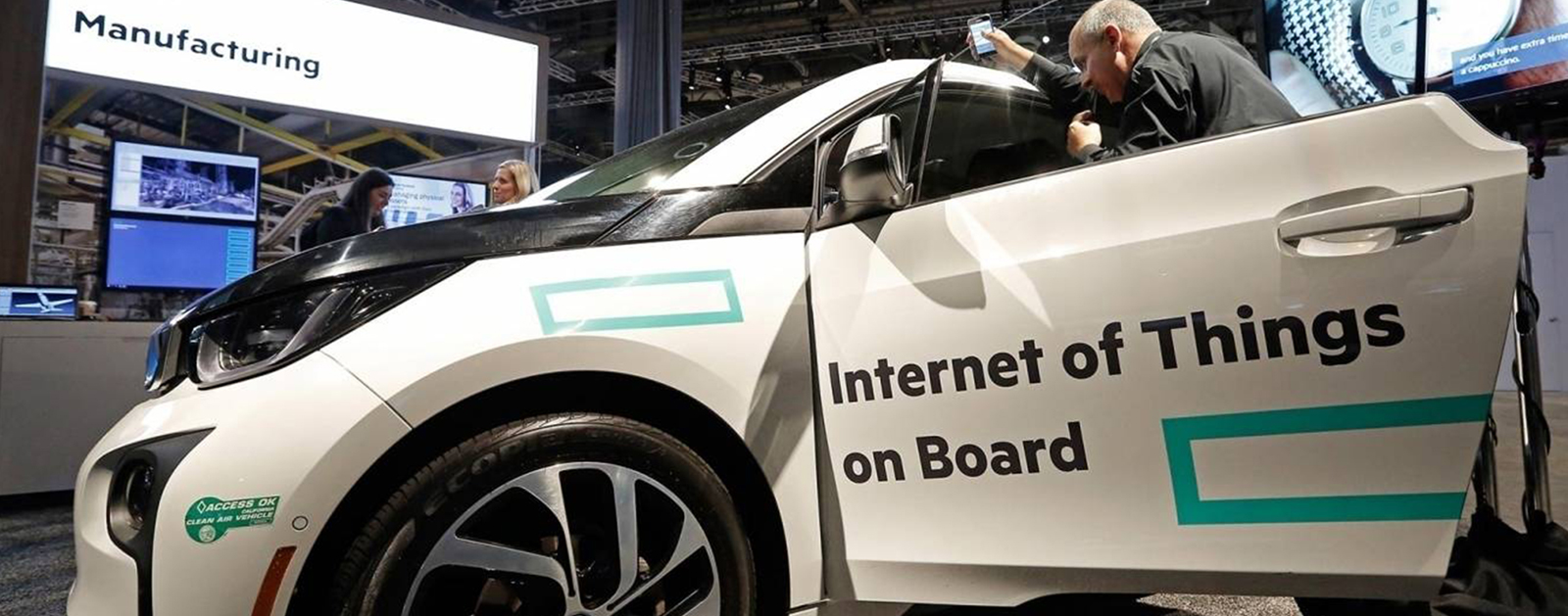
Your company leadership team just issued a corporate goal (aka mandate) of reducing defects to fewer than five per million units made. This goal is coupled with a need to reduce manufacturing costs by 10 percent while meeting new good manufacturing practices (GMP) or ISO standards. Oh, and you have four audits coming up in the next two months.
You are not alone. Today, everyone is being asked to do more with less while improving quality and reducing risk. The strategies and tactics of the past won't work because the world of manufacturing is far different today then it was 10 or even five years ago. There are so many more moving parts, both internally and externally. And all those parts are moving much faster today. Just like the rest of the world.
Quality manufacturing needs a digital transformation to keep pace and accomplish what is expected of companies and individuals.
Digital transformation?
Is that a thing? Does it apply to me? IT manages that techie stuff; do I need to be involved?
The answer is yes to all of the above.
Before we go into the top three reasons why quality professionals need to be part of manufacturing's digital transformation, let's quickly get aligned on what we mean by digital transformation.
Simply put, digital transformation refers to the use of purpose-built technologies that give us the ability to do more, in less time, with more control. It's a form of process improvement so that we can do things better and faster while reducing risk. This applies not only at work but also in our personal lives. What you may not realize is "digital transformation" has been happening in our personal lives for years.
For years we have all experienced an "old way" of doing something, which changes into a "new way" of doing something when technology advancements change our behaviors. And then innovation is applied to that "new way," and the result is a yet another "new way" of doing things. It's a continuous cycle of improvement.
Take, for example, a parent who has a teenager who is going out on a Friday night. To manage worries for her child's safety, that parent typically wants to know where the teenager is and what he is doing. How most parents have done this has changed rapidly during the past 25 years.
![]() Click for larger image |
This is digital transformation in our personal lives. Although this analogy may seem like a far cry from the complexity of quality management systems (QMS) for manufacturing and staying compliant, at a foundational level our goals haven't changed. It's the methods available to achieve our goals that have transformed over the years.
Now that we've cleared up what is meant by digital transformation, let's examine why quality professionals need to be an integral part of their organizations' digital transformation for better products, efficiency gains, greater agility, increased visibility, and more predictable results. This not only helps their companies succeed, it also gives quality an active role in these strategic initiatives.
Reason No. 1: Transformation is your expertise, and you are accountable for it
The operative word in digital transformation is transformation. Meaning change. Digital technology without related process changes and proper change management will not deliver the outcomes your company expects.
Technology is advancing so fast. It is a runaway train. The quality professional serves as the conductor so that the train operates safely and gets to the right destination on time.
All companies are going through digital transformation, from finance to marketing to manufacturing and every function in between. It impacts and enables improvement for all business areas. The only thing that's different today is the faster speed, larger scope, and bigger volume.
If your partners in IT leverage technology innovations without working hand in hand with quality, they can introduce risk and veer off course. Without IT understanding the systems that quality defines and adjusts, and why those systems are the way they are, IT will lack the guidance to drive real value. IT just doesn't have the product, process, and compliance awareness that quality does.
|
Bottom line: Quality is just as accountable for digital transformation as IT is.
Reason No. 2: The expanding role of quality
During the past few years, "quality" has emerged as a cultural imperative and has taken a central position within digital transformation initiatives.
Historically, quality has occupied a niche, reactive role within manufacturers. As manufacturing processes are established, quality monitors key manufacturing indicators and thresholds, springing into action once a problem is detected: Complaints are handled, root cause analysis is conducted, corrective actions taken, and operating procedures are updated—problem solved!
But that's not good enough anymore. Today's manufacturers need to prevent the problem (or any problem) from occurring in the first place to remain competitive. This definition of "quality" extends its scope to the point of design; quality needs to underpin all phases of the manufacturing process and in so doing, shift from a niche, reactive role within manufacturing to become a core tenant of the product journey.
As companies orient around the notion of "quality" as a cultural imperative, its role becomes more predictive. Problems are proactively averted. Manufacturing yields improve. Overall product quality increases. Customer satisfaction is enhanced. And all of this accrues value to the brand and an increase in the top and bottom lines.
Quality may be the only function at a company that spans the entire product journey.
Reason No. 3: The quality professional profile is changing
As the world advances, so do the profiles of certain trades and professions. Individuals need to change and grow their skills as the world continues to rocket through changes.
A marketing professional 20 years ago didn't need to know about social media and online search advertising. Today, if you want a job in marketing, you have to have those skills. Members of IT teams have been going through a similar change in ideal job skills. IT has traded in its focus on network connectivity and server maintenance for a stronger business acumen. Why? Because cloud technology has made "keeping the lights on" no longer something IT needs to worry about. More and more IT professionals are getting MBAs and working much closer with the business.
While managing CAPAs, nonconformance inspections, and supplier quality management are still core job skills, the expected skills of the quality professional in today's world are much broader. Artificial intelligence, connected devices (IoT), integrated coaching networks, real-time big data analysis, and using cloud to connect manufacturers with suppliers will all have an impact on quality in manufacturing; quality professionals will need to understand these digital innovations if you don't already.
Because how you manage those CAPAs, nonconformance inspections, and supplier quality management is changing, and those who continue to build their skills and leverage these new capabilities will ultimately succeed.
The future arrived yesterday, and it's time for all of us to gain the skills and perspective to adopt manufacturing technology suited for today's realities.
Ready to learn more? On June 5, 2018, Veeva Systems, a leading provider of cloud quality and regulatory software, is hosting an educational event in Cincinnati focused on why and how quality needs to be an active participant in digital transformation for quality manufacturing.
Join many of your peers and IT counterparts by registering today. Space is limited.
Add new comment