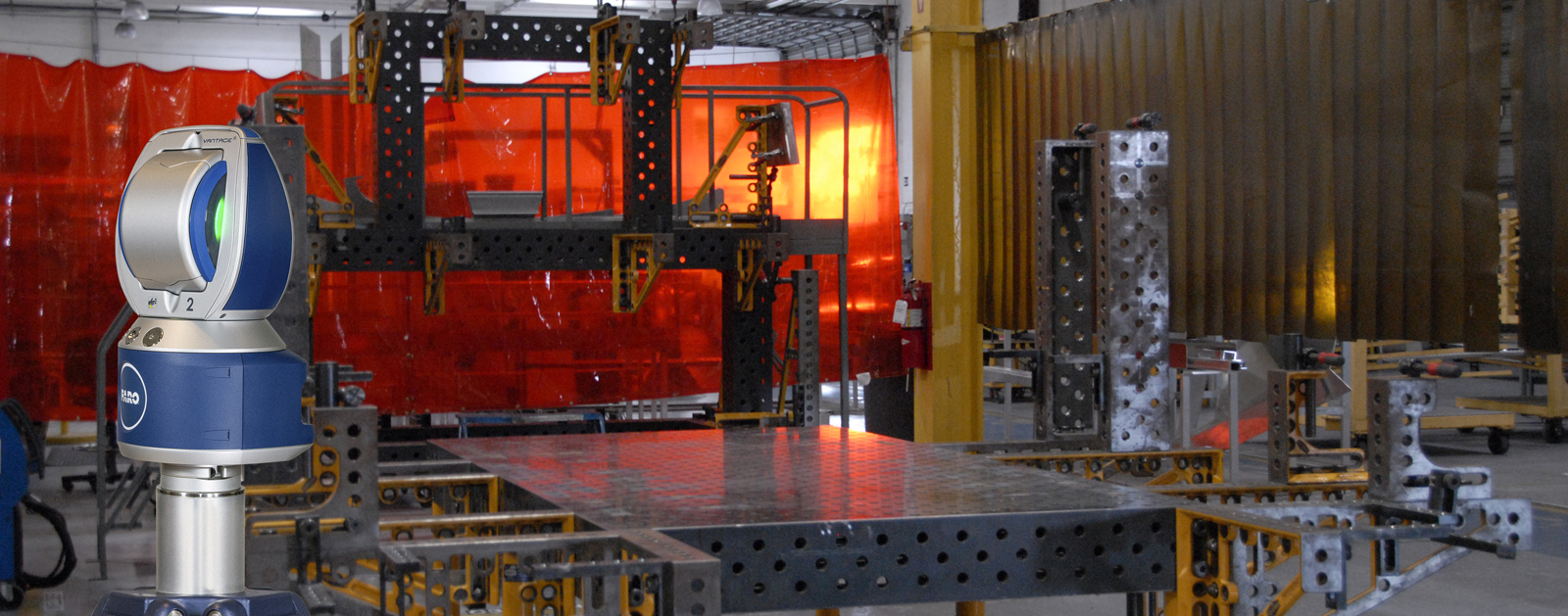
Advanced Integration Technology (AIT) serves the world’s largest and most technologically advanced aerospace OEMs and tier one suppliers, including Boeing, Airbus, Lockheed Martin, Northrop Grumman, BAE, Embraer, Spirit AeroSystems, Triumph, and Bombardier. AIT has facilities in the United States, Canada, Germany, Spain, and Sweden. Boasting multimillion-dollar contracts and multiple supplier awards from prestigious aerospace OEMs, AIT is a bona fide manufacturing superstar. If you’re in manufacturing, you must ask yourself, “What does it take to build an organization like that?”
Requirements for business excellence
AIT takes a classic approach to excellence by combining customer satisfaction, innovation, and utter dedication to quality: “We work with customers to turn the impossible into the possible, create opportunities to lower costs, reduce risk, and deliver systems within limited time constraints,” the company says on its website.
The thing that sets AIT apart from other manufacturers is not a secret sauce but its execution of these tried-and-true principles.
The leaders at AIT also know that achieving extraordinary levels of repeatable quality requires tools and technology that allow them to consistently manufacture within a few thousandths of an inch. They can’t do it building “shimmable” parts. They must invest in the means to deliver “the impossible” and to do so “within limited time constraints.”
The impossible
For the AIT team, sometimes the impossible takes the form of sensitive work for government entities that requires ultra-secure, self-contained manufacturing facilities within facilities.
More often though, AIT must continually innovate to design and build large tooling with tight tolerances.
“At our particular facility we do 90-percent one-offs,” says Robert Weller, metrology supervisor at AIT’s Michigan tool manufacturing plant. “Some tooling we make are just one-time-use tools, R&D stuff, but here and there we'll have a small run of two to five units. But no two jobs are ever the same here, so we have to keep up with engineering.”
The tooling AIT manufactures poses multiple challenges. For the most part, each piece produced is unique, large, and complex.
Moreover, they must get it all done in a time frame that satisfies their customers and turns a profit.
Made possible
Typical manufacturing scenarios often see a part built up of several components and then verified to specifications at the end of the process. AIT’s tooling plant in Michigan identified serious efficiency shortcomings in that processes.
“We do something here a lot different than a lot of people,” reveals Weller. “In our bond tool manufacturing process, we use FARO Vantage Laser Trackers every step of the way. From fab to machining and final and build, and then all the way until the job is packaged up and shipped out the door. You know we put a laser [tracker measurement] on it pretty much 100-percent of the time all the way through.”
With 160 m (525 ft) of spherical working volume, the FARO VantageS and VantageE series have reinvented high-accuracy, large-volume measurement. The Vantage provides tremendous value in a complete laser-tracking solution that offers portability, accuracy, and great shop-floor durability.
“So, on a bond tool, for instance, after we prep the data, the fabricators will assemble the bond tool and just tack it together, and then we’ll go in with a laser tracker and shoot the whole tool to make sure it’s square and straight in parallel, and good to weld,” explains Weller. “When it’s done being welded, we’ll shoot it again to make sure it’s still within tolerance. Then we’ll tack on the face sheet and measure the face with the laser tracker again. As long as everything is still within tolerance, they’ll weld that on, and then it’ll go out to heat-treat. When it comes back, we’ll measure it again with the tracker. We then mill the face sheet, and when it comes out of the mill, we’ll measure it again with the tracker. Then it goes into a bench phase, we’ll measure it with the tracker after bench, and then it’s pretty much ship it to the customer.”
Although adding multiple inspection points may seem counterintuitive to increasing throughput, AIT has seen the light.
“We have a tool that’s in machining right now that we used two laser trackers, one on each side,” says Weller. “We’re literally doing on-machine inspection of the tool as it’s cutting. We’re in and out a lot quicker doing it that way.”
The VantageS is intended for short- to long-range measurement applications of up to 80 m, while the VantageE supports short- to medium-range applications of up to 35 m. Both compact models offer:
• ActiveSeek (patent pending) capability to quickly sync up the user and the tracker to measure faster than any other laser tracker in the market today.
• RemoteControls workflow (patent pending), which streamlines laser tracker operations, allowing a single user to control functions, such as live video feed and tracker movements, from a mobile phone or tablet. A single operator can easily control the tracker from anywhere in the measurement area.
• Industry-leading portability with an integrated master control unit (MCU). These laser trackers are easily transported in a single carrying case between job sites or locations within the factory.
• Hot-swappable batteries that eliminate the need for AC power and cabling.
• Industrial-grade WiFi for reliable, wireless communications.
Within limited time constraints
“Doing inspection this way affected our business by speeding up the process of getting tools we are building through each department, as well as reducing rework by roughly 75 percent,” says Weller. “When you have a laser tracker collecting data at each step of the process, you don’t even have rework later. Let’s just make it right, right now. Rework always involves additional money spent, and stopping for rework doesn’t help get the job out the door on time, either.”
Delivering product in a timely manner is second only to quality when it comes to customer satisfaction. To aid in delivering world-class quality as rapidly as possible, AIT also employs several FARO ScanArms.
It’s all about increasing throughput.
“It’s just quicker, faster, and easier to do inspections with a FARO ScanArm rather than to keep using a CMM,” admits Weller. “There were three CMMs in use when I started with AIT, but between the software and the FARO arms, I would say our inspection time is at least 30- to 40-percent faster.”
On occasions when time restraints are even more of a concern than usual, the team assigns multiple operators and ScanArms to one piece with multiple inspections going on simultaneously. In those cases, the team utilizes one Vantage Tracker with multiple arms scanning into a single coordinate system.
“When we have a super-tight deadline, sometimes we combine the tracker with more than one arm,” explains Weller. “With that setup, we can reach as much critical stuff as we need to while we keep moving forward.”
FARO refers to this configuration as the Super 6DoF TrackArm. The Super 6DoF provides high-accuracy 3D scans, even for large components. It can be used to measure complete cars, car bodies, bodies in white, tools, fittings, fixtures, parts and components, cubings, and master jigs for pilot and production phases. Super 6DoF is ideally suited for applications with parts that are not only large but also extremely detailed and complex. This advantage makes it an ideal solution for industries such as automotive, heavy machinery, and aerospace.
Growth through investment
Although AIT already employs numerous FARO products, it continues to invest in the future.
“Actually, I just got a quote today for three more Vantage Laser Trackers,” says Weller. “The accuracy and repeatability of the FARO equipment factors into our growth due to the fact that we’re outputting good tools to the customers. They see a high degree of quality in tool after tool that was made in our Michigan plant. We’ve had plenty of installs where customers have asked us, ‘Is this a Michigan tool?’ Yup. ‘Thank God.’”
Weller sums up his assessment of the FARO equipment: “The accuracy and repeatability of the FARO products are superb. Our operators like how easy it is to hook it up and get it going.”
“Another thing with FARO is the support group,” he adds. “When you need help, they’ll talk you through everything you need to know. You send them an email, and they will call you back and walk you through the steps necessary to go through.”
Add new comment