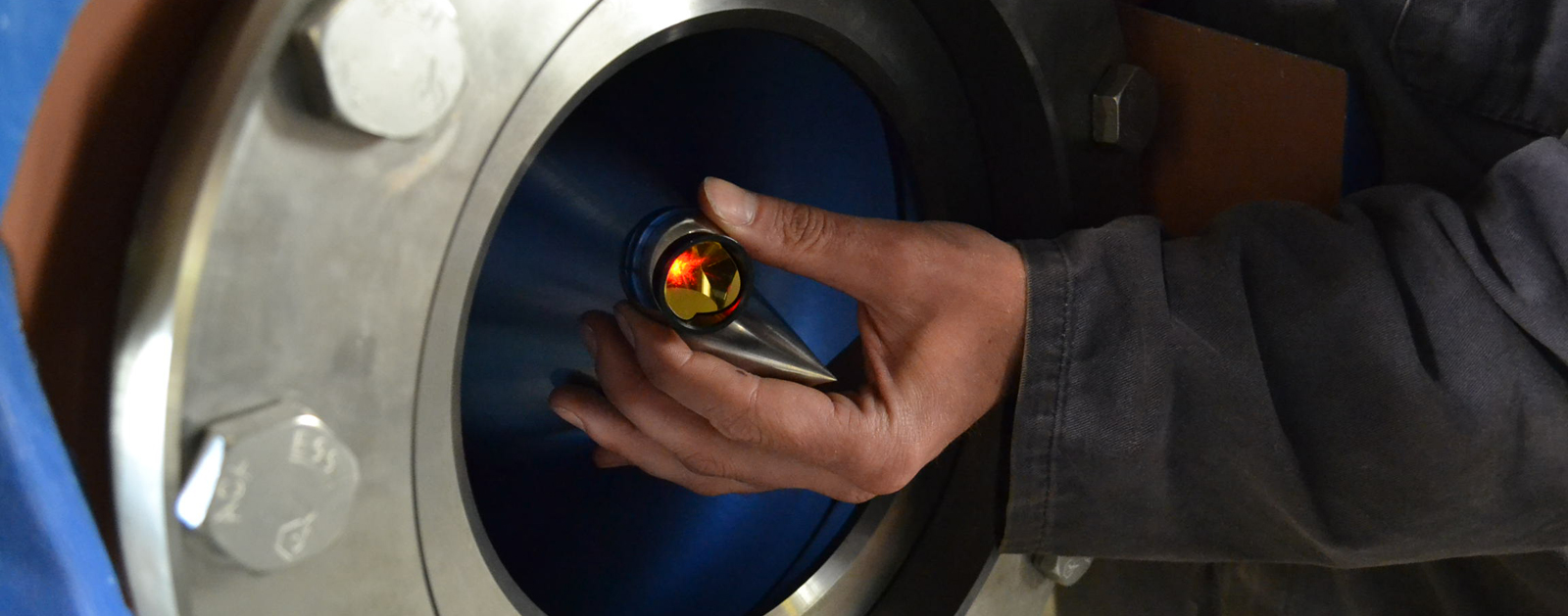
Invented in 1987 and commercially available since 1991, laser trackers have long been a mainstay of the aerospace industry. Automotive manufacturers have also adopted laser trackers for quality control (QC) and design. The fact is, any industry dealing with large-scale measurements—from small machine shops to medium-sized enterprises to major Tier 1 automotive and aerospace suppliers—all share the potential to realize tremendous benefits by adopting laser tracker technology. But, not all industries that could benefit from using laser trackers do use them.
Fortunately, advancements in ease of use and lower entry price-point have combined to bring about the democratization of laser trackers.
Not just for rocket scientists anymore
democratize: verb
1. to make (a country or organization) more democratic
2. to make (something) available to all people; to make it possible for all people to understand (something)
One reason laser tracker technology hasn’t been adopted by some industries that stand to gain so much has been a perception that extensive training and experience are required for an operator to reach a level of acceptable competency. And historically, that’s been a fairly accurate assessment.
“The earliest trackers were interferometer-based trackers,” explains Chuck Pfeffer, director of product management factory metrology at FARO Technologies Inc. “Which meant that when you broke the beam between the laser unit and the spherically mounted retro reflector (SMR), or target, you had to go back to a certain position and start again.”
|
Obviously that’s not an ideal trait for an instrument being used on the shop floor for large-part inspection and assembly. Although development of absolute distance measurement (ADM) systems increased the capability of regaining contact between the laser tracker and SMR, it was still done manually, which translated into wasted time.
“Half of the effort involved in using laser trackers is making sure that the SMR stays in line-of-sight with the tracker,” says Jim Cassady, factory metrology product marketing manager at FARO. “If you lose connection with the laser beam, things become difficult, frustrating, and challenging.”
|
One recent innovation by FARO Technologies Inc., called ActiveSeek, significantly improves usability by less seasoned operators.
ActiveSeek is a patent-pending feature available on FARO’s VantageS and VantageE laser trackers. The ActiveSeek feature enables the Vantage tracker to actively seek and lock onto a target after a beam has been lost during operation. What this means is that when a line-of-site beam is broken because an operator must walk behind an object or climb up scaffolding while taking measurements, the Vantage tracker will seek and lock onto the target again when the target is in a stable position—automatically. The stereo cameras used for this feature afford a 50-degree field of view—the best in the industry—and make ActiveSeek effective across a wide footprint.
“ActiveSeek totally changes the whole mindset of what you’re doing,” says Pfeffer. “Operators can focus more on their work now. That increases productivity, and even for the expert it saves time. ActiveSeek just makes it easier to make sure your tracker is giving you the best data all the time.”
“I love ActiveSeek. Even though I only began working with the tracker last year, I feel like ActiveSeek helps me control it like a 10-year pro. The moment I first used it, ActiveSeek made using the Vantage easy and effortless. When I use the ActiveSeek feature on projects with customers, they don’t even realize I am using it because it finds the SMR so well.” |
The ramifications of increased efficiency afforded by ActiveSeek technology touch everything from
productivity…
“We had one of our sales associates show this to a customer who was using a competitor’s product,” explains Cassady. “The customer is a major user of a competitor’s laser tracker. They tried out a FARO VantageS with ActiveSeek and compared it to the competitor’s laser tracker in a ‘bake-off.’ They were measuring a large, complicated assembly. With the competitor’s laser tracker, it took seven hours to do the measurements, plus another four hours to create the inspection report with the competitor’s software for a total of 11 hours. Using a Vantage with ActiveSeek, the measurements were completed in five hours, and, using FARO software, the report was generated in just two hours. Total effort with FARO/Vantage was seven hours vs. 11 for the competitor.
“To perform the measurements, the user had to climb on the frame of the large assembly and pass behind many steel plates,” continues Cassidy. “Every time, ActiveSeek with its industry-leading 50-degree field of view was able to find the SMR in just a couple of seconds.”
to safety…
“Imagine working in a factory,” suggests Pete Edmonds, vice president of global factory metrology at FARO. “As you walk around, there are beams, and girders, and machines, and all kinds of stuff that gets in the way when you’re taking measurements. As you move behind these things, when you have a traditional tracker, you have to keep your SMR in line of sight with the tracker. So, you may be climbing up a ladder or whatever it may be with one hand, and you’re holding your SMR in the other while you’re trying to keep the beam. With ActiveSeek, instead of trying to walk up the stairs with one arm, so that you can measure points 12 feet in the air, you can put the SMR in your pocket, walk up the ladder, and when you get to where you’re going, you just hold up the SMR and boom, ActiveSeek finds it.”
to HR…
“Our goal is to create a product for the guy that has a zero skill-set, and have a program for him where all he has to do is what the program tells him to do,” says Edmonds. “We think we’re getting close to being literally at that level where training is down to a matter of a few days to be able to be a solid and skilled operator of a product.”
|
The software FARO employs plays a big role in creating user-friendly systems.
“We’ve made it possible that what the operator sees on screen is just what he needs to do,” reveals Vito Marone, chief product owner of BuildIT Software and Solutions, a division of FARO Technologies Canada Inc. “On-screen instructions can guide the shop floor operators so they don’t need to go into the specifics of what’s needed—everything from connecting to the device to setting it up to alignment. These plans are set up, and the operator can just follow the instructions on screen for inspection or assembly or whatever the application is. That can include green or red indicators for whether an operator is cleared to move on to the next step or maybe should call for a supervisor before moving on. The data is automatically saved for reporting or future analysis as needed.”
Multiple use technology
Another aspect making laser trackers a more justifiable investment is the variety of applications they are suitable for.
|
“Laser trackers can give you live measurements and real-time feedback,” says Pfeffer. “So, when you’re doing tool building, or moving details on an assembly fixture into place, aligning rollers or system components, anywhere you need to move something dynamically into place with precision, that’s the place for the tracker. Any machinery that needs to be aligned to run well can be maintained with a tracker.
“Once a company owns a tracker to do a specific job, they always find that they can use it over here and over there, and ‘we have a machine over there that could be aligned,’ and ‘this thing could be inspected’ so, it builds on itself,” notes Pfeffer.
“It can start out leveling the bed that a machine is going on, and then building up the machine piece by piece,” he says. “Trackers have unparalleled ability in replacing parts that must be aligned in applications, like in a power plant or a mill. These applications are becoming more and more common with the ease of use and the price combination of the tracker.”
Affordability
Over time, as with all technology, the price point to take advantage of laser tracker technology has dropped considerably. In fact, from the time trackers were first commercially available to now, the industry has seen a drop in pricing by approximately 400 percent.
Because trackers are easier to use and the software is easier to manipulate, along with the drop in price, managers have begun to ask, “Why are we spending tens of thousands of dollars again and again to outsource this? Why are we using slow, old-fashioned methods to do this work? We could actually handle it ourselves now.”
Marone concurs. “As the price of the hardware goes down, it becomes accessible to more people,” he says. “So, you have reduced cost, reduced training time, and increased productivity. The combination of these elements makes using laser trackers possible for more people in various industries. It’s not just limited to aerospace as it used to be.”
Add new comment