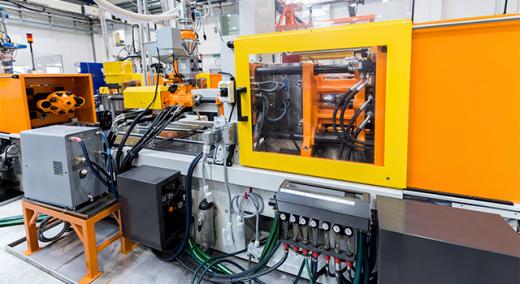
Injection mold making used to be a relatively simple business: machine the cavities and runners, polish, cross-drill for cooling, then shoot resin. Today, however, relentless pressure for lower part cost and higher productivity have led to bigger, faster machines with molds to match.
ADVERTISEMENT |
Multilayer stack molds, gas-assisted molding, overmolding, co-injection, advanced hot-runner systems, and other technologies have collapsed the cost of high-volume commodity resin parts. At the other extreme, a new generation of functional fillers and special-purpose engineering resins are allowing very large, special-purpose part making for industries such as automotive, aerospace, and medicine. In every application, cycle time, dimensional stability, and surface finish are paramount; hiding a sink mark under a trim plate just doesn’t cut it anymore.
Despite all the technical understanding of making injection molds, a surprising number of manufacturing engineers know very little about the complex dynamics that happen inside an injection mold.
…
Add new comment