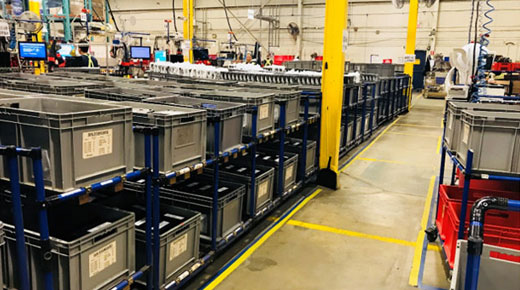
Cogeco’s technical distribution center in Burlington, Ontario, is one of Canada’s drop-off points for internet modem and cable device repair. In 2011, the company’s management carried out a kaizen blitz to improve the efficiency of its device repair process. The process was indeed challenging but did have the desired outcome. Read on to find out how Cogeco integrated a lean solution into its operations, and how it dealt with resistance to change.
ADVERTISEMENT |
Kaizen blitz: before and after
A consulting firm hired by Cogeco was tasked with analyzing just how efficient the Ontario warehouse was with regards to best practices. Once all was said and done, and the results were in, they were dismal. The production line was in no way efficient. “At that time nobody knew on the floor if we were productive or not because we had no way to measure, and we can’t improve something that we don’t measure,” explains Bill Jeffries, Cogeco’s warehouse manager.
…
Add new comment