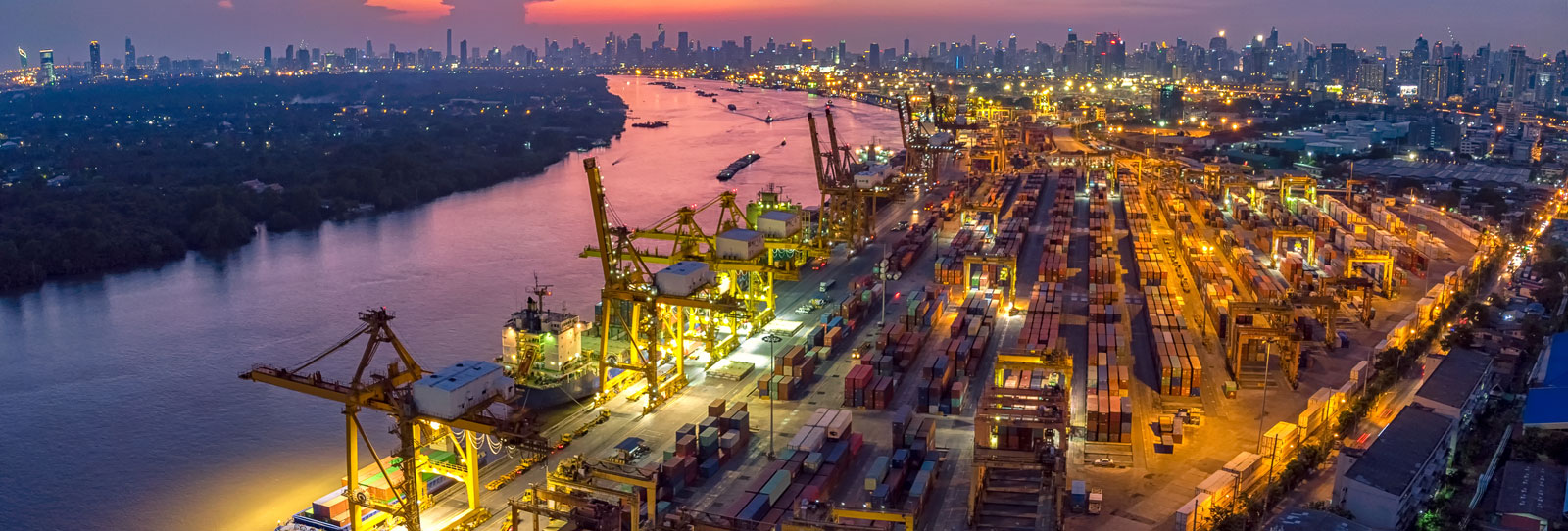
Has the automotive industry learned its lesson about supply chain disruptions? Or will delivery performance continue to suffer with every new disruption?
In addition to constant disruption, auto industry business models are rapidly transforming. Consumers are buying vehicles online. The transition to autonomous connected electric shared (ACES) vehicles is changing the way vehicles are designed, sourced, produced, sold, and utilized.
To succeed in this evolving marketplace, manufacturers must refocus their operations from manufacturing-centric to supply chain-focused. How?
Automotive supplier delivery performance, already susceptible to many internal and external disruptions, faces increased pressures rippling back from an accelerating pace of new vehicle technologies and rapid shifts in consumer demands. The automotive supply chain must be strengthened to ensure back-end supply chain processes become disruption-proof while aligning to support new vehicle-buying behaviors.
Suppliers must confront their shortcomings in delivery performance and consider process and technology improvements for competitive advantage, just as they embraced continuous improvement around quality and safety expectations.
Systemic root causes of poor delivery
How does the industry improve delivery performance? By confronting three primary systemic root causes:
1. Lack of supply chain process standards
Essential supply chain processes have not been consistently identified, nor have supply chain management requirements been adopted across the automotive industry. Supply chain-related processes traditionally have been viewed as nonvalue-added activities in manufacturing operations, and therefore tend not to be a focus for standardization and improvement. Quality and supply-chain functions often operate as silos. This leads to suboptimal results for the manufacturers as well as the overall automotive supply chain.
2. Lack of supply chain competency tools and training
Accumulated knowledge has been lost across the automotive industry during the past two decades due to retirements and workforce reductions, as well as diminishing interest among younger generations in pursuing automotive careers. This critical knowledge loss, especially related to supply chain management, prevents stabilization and improvement of key operational activities and hinders development of the next generation of automotive supply-chain professionals.
3. Low adoption of automation and advanced technologies
Applications of automated supply-chain processes and advanced technologies have not been adopted as a standard throughout the industry. Automotive manufacturers tend to apply their focus and investments on core manufacturing processes. This is a critical oversight as the industry shifts toward a consumer-driven model where value-add is defined as “the right product in the right place at the right time,” making supply chain processes essential for business success.
To achieve immediate and continuous improvements in supplier delivery performance—and align the automotive supply chain with a consumer-focused present and future—these systemic root causes must be addressed by the industry as a whole, as well as through changes to systems and structures within each automotive supplier.
Road map for improving the automotive supply chain
Toward that goal, a proposed five-step roadmap for improvement includes:
1. Identifying essential automotive supply-chain processes
2. Assessing current supply chain competencies based on these essential processes
3. Creating industry standards and related training to develop supply chain competencies
4. Promoting organizational adoption of a supply chain-focused operating model
5. Leveraging automation and advanced technologies to integrate supply chain processes for improved supplier performance
Here’s a quick look at two of the five steps in the road map:
Identifying essential supply chain processes
The key to future automotive supplyfchain success is to identify and manage the essential processes for sustainable delivery performance. A comprehensive review of MMOG/LE version 5 and IATF 16949 has identified 24 essential processes that will improve the performance of the automotive supply chain. Automotive suppliers should consider integrating these into their existing management systems for better supply chain outcomes. Although each of the 24 processes is applicable across all areas of operations, they align within five key business functions (see figure 1).
Figure 1: Five key business processes
Vetted by more than 20 automotive manufacturers—including OEMs, Tier 1, and Tier 2 suppliers—as well as several automotive industry associations, these 24 supply chain elements represent the key areas of concern regarding supplier delivery performance issues. Industry professionals also agreed that a shift to a more disciplined supply chain focus is needed, especially as the industry continues to face more global supply chain disruptions (e.g., pandemics, part shortages, geopolitical risks) and the move to electric and autonomous vehicle technologies.
Identifying essential supply chain processes also leads to better control of supply chain performance by monitoring key supply chain performance indicators. Typical supply chain KPIs such as on-time delivery and instances of premium freight represent process outcomes at the supply chain interfaces--for example, between OEMs and Tier 1 suppliers, and between Tier 1 and Tier 2 suppliers. However, they do not provide insight as to which supply chain processes are not functioning effectively. A May 2020 joint publication from ODETTE and AIAG provides an industrywide recommendation for standardized supply chain performance indicators (related to materials management and logistics) for production and service parts suppliers.
Industrywide adoption of these recommended supply chain KPIs would encourage automotive suppliers to define, measure, and optimize internal processes that contribute to these outcome metrics.
Leveraging advanced technologies
![]() Figure 2: Click image to enlarge |
To ensure sustainable, improved supply chain performance, especially as the automotive industry becomes more consumer-focused and the velocity of the supply chain activity increases, automating and integrating key business functions and processes is critical. Despite the availability of fully integrated ERP solutions, manufacturers tend to implement piecemeal solutions or develop in-house systems that can be myopic in their application, only addressing isolated business functions. This partial application of automation creates the need for interface activities, especially in supply chain planning, which often are filled by Excel spreadsheets or require interfaces to an enterprise resource planning (ERP) system.
The problem with incremental and manual solutions is that they are not in sync, up to date, or readily accessible by all functions requiring such data. Adopting a 360-degree enterprise view of the supply chain (see figure 2) provides real-time data across key business activities. Most important,enterprise ERP solutions provide virtual integration of these essential supply chain processes with related key business activities, leveraging data across functions for better risk management and decision making. A fully integrated ERP also provides the basis for adopting advanced technologies to improve the efficiency of essential supply chain tasks and facilitate the use of analytics.
Moving forward
With the rapidly changing landscape of the automotive industry due to new technologies and evolving consumer expectations, automotive manufacturers must develop robust supply chain processes that integrate seamlessly into their business systems.
The good news is that it’s not too late. The bad news is the clock’s running, and the next supply chain disruption isn’t far off. Global automotive manufacturers must take action now. For a detailed look at the proposed five-step road map and the 24 essential supply chain processes, read “Delivering on the Promise of Delivery: Part 2, Roadmap and Essential Supply Chain Processes.”
Organizations that succeed at defining and integrating these key processes systemically into their existing operations experience improved delivery performance, both incoming and outgoing in their business.
Add new comment