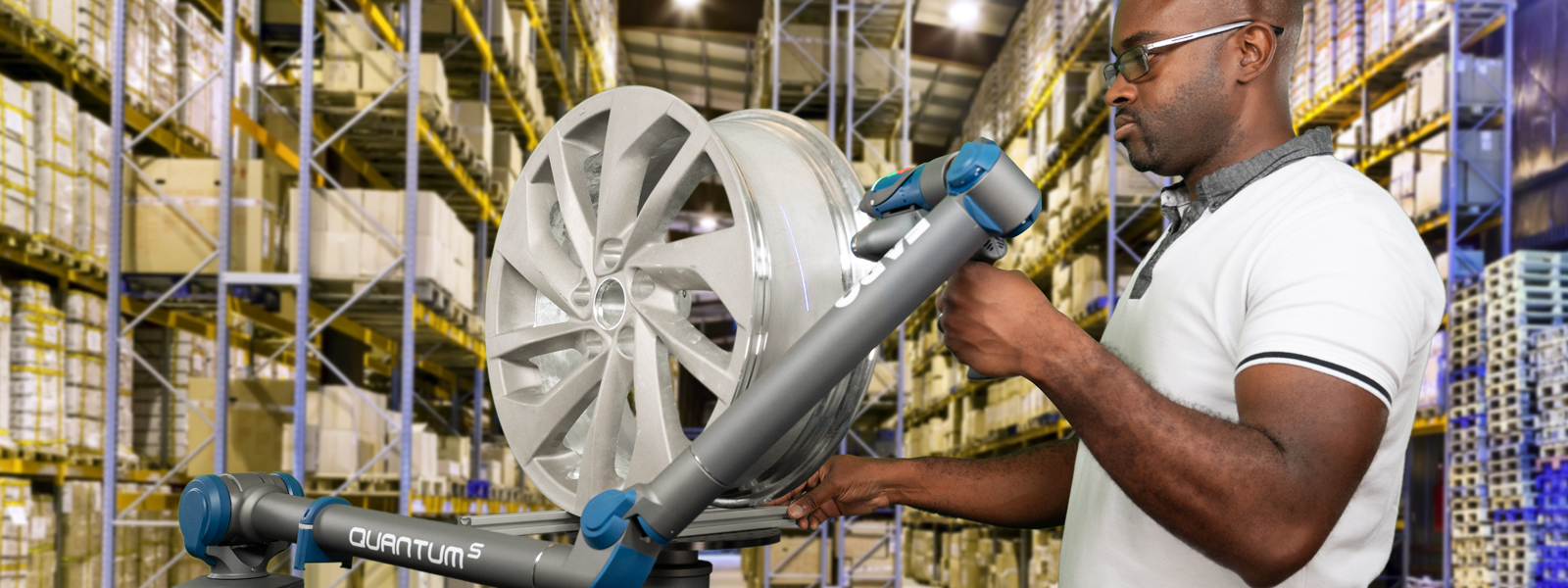
If your manufacturing organization is going to grow, you know you need an inspection solution beyond the capabilities of micrometers and calipers. You know you need to gather more data in a faster and more reliable manner. It’s time to invest in a 3D inspection solution like a coordinate measuring machine (CMM). You also know CMMs require a significant investment and you shouldn’t rush in uninformed. Here are three questions to ask yourself to help you make wise decisions that will result in a good return on investment.
These questions arose from a conversation I had with Elliott Mills, product and regional sales manager; and Les Baker, applications engineer; both with FARO Technologies. These two have several decades of combined experience using both fixed and portable CMMs in multiple industries. Their hard-earned insight about 3D inspection comes from many years on the shop floor. Before deciding on a metrology solution, it would be wise to consider the following:
1. What is the size of parts to be measured?
2. What is the actual level of accuracy required?
3. What are the throughput requirements?
Your decisions on whether to invest in a fixed or portable CMM will be based on a composite of answers to these questions. It’s not likely that any one aspect will provide a make-or-break answer, but examining your needs with a trifecta point of view may help your team to better address its inspection needs.
Size of parts to be measured
This is a good place to begin evaluating your inspection needs. Are you working with flat parts or volumetric parts, more or less than 3 sq ft? This is not a wish list. The size capability of an inspection system has a direct correlation to its overall cost and complexity of implementation.
“If you’re measuring very large parts, and you want to do so in an automated fashion, a fixed CMM may be a good solution,” says Mills. “But, when you get into very large volumes, say 2 to 4 m2, the initial investment can run up to a quarter of a million dollars. If it is a very large machine that requires a dedicated foundation, you’re looking at half a million dollars, maybe a million dollars. Large-volume capability has got to be a true value fit to warrant such an investment.”
The size capability of a large-volume fixed CMM also comes with square-footage stipulations.
|
“Installing a large-volume fixed CMM is a big undertaking,” explains Mills. “Beyond simply acquiring the asset, you often need a dedicated temperature-controlled environment, which means you need the square footage of the CMM’s footprint plus the room it goes in. And you have to consider how you’re going to control the room’s temperature and humidity.”
Les Baker also has experience with large-volume CMMs.
“To reach more than, say, 1.5 m, a fixed CMM typically has to have a long and wide base, and also pushes you up into the real high-dollar CMM price range,” says Baker. “But with something like the 3.5 m (11.5 ft) FARO ScanArm, certified to 0.080 mm (0.003 in.), you can reach to a height of more than 1.5 m (5 ft) from its base.”
“I recently visited a company that used to have three gantry-style CMMs. They sold two of them and now scan everything with a FARO Quantum ScanArm.”
|
|
Accuracy requirements
It cannot be overstated how important it is to have concrete knowledge of your organization’s metrology needs. What are the measurement parameters you work with? Are you measuring product down to within ±3 µ (0.0001 in.), or will your needs be fulfilled by a solution that gives reliable performance down to ±0.127 mm (0.005 in.)? Be aware that, just like size capability, increased accuracy increases the cost of a solution and can also limit flexibility. If your QC needs really are that tight, make sure the CMM you’re considering can deliver.
“If you have a 3-µ tolerance on a critical part, a fixed CMM is probably where you would look to measure that part,” says Mills. “If your needs aren’t quite as stringent, make sure you don’t pay for capabilities you don’t need.”
Oddly enough, matters of accuracy may not be as straightforward as one might think.
“Can you accurately measure something? Believe it or not, the answer to that is a subjective statement,” says Baker. “But asking, ‘Can you measure with confidence?’ can yield a yes or no answer. ‘Yes, we can discriminate between acceptable and not acceptable pieces for this application.’ With a portable CMM such as the FARO ScanArm, we prove out and build confidence by measuring customers parts, as opposed to relying on numbers on a technical data sheet for a fixed CMM.”
Although fixed CMMs can be more accurate in certain situations, they aren’t as effective when your production profile suggests more need for flexible quality control inspection methods rather than ultra-tight tolerances.
|
In many cases, it’s too easy to conflate accuracy with reliability. Make sure you know what you need.
Throughput requirements
If your facility needs to inspect dozens or even hundreds of the same part per day, a computer-controlled inspection system with an integrated, fixed CMM may be a cost-effective solution for your needs.
“If you want to do repeat-part inspection in high-volume with cycle times in the five-minute to one-hour range, a fixed CMM is a good way to do that,” says Mills. “It’s an interesting device to consider when you have high-volume, tight-tolerance requirements for a low number of part numbers.”
That kind of capability comes with caveats.
“Where the fixed CMM does fall down a little bit is when you have an application where you do need high accuracy, but you don’t really need the high-volume throughput,” explains Mills. “With the fixed CMM you have to write an inspection routine for each and every part, or you have to manually drive the CMM probe around with a joystick to take measurements. The joy of using a ScanArm is the flexibility; you don’t need a specific, preprogrammed routine to capture those data. With a fixed CMM, it’s not that easy to toggle things on and off, so you end up running the whole inspection routine to get those individual features you may need. Coming from a fixed CMM background, it took me a long time to realize just how flexible a portable CMM really is.”
|
Ease of operation
Once you have a firm understanding of your primary needs, you can then compare features that fall into the ease-of-use category. Risk factors such as employee turnover and shifting workloads make system usability a significant consideration.
“Out on the shop floor, you’re not talking about a controlled temperature environment,” says Baker. “The fixed CMM room is a temperature-controlled environment, so when you transfer a part into the CMM room to be inspected, you have to wait for it to stabilize before taking the measurements. Then it has to go back out to its machine, be reset up, and then finished. So there’s lots of additional complications and an extra square footage that you have to have available in order to store all those parts while they’re waiting to go on the CMM and transporting back to their machining center.”
“The FARO ScanArm provides a low-cost way of being able to mount the CMM to a machine center and inspect a part actually on-machine without having to break it down.”
|
The bottom line is this: If your quality control process requires ±3-µ tolerance and you run high-volume low-SKU product lines, an automated, fixed CMM may be your best choice.
On the other hand, if your organization’s situation looks more like this:
• Actual need for measurements falls outside of ±3 µ
• Automated long-run inspection isn’t a value-add
• Any one shift may be required to inspect several different part numbers
• It’s more beneficial to inspect parts on the shop floor
• CMM solution will be used to inspect multiple surfaces, shapes, and materials
• Current or prospective customers require a color map as part of reportage
• CMM solution may be used for reverse engineering
A portable CMM solution such as the FARO ScanArm may be a better fit.
“There are multiple aspects of flexibility, but for me it means being able to measure whatever I want, wherever I want, and the freedom to do so without a predefined inspection routine. I want to capture all the measurement data and evaluate those few points I’m after, and then have the ability to come back and look at data I didn’t even think about on the first go ’round.”
|
In any case, it is most wise to make your decision based on more than cost alone. Cost can be mitigated, delayed, and defrayed, but living with your investment on the shop floor will be immediate and unavoidable for the duration of ownership.
Attribute |
Portable CMM |
Traditional |
Amount of training required |
Medium for programming |
High for programming |
Noncontact inspection |
Yes |
Rare |
Programming required |
None |
Extensive* |
Collision detection programming required |
None |
Extensive** |
Fixturing |
Sometimes |
Complex, dedicated, and expensive*** |
“Metrology room” environment |
No |
Yes |
Transportable within production facility |
Yes |
No |
On-machine / in-process inspection |
Yes |
Rare |
Flexibility—measure virtually anywhere without predefined routine |
Yes |
Rare |
Accuracy |
High |
Highest, but high cost for high accuracy |
High-volume, repeat-part inspection |
Good |
Better, on high-cost CNC CMMs |
Cost |
Low to medium |
Medium to high |
|
||
Notes: |
||
* Some CMMs can be operated interactively (without programming) using just the joystick, but it is more time-consuming and less efficient than using a portable CMM. |
||
** Some CMMs have automated collision detection but tend to err on the safe side to avoid collisions, thus decreasing efficiency. |
||
*** Because fixtures tend to be dedicated, they need to be machined and CMM’ed. When a production run for a part is complete, the fixture often becomes scrap. |
Add new comment