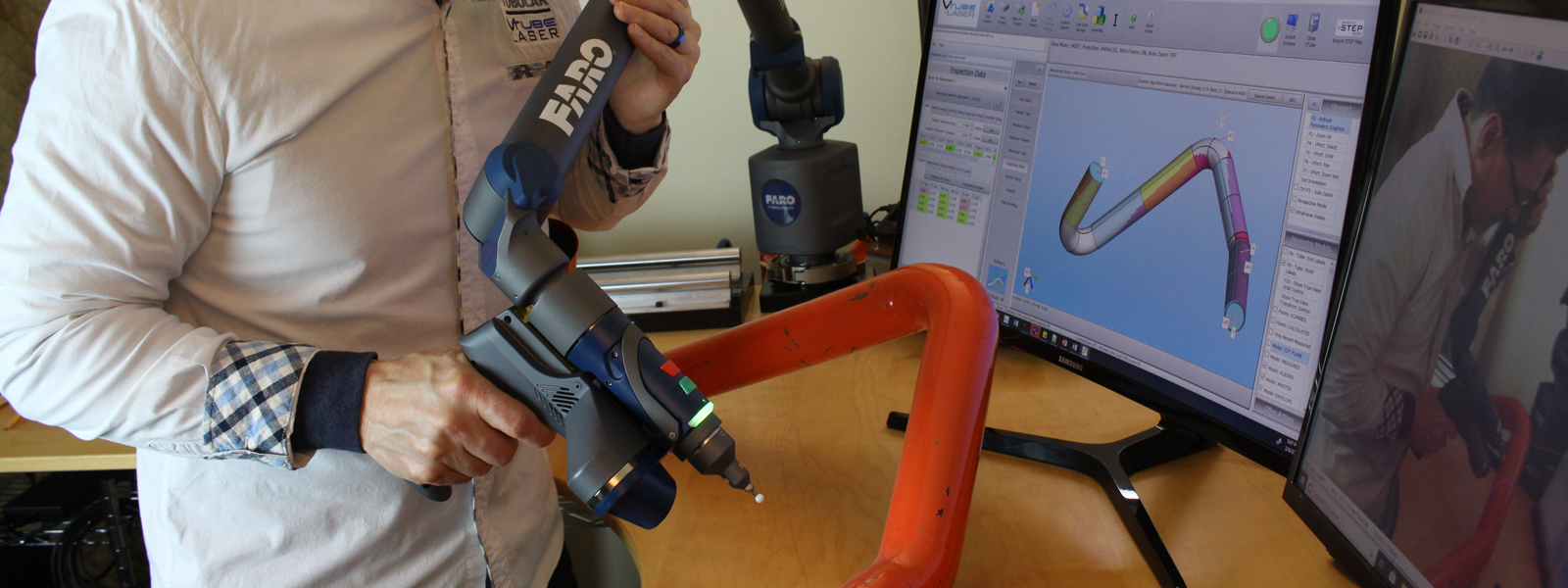
In the manufacturing universe, metal tube fabrication is a world of its own. That being said, the requirements for developing a new world-standard solution for tube bending are common to all manufacturing—be faster, more accurate, and more economical.
With customers like Delta Air Lines, British Airways, United Airlines, and the U.S. military, Advanced Tubular Technologies has been working to deliver on that goal. Its systems are used across many industries, including air compressor and hydraulic parts manufacturing, shipbuilding, railroad and exercise equipment, and the race car circuit in Nürburgring, Germany.
Advanced laser scanning technology and the software required to leverage it to the fullest are having a tremendous impact on the tube fabrication industry, and this synergy is the foundation for Advanced Tubular’s VTube-LASER solution.
“My goal is to make VTube-LASER the world standard in tube-measuring software.”
|
Standard, old-school method
For decades, jigs, fixtures, and gauges have been the standard method of ensuring a finished product meets its intended design.
“In a nutshell, a CNC bender operator bends a tube [with multiple angles] and then drops it into a gauge,” explains Mike Cone, owner of Advanced Tubular. “It’s not uncommon for the part to be twisted up, under-bent, or somehow not fit. So, the operator assesses what changes to the bend angle and the planes between bends need to be made, enters new data into the bender, and then hours later delivers a tube that kind of fits the gauge. That’s the standard method.”
Cone saw the opportunity to introduce a game-changing upgrade to the industry.
Building a better standard
The new gold-standard in engineering is the model-based definition (MBD) method. MBD relies on laser scanners and software capable of leveraging its unique advantage of gathering massive amounts of measurement data.
“Tube fabricators now have the option to use an articulated arm [and laser scanner], like the FARO QuantumS ScanArm, coupled with VTube-LASER software,” reveals Cone. “They can now scan a [first article inspection piece] and compare it with a virtual gauge on-screen. They can see if and where a part is outside of a tolerance envelope, and that information is in the form of data. That data go to the bender, and the next piece is ready in minutes instead of hours. Manufacturing reps see this technology and say, ‘Wait, we’ve been doing this manually for years, and it’s cost us two to four hours every time. Now we can do it in 15 minutes?!’ They start scrambling for funds to buy one of our systems because they understand the ROI immediately. It’s very powerful when they see they don’t have to guess anymore.”
|
Measurement data at the bending machine
The MBD method brings a whole new level of efficiency and profitability to manufacturing operations.
“Importing model-based definition is the most hotly sought-after methodology of bringing data in,” explains Cone. “There is a section of our software called the VTube-STEP, and it’s named that because what it does mainly is import STEP models. We can import entire assemblies with it. The old way is to enter X, Y, Z coordinates. Or you can enter bender data and reverse-calculate back to X, Y, Z data. With MBD, you just punch a button, and the next thing you know, the model itself is being analyzed.”
Cones’ new “world standard” for tube fabrication includes the ability to connect laser scanner data directly to the tube-bending machine.
“Connecting databases to bending machines is one of our areas of specialty,” says Cone. “We trademarked the name Benderlink back in 1993. This software can link to multiple brands of benders.”
“Basically, whatever data are collected using the laser scanner are analyzed, and then updated bend information is routed to the bending machine, where instead of manually entering the data, an operator can just punch a few buttons to accept the data.”
Advantages of laser scanning technology
Versatility
“Many of our customers want a laser scanner because there are so many things you can do with a laser scanner in addition to measuring tubing,” says Cone. “With a fork probe, all you can measure is a tube, and you can't even measure a square tube, really. With VTube-LASER, you can measure square and rectangular tubing, or you can measure cylindricity. You could even run another software package and scan the fender on a car. Go for it! You can’t do that with other solutions.”
Reverse engineering is another powerful component of laser scanning technology.
“We had one customer who commissioned a company in China to make parts for their evaporator units,” says Cone. “The company made them but never documented anything. He got all these parts back, maybe a thousand of them, but he had no digital information at all. This customer was able to reverse-engineer the newly designed parts with the VTube-LASER system.
“Reverse engineering is an invaluable process,” he adds. “I was recently visiting a company that makes after-market classic car parts like fuel lines and brake lines. These are long units reaching from the front of the car all the way to the back. They were going to reverse-engineer a certain part that had no existing model data. They had just invested in our VTube-LASER system and wanted to see how fast they could do it. They had it completely bent in about 10 minutes. They said, ‘Last week we did a similar part manually, and it took us two hours!’”
Industry-leading solutions, like the FARO QuantumS ScanArm, up the versatility quotient with an integrated hard probe and can digitize interchangeably without having to remove either component.
Speed
The FARO QuantumS ScanArm combined with Advanced Tubular’s software is proving to be a synergistic combination, greatly increasing throughput and bottom-line profitability in the tube fabrication industry.
“Our software, in addition to qualifying the shape inside an envelope, sends correction data out to the bender,” says Cone. That’s just critical for generating increased throughput. “Some of the operators are shocked when they start to realize how much faster and reliable this technology is. We had some operators who originally thought their bosses were nuts for buying this, but after about an hour of the system self-correcting part after part after part, they came back with big grins on their faces saying, ‘Wow, this is really working. This is going to save a lot of time and money.’”
“Think of this as a really nice tool that’s going to make you look really good, really fast.”
|
Ease of operation
With the VTube-LASER system, scan data are transferred seamlessly to VTube software, streamlining operations with much fewer steps to completion.
“I had a FARO account manager tell me, ‘I measured a tube with two of your competitors’ software,” boasts Cone. “With one, the job took me 75 button presses, with the other it took me 175 button presses. I just went and measured the same tube with VTube-LASER, and it took me only five button presses. I'm sold.’”
"I have a great working relationship with FARO. I value that relationship. It’s been a very positive experience, and they’ve provided a lot of support and enthusiasm. They’re very knowledgeable people."
|
Accuracy and repeatability
Cone is not only the founder of Advanced Tubular but also the lead developer of a small and dedicated team. According to Cone, “We don’t hide from the guys on the shop floor.” This direct communication with senior operators only serves to illustrate the high level of accuracy and repeatability that advanced technology can provide.
“One company had our VTube-LASER mated to a FARO scanner, but they still had their older machine in the shop,” explains Cone. “They were measuring parts with our system and cross-checking it with the other machine. About a month later they called me with a complaint about some discrepancies. Basically, their message to me was, ‘We want you to make the outcome of your results to be just like the old machine.’
“I suggested we run some tests before deciding which system they should be copying. We discussed gauge R&R, and then started working through it. They ran repeatability tests on both measurement systems, and when they were finished, our system so devastated the other system in accuracy and repeatability, their administrative staff forbid further use of the old machine.”
The conclusion: The VTube-LASER system gathers and optimizes so much data, Advanced Tubular is enabling and protecting users at levels they’re not used to.
“Our data tell the truth about a part.”
|
Add new comment