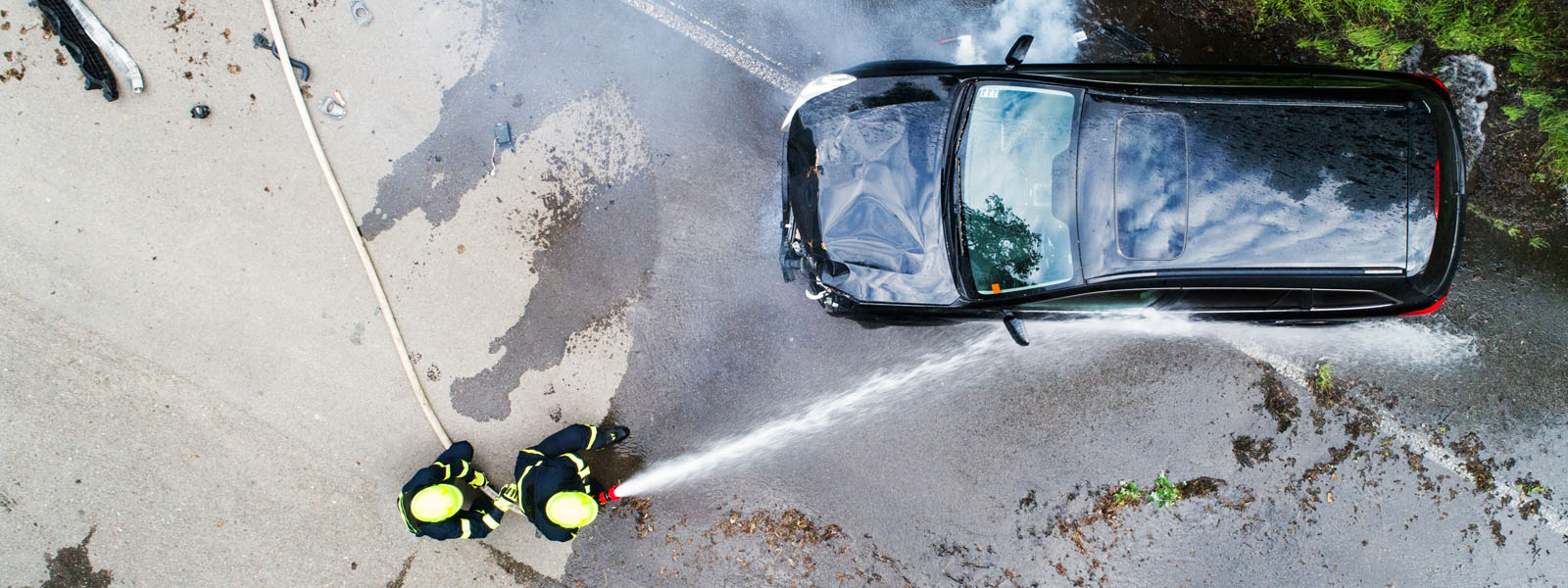
During the first six months after the publication of its first edition in June 2019, the AIAG & VDA FMEA Handbook gained popularity in the global automotive industry. Both U.S. and European OEMs have started to require the AIAG VDA approach to failure mode and effects analysis (FMEA) in their programs. Like the AIAG Guidebook, fourth edition, the handbook provides guidance, instruction, and illustrative examples of the requisite analytical techniques. The activities and analyses historically involved in FMEA have been formalized as discrete steps in the handbook.
The seven-step approach described in the handbook and outlined here guides the development of design, process, and supplemental monitoring and system response of FMEA through the sequencing (and the iteration) of described activities.
Step 1: Planning and preparation
Develop a failure mode and effects analysis (FMEA) project plan, including the identification of:
• The intent or purpose of developing the design or process FMEA
• The timing required to support critical product and manufacturing engineering decisions
• The multidisciplinary team of knowledgeable participants
• The tasks that will be required in FMEA development, beginning with the definition of the scope and level of the product or process to be analyzed, the product interfaces to be included, a decision whether a baseline/foundation/core FMEA will be used as a starting point for analysis
• The tools that will be used, e.g., adherence to which FMEA guidelines or “standards,” which software—spreadsheet or dedicated FMEA
Step 2: Structure analysis
Depict the product or process to be analyzed using an appropriate graphical or visual method.
• One new aspect of the handbook approach is the analysis of the “focus element” not as a standalone product but relative to product at the next higher level and the next lower level. The relationships among the system, subsystem, and components may be complex and challenging to analyze, especially without FMEA software.
• A boundary diagram or tree-structure diagram indicating the elements of the system or subsystem, the interfaces among elements, the interfaces between the target product and external elements would be employed in the design FMEA.
• A process flowchart or process tree structure that indicates the step-by-step process involved in manufacturing or assembling the target product or focus element, the specific work elements that make up each process step, and the higher-level process “item” would be used in depicting a process FMEA.
Step 3: Function analysis
Identify the functions to be performed and the requirements or criteria by which their performance is evaluated, for both design and process FMEA development.
• The handbook approach facilitates the flow-down and traceability of functions and requirements, from product level to level, including from customer to supplier.
• For the design FMEA (DFMEA), functions and requirements are identified by the focus element, the next lower level functions and characteristics, and the higher-level item that the focus element enables. Functions may be developed in tabular form or as a function-analysis tree structure. This function tree is usually developed in conjunction with the tree structure.
• For the process FMEA (PFMEA), the functions that each step of the manufacturing or assembly process must achieve on producing the product or focus element are identified. These are the functions (i.e., characteristics to be achieved) that are required at the next lower level, work-element level, and at the next higher level; the functions to be achieved overall; and the collective sequence of manufacturing or assembly steps. The depiction of step-by-step (i.e., workstation by workstation) achievement of each function and next lower level characteristic(s) is readily shown in a process flowchart.
Step 4: Failure analysis
Identify failure modes, effects of failure, and causes of failure.
The failure analysis step described in the AIAG & VDA FMEA Handbook is significantly different from the analysis of failure described in the AIAG FMEA Guidebook, fourth edition. (See figure 1.) The handbook instead promotes the use of a “failure chain” of the failure mode at the focus level, the effect of failure at the next higher level, and the cause of failure at the next lower level.
Figure 1: Failure analysis step from the AIAG & VDA FMEA Handbook, first edition, 2019
In the design FMEA, the definition of multiple types of failure modes—e.g., loss of function, degradation of function, intermittency of function, partial functioning, and unintended functionality—is the same for DFMEA in both the handbook and the AIAG Guideline. Failure modes apply to the failure of the focus element product to meet requirements.
Effects of failure are evaluated for impact on the next-higher level of product.
Causes of failure, per the handbook, are typically assigned to the components that make up the focus level of the product. Causes of failure at the focus-element level are only cursorily mentioned.
Given that most design related causes of failure occur at the interfaces between elements, the handbook’s emphasis on failures at the component level, does not appropriately address a very significant issue.
Some dedicated FMEA software systems, notably the Omnex AqUA Pro software, acknowledge the important need to include the analysis of integration and interface failures at the focus-element level. DFMEA improvement should be focused on causes of failure that are within the control of the FMEA team, vs. just assigning causes to the supplier or to a lower-level product.
Additionally, the handbook illustrates the relationship among different levels of product: system, subsystem, components, and feature characteristics, failure effects, failure modes, and failure causes cascade from one product level to the next. (See figure 2 below.)
Figure 2: Relationship among different levels of product, from the AIAG & VDA FMEA Handbook, first edition, 2019
The process FMEA also uses the failure chain as a model for failure analysis.
Failure mode, again using the various aspects of failure (e.g., loss of function, degradation of function, intermittent function, partial function, and so forth) is evaluated at the focus element.
Cause of failure at the next-lower work element level are also defined.
Effect of failure on the end-user, the plant personnel, and the production operation at the next-higher level are separately identified. Note: The effect of failure on the end-user is communicated from the design to the process FMEA. The PFMEA relies on this information to comprehensively address effect.
In both the DFMEA and PFMEA, the severity of the effect of failure is rated on a 10-point scale.
Step 5: Risk analysis
Estimate the level of design or process risk by assigning severity of effect, occurrence of the cause, and detection of the cause of failure.
• As in the AIAG Guidebook, fourth edition, the AIAG & VDA FMEA Handbook employs 10-point rating scales to evaluate severity, occurrence, and detection.
• The recommended method of combining these three indices into a single composite value is no longer the risk priority number. In the handbook the action priority matrix, a three-axis reference table, is used to assign a relative high, medium, or low need for action.
• The occurrence rating of the cause of failure is based on the current use of prevention-oriented DFMEA or PFMEA controls as well as the historical incidence of the causes of failure, e.g., field failures, warranty, customer issues, in-plant test and inspection failures (PFMEA); and design verification or validation failures (DFMEA).
• The detection ranking of the cause of failure is predicated on the effectiveness and capability of the detection control to assess the cause of failure, and during the product development timeline (DFMEA) or the process (e.g., within station, subsequent station, end of line) when the cause of failure is detected. Per the handbook, detection-oriented design and process controls are focused on failure mode in addition to cause of failure.
Supplemental Step 5A: Link special characteristics to functions and requirements
• The Omnex FMEA development process formally includes the identification of special characteristics and the linkage of FMEA from level to level and between design and manufacturing
• Identify potential special characteristics in the DFMEA, based on severity ratings and potential performance safety concerns.
• Transfer identified, potential special characteristics from the DFMEA to the PFMEA to underline the criticality and importance of process controls.
• Further identify special characteristics in the PFMEA based on the manufacturing or assembly organization’s station-by-station, and work element by element, process capabilities, and in-plant failures.
Step 6: Optimization
Based on risk evaluation, determine which aspects of the design and process require risk mitigating actions, and define those actions.
• Identified actions require the assignment of a person responsible for completion, a target date, status of each action, assessment of the effectiveness of actions, and re-rating of completed actions.
• Organizations may choose to use the suggested action priority matrix ratings of FMEA line items, or use company-specific values as criteria for establishing the need for further actions.
• Collaboration among the FMEA team, suppliers, customers, and company management is often needed to develop appropriate actions to reduce risks.
Step 7: Results and documentation
Summarize, highlight, communicate, and document the findings, risk reductions, and remaining residual product and process risk
• Develop a comprehensive report that includes the final risk status of the product or process
• Document and bring closure to the original FMEA goals, including whether the purpose of the FMEA was achieved, the high-risk failures that were addressed, and those that remain open
• Actively involve management in the review of findings
Supplemental step 7A: Document linkages
• The Omnex FMEA development process includes formal linkage of critical quality documents to design and process FMEA.
• Link content of design FMEA, and prevention and detection design controls, with the design verification plan and report
• Link the content of process FMEA, and prevention and detection process controls, with the process control plan, which subsequentially links with operator work instructions.
Omnex continues to incorporate innovations to FMEA. Most recently it has developed a methodology for identifying and including multipoint failures in the design FMEA. Using this approach, the DFMEA would serve as a repository for potential faults and failures resulting from the simultaneous and sequential causes, in addition to the traditional single causes. Additionally, the multipoint FMEA allows the FMEA, failure mode effects and diagnostic analysis (FMEDA), and fault-tree analysis to link; this is especially important to mechatronic and electronic designs.
Omnex has written white papers and conducted free webinars on these additional tools and topics and the AIAG VDA FMEA. Visit Omnex’s Resource center or contact Omnex at info@omnex.com.
Comments
AIAG VDA FMEA Process is Fundamentally Flawed
On Nov. 27, 2017, the Automotive Industry Action Group (AIAG) made a draft available of the AIAG-VDA FMEA Handbook that they co-developed with members from the VDA for a 90-day stakeholder review and commenting period. In response to that request I wrote the article "The Case Against the AIAG VDA DFMEA" which was published by Quality Digest on January 31, 2018 https://www.qualitydigest.com/inside/risk-management-column/case-against-aiag-vda-dfmea-013118.html . Within that article I explained that the FMEA process contained within the manual was not a harmonization of the 2008 AIAG 4th Edition FMEA Methods and the 2012 VDA FMEA Methods but rather an adoption of the fundamentally flawed German software driven VDA FMEA methodology that was first published in the form of a VDA FMEA manual in 1996.
Unfortunately, the released version of the AIAG VDA FMEA Handbook fixed none of the major problems in the version of the manual put out for stakeholder review in Novemeber of 2017. The final DFMEA and PFMEA methodologies contained within the AIAG VDA FMEA Handbook result in the creation of DFMEAs and PFMEAs that are ineffective in managing design and manufacturing risk and take considerably more time to create than DFMEAs and PFMEAs created using the AIAG 4th Edition FMEA manual methodologies. For more information on the weaknesses of the AIAG VDA FMEA methodology view the ASQ Risk and Reliability Division Webinar titled “ASQ AIAG-VDA FMEA Webinar - Implementing DFMEAs & PFMEAs Using the New Handbook” at ht tps://www.harpcosystems.com/videos/asq-risk-reliability-webinar-dfmeas-pfmeas-using-the-aiag-vda-fmea-handbook
In the article, the author states that that “Both U.S. and European OEMs have started to require the AIAG VDA approach to failure mode and effects analysis (FMEA) in their programs”. This is not accurate. While it would be expected for the European OEMs to agree to the VDA FMEA method they are already using, the same has not happened in the US. Since the publication of the AIAG VDA FMEA Handbook in June of 2019 only FCA US LLC of the big three automotive companies has published an IATF 16949 Customer Specific Requirement related to the AIAG VDA FMEA Handbook. In the July 8, 2019 Customer Specific requirement, FCA stated they preferred suppliers continue use the AIAG 4th Edition FMEA Method and that suppliers may use the FMEA process in the handbook under certain circumstances. Following is the FCA US LLC comment about their preference that the AIAG 4th Edition DFMEA method be used but allowing the use of the AIAG VDA FMEA Handbook DFMEA method found in their IATF 16949 Customer Specific Requriement:
"Organizations preparing DFMEAs should follow the AIAG Potential Failure Mode and Effects Analysis (FMEA). The AIAG/VDA Failure Mode and Effects Analysis (FMEA), Design FMEA and Process FMEA Handbook may be used, with analysis documented on the alternate form (Form B)."
Perhaps even more telling about the US automotive industry feelings about AIAG VDA FMEA methodology is the new revision of the SAE J1739 FMEA Manual Revision that has been delayed due to COVID-19. The SAE J1739 FMEA Manual is considered to be the FMEA bible for the US auto industry. It has aligned with the AIAG FMEA manuals for the last 18 years. I participated on a panel that included members of the SAE J1739 FMEA Manual Committee to discuss the pros and cons of the new AIAG VDA FMEA Handbook. Several members of the SAE J1739 FMEA Manual committee advised the audience to wait on the new version of the SAE J1739 FMEA Manual before moving to the AIAG VDA FMEA Handbook methodology. Based on their comments, the new SAE J1739 version is not going the adopt the AIAG VDA FMEA methodology. With its 120,000 members, the SAE has considerable power in the US automotive industry. Before purchasing any AIAG VDA FMEA Handbook related software or training, I would wait on the SAE FMEA Manual. You may not even have to change.
No Linkage Exists Between DFMEA & PFMEA Special Characteristics
The author introduces a supplemental step to the AIAG VDA FMEA process that exists in the Omnex FMEA development process titled “Supplemental Step 5A: Link special characteristics to functions and requirements”. The author states the supplemental step includes the following:
1. Identify potential special characteristics in the DFMEA, based on severity ratings and potential performance safety concerns.
2. Transfer identified, potential special characteristics from the DFMEA to the PFMEA to underline the criticality and importance of process controls.
The following will explain the proper use of the Class column in the DFMEA and PFMEA and why the suggested Supplemental Step 5A of the Omnex methodology is flawed.
For the sake of simplicity, a product that consists of hardware components and has no software will be used as an example.
The ISO 9001:2015 standard states that “Risk is often expressed in terms of a combination of the consequences of an event and the associated likelihood of occurrence”. ISO 9001:2015 requires the implementation of “Risk-based Thinking”. Using the ISO 9001:2015 definition of risk, let us examine how a properly constructed DFMEA can be used to demonstrate the company is using “Risk-based Thinking” in the design process. We will examine the important role the Class column plays when properly used in the DFMEA.
The DFMEA, when properly performed, is a risk assessment of the adequacy of the design (current hardware specifications) in defining a product that will meet the design requirements. Let us examine how the ISO 9001:2015 risk terms are translated to DFMEA terms.
1. In the Design FMEA, the objectionable event that leads to the “circumstances” is called the Failure Mode. Any failure of the design to meet a design requirement is an “objectionable event”.
2. The “circumstances” that can occur as the result of the objectionable event (Failure Mode) are documented in the Failure Effects column of the DFMEA.
3. A numerical rating equivalent to the severity of the worst case possible “circumstance” is placed in the Severity Rating Column of the DFMEA.
4. The potential Hardware Specification mistakes that may be present in the design being assessed that could lead to the objectionable event (Failure Mode) are placed in the Failure Cause column of the DFMEA.
5. The Prevention and Detection Design Controls columns of the DFMEA are used to capture the risk controls that will be used to determine the probability of the (event) Failure Mode occurring due to the Failure Cause (potential improper hardware specification) listed.
6. The results of the Prevention and Detection Risk controls are used to establish the probability of the Failure Mode due to the Failure Cause. A number corresponding to this probability is placed in Occurrence rating column.
7. A risk matrix exists that shows the level of residual risk for every possible Severity and Occurrence combination. If the residual risk is considered acceptable based on the product type being designed, the matrix contains no symbol for the Severity and Occurrence combination. If the residual risk is considered unacceptable, a symbol that is indicative of the level of risk is placed in the Class column of the DFMEA. These symbols are often referred to as a “Special Characteristic” symbols because properly documented DFMEA Failure Causes always consist of a Characteristic Specification and how it could have been specified incorrectly.
8. Any line in the DFMEA with a residual risk symbol (aka Special Characteristic symbol) must be worked on by the Design Engineer because the symbol indicates if the Design is manufactured as currently specified it will expose the user and/or company making the product to an objectionable level of risk.
The “Special Characteristic” in the Omnex supplemental methodology does not have a probability component consequently it cannot be used to represent residual design risk. The “Special Characteristic” in the Omnex supplemental methodology is nothing more than a restatement of the information found in the Failure Mode Effects and Severity Columns of a properly performed DFMEA.
Proper Use of Class Column and Special Characteristics in the PFMEA
The PFMEA, when properly performed, is a risk assessment of the adequacy of the process (suppliers, process equipment, process controls) in producing a product to the hardware design specifications. Any time an out of spec condition is created (PFMEA Failure Mode) there is an exposure to circumstances (PFMEA Failure Mode Effects and Severity Rating). Prevention and Detection risk controls are used to reduce the risk. When the PFMEA Class column is properly populated the Special Characteristic symbol for each row of the PFMEA it is determined using the Severity and Occurrence ratings from the row. The PFMEA special characteristic placed in the Class column represents the residual process risk that remains after the Prevention and Detection controls are implemented.
The Omnex methodology states that the special characteristics are to be transferred from the DFMEA to the PFMEA. This cannot be true since the DFMEA Class column entries when properly determined are representative of design residual risk and PFMEA Class column entries when properly determined are representative of processing residual risk.
The improper use of special characteristics in the DFMEA and PFMEA as defined in the Omnex supplemental methodology is very common throughout the US automotive industry. There are many potential sources of this mistake that are beyond the scope of this comment. We have had to provide our FMEA software customers with multiple responses to respond to their customers who do not understand the proper use of the DFMEA and PFMEA class column. Sometimes our customer’s customers demand that the columns be used incorrectly. We have added special features in our FMEA software to deal with this situation.
One of the most powerful indicators that the AIAG VDA FMEA Committee did not understand the importance of the DFMEA Class column is its removal from the AIAG VDA DFMEA form.
If you want to learn more about the proper use of the DFMEA and PFMEA Class (Residual Risk) columns watch the ASQ Risk and Reliability Division Webinar “How to Assign FMEA Ratings” at https://www.harpcosystems.com/learn/resources/how-to-assign-fmea-ratings
Lack of proper copyright reference
The document is called the "AIAG & VDA FMEA Handbook, 1st Edition, 2019". At least give proper copyright references when using text and/or figures directly from the manual.
Add new comment