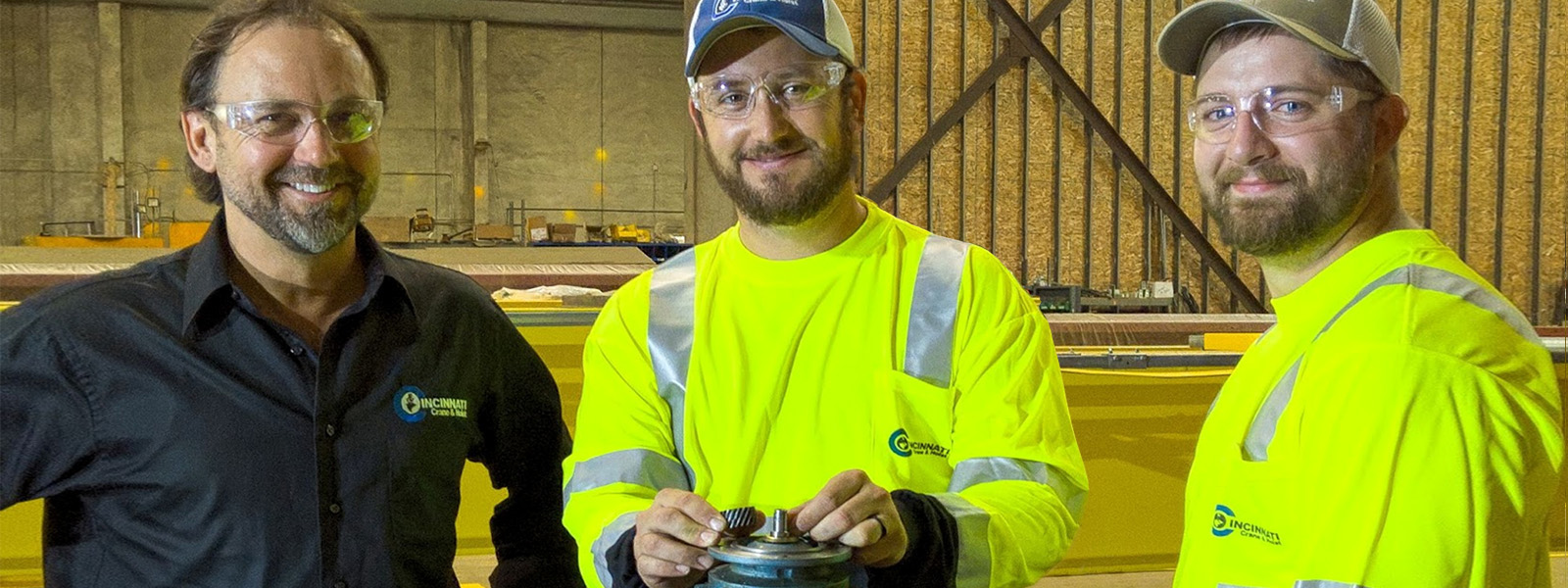
Workforce development is an essential yet frequently overlooked aspect of supply chain management in manufacturing. Similar to how disruptions in material sourcing or logistics can halt operations, talent shortages and skill gaps create bottlenecks that jeopardize efficiency, quality, and growth.
The decades-long manufacturing labor shortage is a complex and pressing issue, and the latest data indicates it may be more significant than previously estimated. A 2024 study from The Manufacturing Institute and Deloitte indicates that the domestic manufacturing industry could require up to 3.8 million jobs to be filled by 2033. A 2022 report from Deloitte estimated that 2.1 million U.S. manufacturing jobs could go unfilled by 2030.
The manufacturing sector faces significant workforce challenges that threaten its long-term viability. Factors contributing to this shortage include:
• Retiring baby boomers
• Skills gaps
• Changing perceptions of manufacturing careers
• Competition from other industries
• The rise of advanced manufacturing and the need for new skill sets
The result is a growing mismatch between available talent and industry needs. Manufacturers must adopt a more proactive, strategic approach to workforce development to close these gaps. Viewing workforce planning through the lens of supply chain management can provide a framework for addressing these challenges systematically. In this article, I’ll show you possible approaches and action items to integrate workforce development into your overall supply chain strategy to bring in new talent, foster innovation, strengthen resilience, and maintain a competitive edge in an ever-evolving industry.
Workforce as a supply chain issue
Workforce development closely parallels supply chain management, because both demand strategic planning, long-term investment, and adaptability to disruptions. Just as manufacturers diversify their supplier base to reduce risks, they must also expand and reinforce their talent pipelines. Neglecting this can create workforce bottlenecks that affect operations at every level, from production lines to delivery schedules. Talent shortages hinder the ability to scale operations, innovate, and meet customer expectations. This cascading effect mirrors the impact of supply chain bottlenecks, where one weak link disrupts the entire system.
Workforce development often functions similarly to supply chains in that it has upstream and downstream components. You depend on educational institutions and external training programs to help supply talent, and you can train and develop employees internally or with specialty training. These talent pipelines also face vulnerabilities, such as outdated curricula, limited access to training resources, and inadequate industry collaboration. It’s important to be aware of the strengths and gaps in those sources so you can build a more extensive and reliable talent supply chain.
Benefits of aligning workforce development with supply chain
As you better align your operation, your workforce development efforts will undoubtedly focus on more advanced skills, such as for automation and emerging technologies. This will not only benefit your operation in the long run; your employees will appreciate it as well. The benefits will include:
Reduced downtime. A skilled workforce can quickly adapt to changing demands and minimize production delays. MaintainX’s State of Industrial Maintenance 2024 found that investments in training and education were the third most cited reason for a decrease in downtime, trailing only preventive maintenance programs and replacing aging equipment.
Improved quality. Well-trained employees contribute to consistent and higher-quality output. For example, one automotive manufacturer saw defect rates drop by 18% after implementing a targeted skills training program.
Future-proofing. By equipping employees with the skills needed for emerging technologies, companies can stay ahead of industry trends. Examples include training in areas such as robotics, artificial intelligence, and data analytics positions businesses to embrace automation and smart manufacturing.
Employee retention. Investing in training and development fosters loyalty and reduces turnover costs. According to Gallup’s 2023 workplace report, companies that invest in employee development see a 20% higher retention rate on average.
How to embed workforce development in supply chain strategy
The keys to integrating your workforce development initiatives with your supply chain strategies are to focus on how and where the two areas intersect, target your training efforts, and build data into your decision making.
Step 1: Map the interdependencies
First, create a map of your supply chain. Identify key suppliers, transportation routes, warehousing, and internal production processes. Pinpoint critical dependencies: where bottlenecks might occur, where quality issues arise, and where flexibility is needed.
Simultaneously, map the workforce skills required at each stage of the supply chain to identify where current employees lack necessary expertise. This includes:
• Technical skills (machine operation, maintenance, quality control)
• Soft skills (communication, problem solving, teamwork)
• Digital literacy (such as using ERP or other systems, data analysis)
Now overlay the two maps to reveal areas where skill gaps directly affect supply chain performance. For example, if a specific machine is critical to production and requires specialized maintenance, but no employee has that expertise, that’s a key alignment point.
Step 2: Target training and development initiatives
Once you have identified the dependences, gaps, and vulnerabilities, you can focus your in-house training programs. Here are three possible approaches to your training efforts.
Prioritize critical skills. Focus training efforts on skills that directly address supply chain vulnerabilities. For example, if supplier quality is an issue, train employees in advanced quality control techniques. If demand fluctuates, train employees in flexible production methods and cross-training for multiple roles. If new software is implemented for supply chain management, provide training for employees to use that software.
Collaborate with suppliers on training initiatives whenever possible. This can improve communication, ensure consistent quality, and address shared skill gaps. For example, if your supplier uses a new metal treatment, ask them to train your quality control team.
Leverage technology for flexible, on-demand training. Utilize online training platforms and virtual simulations to provide cost-effective and accessible training.
Step 3: Define metrics to enable data-driven decision-making
Keep the interdependencies in mind as you create metrics to track your workforce development efforts. For example:
Supply chain performance. Your goal is to analyze how workforce development initiatives affect key supply chain metrics such as on-time delivery, inventory levels, and production lead times.
Employee performance. Also monitor the effectiveness of your training and development efforts through performance reviews, assessments, and feedback. Use this information to refine training programs and identify high-potential employees.
Predictive analytics. If budget allows, use predictive analytics to forecast future skill needs based on anticipated changes in your supply chain, such as customer demand, supplier capabilities, and technology.
Your local MEP Center can help you secure your future
Automation, sustainability, and digital transformation only heighten the importance of a skilled and adaptable workforce. Treating workforce development as a critical supply chain resource will help your company overcome challenges and prepare for the future. Experts at your local MEP Center can help you better align your workforce development with your needs. Contact your local MEP Center to get the conversation started.
Add new comment