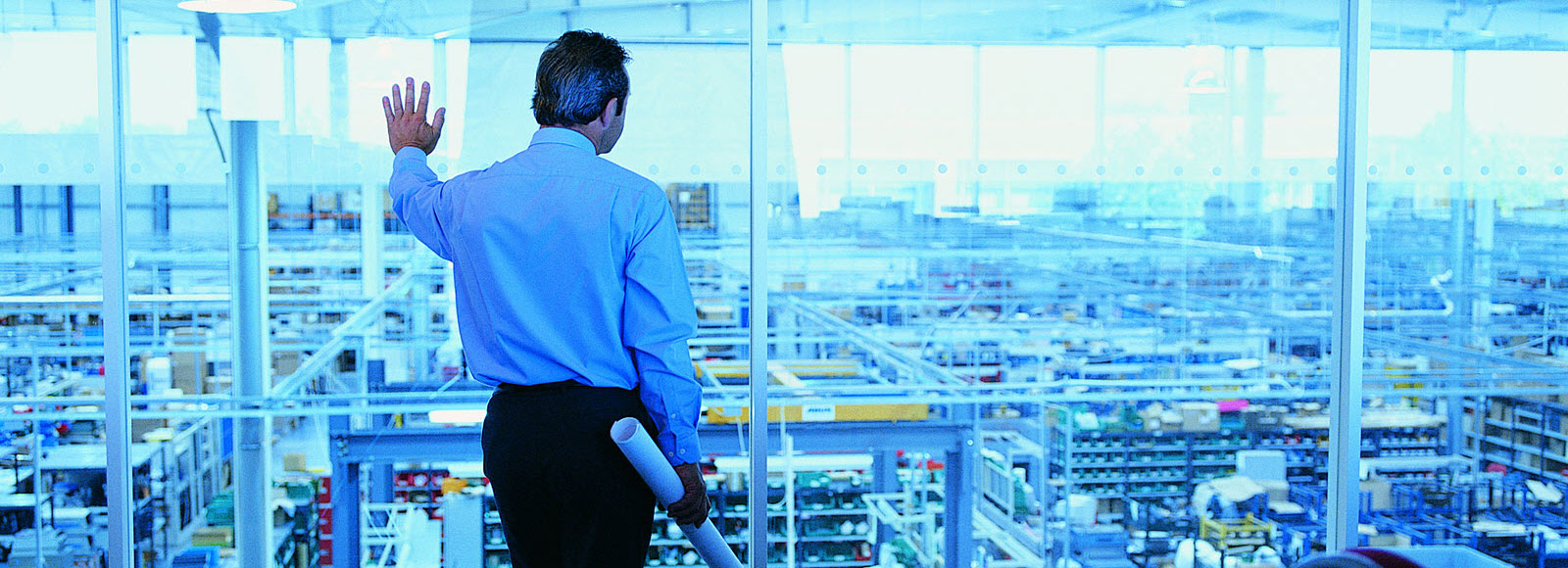
Manufacturers routinely face uncertainty, risk, and volatility in everyday operations. It’s understood that organizations must be ready for anything, from supply chain interruptions, supplier quality issues and process variations, to volatility in market demand, competitor activities, and political influences.
But the Covid-19 pandemic presents a level of impact that even the most seasoned manufacturing leaders haven’t seen. Organizations are responding at an incredible pace to continue providing necessary and in-demand products, while adjusting to either increased or decreased volume (or in some cases, both).
Companies are deploying new protocols and procedures to keep their employees safe, including moving many roles to remote work and adapting shifts and resources to reduce the number of personnel onsite at any one time. Some are even retooling and repurposing their factories to produce the goods that are most needed. Many are even going above and beyond, donating essential safety gear or food to support our frontline workforce.
These truly heroic efforts come at a cost, and for many organizations, they represent a way of working that is significantly new. Fortunately, technology offers solutions that manufacturers can employ quickly to enable improved efficiencies through shared information and better visibility across operations.
While manufacturers fight the immediate fires that the pandemic is having on operations, they also have opportunities to limit or mitigate the risks to their operations, people, and bottom line. Technology can play a vital role.
• Technology that supports the digital transformation of manufacturing operations can significantly help create a more flexible, agile, and responsive manufacturing environment.
• Further automating manufacturing operations and replacing manual processes with automated alternatives can help mitigate workforce availability challenges.
• Likewise, centralizing and standardizing operational and quality data enables remote-working quality managers and plant leaders to respond and adjust operations.
• And having real-time access to information across product lines and plants is essential for coordinating all these efforts.
The key to success for this digital transformation is ensuring that everyone, from the plant floor to the executive suite, has access to the information they need to do their jobs. Modern, cloud-based statistical process control (SPC) software solutions can provide the visibility and shared information base that are needed to coordinate efforts and help solve the critical challenges manufactures are facing right now.
Support a remote and mobile workforce
Manufacturing organizations have taken rigorous steps to protect the health and well-being of their employees, contractors, and even onsite visitors. For many, this means that many workers are asked to work remotely—something that many have not considered until now. Quality managers, engineers, plant managers, and executives may all be working offsite for an extended time, and they are looking for ways to connect and communicate effectively.
• Cloud-based software enables quality and operational data to be centralized, standardized, and accessible across products, lines, and plants.
• Remote monitoring and analysis software enables operations and management employees to stay productive, even when they can’t work onsite.
Maximize productivity of a reduced onsite workforce
Some functions simply have to continue onsite, but operators and other onsite staff may be stretched thin as organizations reduce the number of people on the plant floor. Some operators may be working different shifts or covering operational areas that are new to them.
• Automating routine activities such as data collection, monitoring, and reporting helps a limited or reduced workforce keep up with vital tasks.
• Role-based dashboard interfaces help workers quickly see the tasks and checks that are required and ensure they get done.
Increase or scale back output
When volume is critical, operations must scale up quickly while maintaining a high level of efficiency and productivity. When demand is down, organizations must protect the bottom line by reducing cost, waste, and giveaway, while optimizing worker efficiency.
• Fast access to quality and operational data from a centralized source enables quality teams and leaders to share information across the enterprise.
• New, sophisticated analytics enable offsite teams to view intuitive, visual reporting and identify when and where to adjust operations—by region, product, or plant.
Maintain product safety and quality
Even when personnel have to switch roles or step up to cover an absence, quality and compliance never take a back seat. The current chaos means that manufacturers must increase their focus on product safety and quality checks.
• Semi-automated and automated data collection, as well as automated alerts and notifications, help ensure checks are completed and data is accurate.
• Centralizing collected data in a single repository helps you build a clear picture of quality across the organization and ensures compliance data is available at a moment’s notice.
Respond and take action quickly
Operations managers and quality team members need to know the moment an issue arises so they can take steps to preserve quality or avoid costly missteps.
• Access to real-time data through a web-based interface enables fast, accurate decision-making.
• When everyone has access to the same quality information, pulled from standardized data, it’s easier to streamline communication, create best practices, and keep everyone on the same page.
Looking to the future
In manufacturing, production downtime should never be unproductive time, especially for management levels and above. One of the typical challenges in digital transformation projects is that leaders are so busy managing day-to-day operations that they can’t devote attention to the initiative. Yet many of these projects can be researched, explored, planned, and cultivated remotely.
While key members of the workforce are working remotely, a cloud-based quality management solution provides the data and analytics capabilities they need to work on these projects—and to develop them with the goal of reaping significant long-term benefits from the system.
Remote quality project leaders have the opportunity to answer a number of key questions your organization might not otherwise address:
• What do we need to know about how to improve our production processes that we don’t know at the moment?
• How can we better understand the variables that affect the quality of our processes?
• What data do we need to be able to do that?
• What solutions exist that could help?
All of these questions can be addressed remotely. All that is required is an internet connection.
Take advantage of data you already have with technology that exists now
During the chaos of the pandemic, the picture is changing daily, if not hourly. At this early stage, no one really knows the depth of the impact, how long the challenges will persist, or how long the recovery phase will take.
From a manufacturing perspective, there is no avoiding the impact of the crisis. But the technology to adapt to this “new normal” already exists. Cloud-native quality management software is purpose-built to address the challenges that are most urgent now—and to enable ongoing flexibility and adaptability as manufacturing markets adjust and recover. In addition, cloud software that uses a software-as-a-service (SaaS) model can be deployed quickly, on a pay-for-what-you-use basis, without extended contracts or costly infrastructure investments.
Take advantage of the solutions available quickly, and you’ll be in a position to survive and succeed going forward.
At InfinityQS, we understand that we all face some interesting and tumultuous times ahead. But we face them together. For the days and weeks to come, we wish all our manufacturing colleagues the very best. Feel free to visit our website to learn more about how our software solutions can help your organization in immediate and practical ways. Stay safe—and let us know how we can help you.
Add new comment