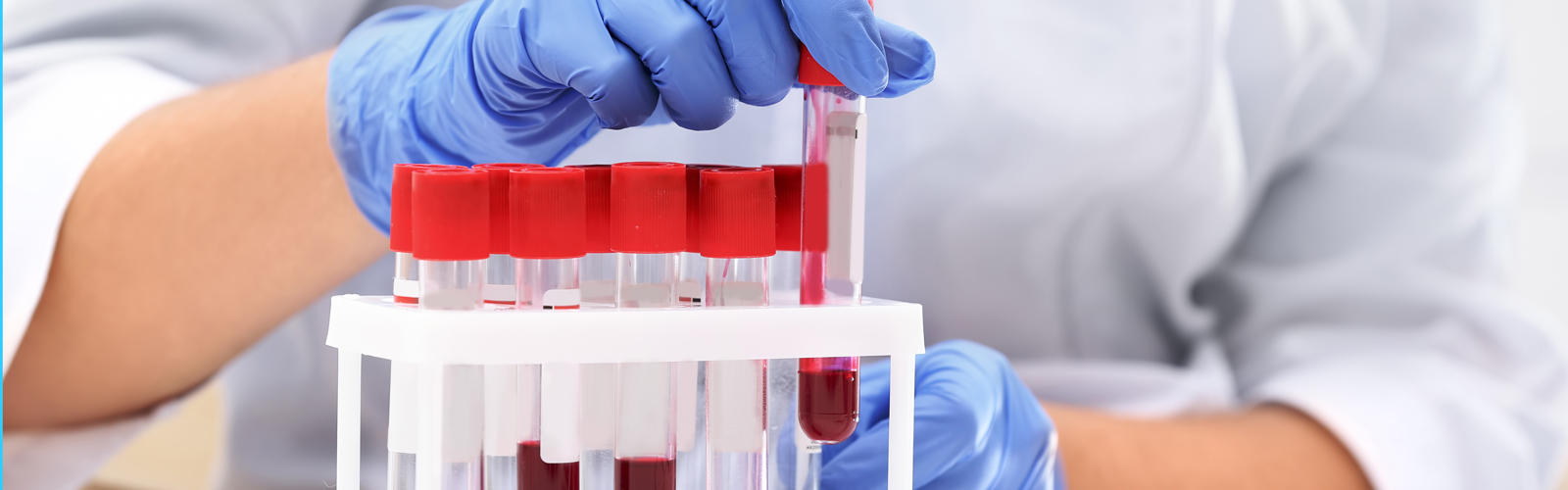
BioBridge Global (BBG) is a parent organization for four subsidiary organizations, three of which are involved in production activities, and they’re all around regenerative medicine, including blood components, clinical laboratory testing, and cell and tissue therapies. Organizations in the life science industry, like BBG, operate in a heavily regulated environment. This is the story of how one company delivers world-class products and stays on the right side of compliance while doing it.
BBG’s subsidiaries are:
• Qualtex Laboratories, which provides state-of-the-art patient, donor, and biological testing services. Qualtex has locations in both Texas and Georgia.
• GenCure, which is a human-tissue and cell-therapy organization, collecting and processing human tissues, umbilical cord blood and tissues, as well as providing cell therapy apheresis services, and contract manufacturing services.
• South Texas Blood and Tissue Centers, which provide blood, plasma, platelets, and other blood components to 67 hospitals in 43 South Texas counties.
The fourth arm of BBG is the Blood & Tissue Foundation, which raises awareness and funds to support the many life-saving activities of BioBridge Global.
BBG’s efforts reach into blood transfusions, bone grafts, and cell therapy. With human lives at stake and rigorous regulatory scrutiny, BBG depends heavily on a digital QMS to help it do its jobs.
At the MasterControl Summit 2018, I enjoyed the fortune of sitting down with Adrienne Mendoza, vice president of global quality and compliance at BioBridge Global, to discuss how BBG deals with QA and regulatory compliance in such a challenging environment.
“We’ve been in this work—blood product collection, processing, and testing—for over 40 years. We were one of the first organizations to become AABB (American Association of Blood Banks) accredited, also one of the first blood banks to become ISO 9001 certified.”—Adrienne Mendoza |
Quality Digest: How does your quality management system (QMS) help you deal with such a tightly regulated industry?
Adrienne Mendoza: It’s a huge part of it because we have to be able to tell [an inspector] the story of what has occurred throughout a process, how we evaluated the risks, and how we approved the procedures that are going into production. If anything goes wrong, we have to be able to show what happened, when did it occur, and how did we to respond to it.
It’s all really about making sure we can show the entire story of what we designed into a process, how the process went, and if there were any deviations. We also have to make sure that everything involved in a process is qualified, meaning procedures have been approved, training has been completed for all the staff, validations have been signed off for all the equipment, and testing has been completed for all the reagents and materials used.
[Our QMS] also allows us to document our changes, so if we need to make a change to a process due to an opportunity to improve it, or maybe we need to implement something new because of new equipment, we can document the change that’s happening and connect that to the things that we’re changing. [Any change to a process means] we need to reassess the risk, so [within our QMS] we connect that change control to a new risk assessment. We can connect it to changes to the procedures that are relevant to that change and who approved those procedures, and then the training based on those procedures that has to be carried out or connected to that. So, it’s entirely connected—showing everything that we did upstream to make sure that the process was well designed, addressed all the risks, everything was qualified—to anything that happened and any changes that happen after everything’s put in place.
QD: Have you dealt with both a paper and digital QMS environment?
AM: I have, and from just a pure efficiency standpoint, simply being able to find procedures digitally is much easier than if you have to break open “the big binder” and go through and dig through it. We literally have 6,000 procedures; you can imagine what it would be like if we had to handle all those [procedure document] books to make sure we version-control everything out of it, ensure that people can find the data that they need, and that it’s the right procedure.
There’s a lot of potential failures that can happen with maintaining a paper-based system, from having the wrong version of a process, having it not available, or not being able to find it fast enough to be able to make a key process happen. And that’s just the procedures alone, where there are advantages with a digital vs. manual QMS.
[A digital QMS] also can show connectivity between the production process, the deviations, the change controls, approved procedures, and training and validations. Being able to connect those digitally, we can, in a way, automate our assurances that everything was in place before we release a product because we can go back and see that, yes, everything was closed. All training was closed, all material qualifications were closed, validations were closed, edition SOPs were implemented—everything was effective.
In the past [with a paper-based QMS], we would have had to go and pull this big binder to verify everybody had signed it, review the entire record—not review by exception. Being able to automate just the quality management system that houses our deviations, change controls, complaints, documents, and trainings has been a huge time saver for the end users in trying to look up their procedures and complete their training, and also for quality assurance and quality control staff, who need to be able to verify everything was done correctly and be able to ship their product on time.
QD: What about physically maintaining all those paper records?
AM: Unless you move those records to a digital form by scanning or something, you're going to start stacking it up, and then you have so much paper that you're going to have to start storing it somewhere. Just the physical volume of what you’re dealing with is gigantic.
So, then you’ve actually introduced risks, like workplace injuries from lifting those boxes and moving them around; while carting them around from place to place, a paper could fall out or fly off the truck or whatever. You’ve just always got that paper you’re dealing with.
It’s a great, limiting step which, at some point, you cannot keep up with. From a whole cost-of-production standpoint, maintaining it would be impossible. In the [life science industry], there are some records that must be kept indefinitely. So, if [your organization] grows two or three times the size of what you are, and you're producing that much more paper, you just have to change to a digital platform.
QD: We've already heard this weekend that, although the FDA certainly does not require electronic records during audits, it does advocate for their use. What’s the benefit of a digital QMS during an audit?
AM: I've been involved in audits with a paper-based system, and yeah, we ended up filling a room with all the requests that came up. It’s fast and furious, you know? Run to the warehouse, collect that paper, dig through and get everything that was requested. You literally have tables lined up around your audit room piled high with the paper that has to be reviewed. It can be overwhelming when an inspector is waiting. They might get to thinking dangerous thoughts like, “What’s happening? Are they producing this record behind the scenes or something?” Which, of course, is not the case! It’s just taking time to collect that record from the archive position, which is deep in the warehouse, to bring it up for the audit.
I’ve also been involved in audits with an almost entirely paperless system. We were able to present to the inspectors the systems that we're using digitally, and hone in on the section they're asking about without having to show them the entire record start to finish. [Usually] they’re only asking about one or two steps, so you can zoom into those steps and show them. It’s much faster, and I’m sure it makes a much more pleasant experience for the inspectors as well.
I think it’s a huge improvement in the outlook of the inspector because having a digital system in place is becoming more of an expectation; it’s becoming the norm. I think an auditor or inspector can definitely be affected by their perception of you as an organization that hasn’t adapted to more modern mechanisms to prevent and control those risks. And that can hinder a discussion that is, sometimes, already challenging enough. If they get the sense that your organization is not progressive and not improving, it’s not going to paint a very good picture for you. [Inspectors] are looking for [the people involved in a process] to be able to call up information quickly, understand what it says, and be able to deliver that information concisely. It’s about speed and transparency, and those two things are optimized by utilizing a digital platform.
“Our mission is saving and enhancing lives with the healing power of cells and tissues.”—Adrienne Mendoza |
QD: What do you think about the FDA brief, “Supplanting 21 CFR 820 with ISO 13485,” will that have any impact on BBG?
AM: Well, I think it's a big benefit. We don’t manufacture devices; however, 21 CFR Part 820 does apply to our company because it’s referenced as a quality system. It’s referenced by the blood regulations as well as the human cells and tissue regulations, and so we already comply with 21 CFR 820. Where I see the benefit of FDA’s adopting the ISO 13485 standard as a reference point for medical device regulation is the global harmonization. ISO 13485 is recognized internationally, and our industry is becoming more global in nature. For instance, products and devices may be manufactured in one area, tested at laboratories outside of that original jurisdiction, and then shipped to multiple countries. Currently, each country may be regulated differently, and their standards may vary. So, in my opinion, this is a step in the right direction to ensure a more globally harmonized system of regulations and standards so that no matter where you manufacture your product, you're going to meet the same quality systems requirements for that product, whether it’s manufactured in the U.S., China, Japan, or the South Pacific somewhere. The ISO 13485 standard is very logical; it’s complete, and it makes sense. So, I think it’s a positive change.
Learn how digital compliance solutions can help you respond to new FDA and ISO regulations.Get your free FDA/ISO Compliance toolkit now |
QD: What does the shift mean to Biobridge and other organizations in the life science industry?
AM: Although in large part we’re compliant with it, we don’t have an ISO 13485 certification. We do have an ISO 9001 certification, but there’s a couple of its components the FDA recently harmonized to 13485, so we are meeting 13485 with a few small exceptions. What we’re doing is performing an assessment of any gaps that we might have to ensure that we can put those systems in place, but I know that with our implementation of MasterControl and our QMS, we won’t have any problem complying with that.
QD: Any recommendations for other companies that will need to be in compliance with ISO 13485?
AM: Yeah, my recommendation would be for them to review the way that they handle their process development work—and document it. That’s a major component of being able to demonstrate that you’ve addressed any potential risks within your process, and that you have evidence-based conclusions around what you’re doing.
Make sure that for any production failure, there’s a process in place to investigate and correct those things. Make sure there’s a process to manage change control and evaluate the performance of things through their metrics at management review intervals. As long as they adhere to a really robust quality management system, they shouldn’t have any problem, but they can go back and look especially at those sorts of foundational elements; how do they design a process and document all they do to manage, review, and maintain that process.
Add new comment