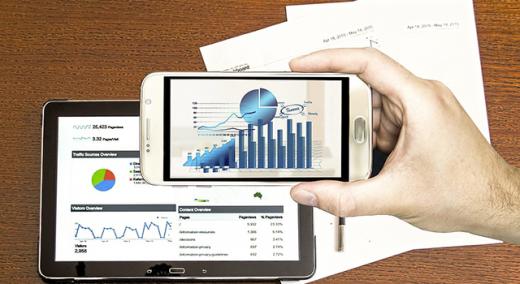
The seven basic tools of quality are a standard set of graphical methods for improving quality. They can help with understanding variation and determining the root cause of errors in processes. The seven basic tools are most commonly used within lean manufacturing. All of the tools are graphical methods that do not require much knowledge of statistics. One or more of them can solve most problems within quality improvement.
ADVERTISEMENT |
The set of seven tools became established in Japanese manufacturing during the post-WWII period, when W. Edwards Deming was promoting statistical quality control methods in Japan. The full set of statistical methods Deming taught included more advanced methods, such as design of experiments and hypothesis testing. These were too challenging for many production workers. Manufacturers, therefore, started trying to use simpler graphical methods whenever possible.
…
Comments
Most Commonly Used in Lean Manufacturing?
On what basis do you make this statement?
"The seven basic tools are most commonly used within lean manufacturing."
Thank you, Dirk
A Suggestion (Run Chart + Control Chart or Process Map?)
Hi Jody, thanks for putting the article out there. With all of the new shiny tools out there, it's sometimes easy for forget the power of the basics!
When we discuss the 7 Basic Quality Tools, we treat the Control Chart as a progression from the Run Chart later on (unless we're looking at a Critical Process/Control Point) and never side by side. This lets us make sure that the Process Map / Flow Chart is one of the 7 Tools.
What are your thoughts on this?
In our view, there's nothing like "seeing" what's REALLY going on then centering an improvement team around a visual tool like a VSM or basic swimlane.
Tim
Add new comment