standards for quality, safety, and sustainability.
NSF offers manufacturers support in this process by providing a complimentary self-assessment tool to help manufacturers evaluate their readiness for certification. Following self-assessment, manufacturers can conduct a gap analysis or begin the process by requesting a quote.
Remaining competitive in a crowded manufacturing industry begins with building a culture of safety, quality, and sustainability. NSF will help you achieve more than compliance. With NSF as your third-party certification partner, you will strengthen your company’s position as a leader in quality and sustainability.
For more information on integrated management systems, or to discuss certification options, visit NSF’s website.
Add new comment