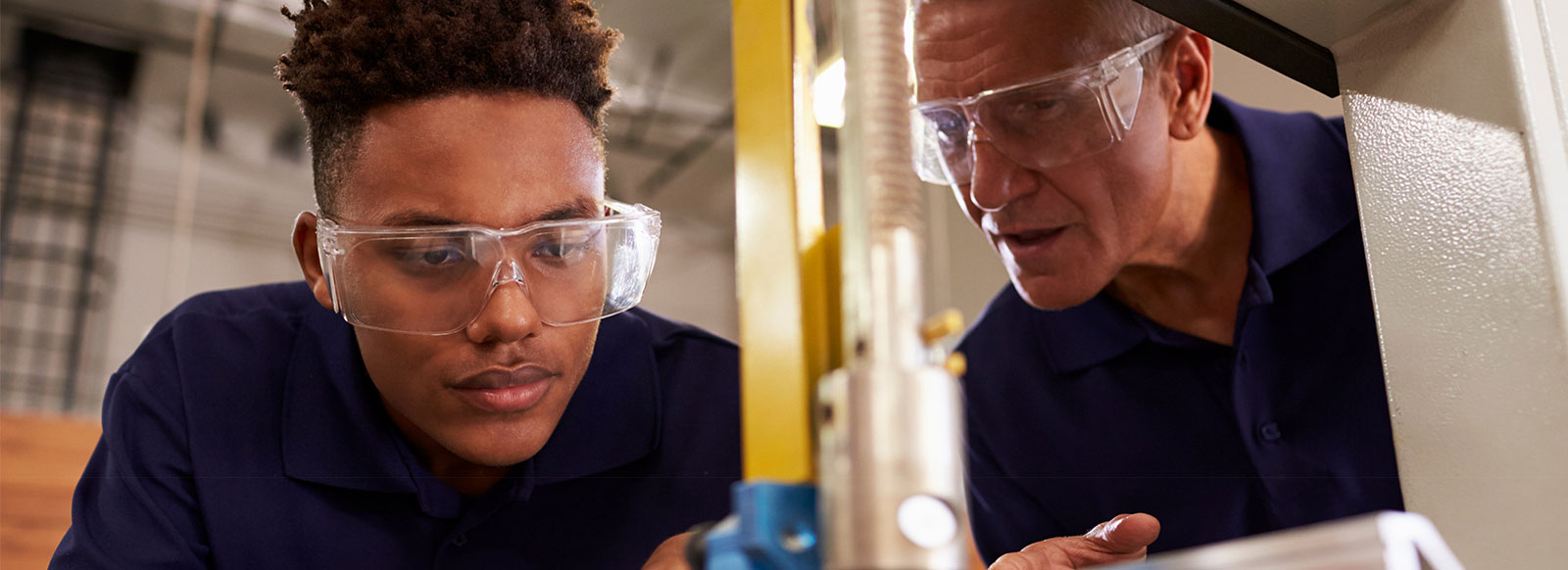
The reality for small and medium-sized manufacturers (SMMs) is that they are going to have to be good at training their workforce or they won’t make as much money. That’s a blunt assessment, but the need for proficiency in training will only increase, whether it’s retraining current employees for new products, processes, and equipment or getting new employees up to speed more quickly. Effective training should be able to drive down the time for training.
Some 39 percent of manufacturers plan on cross-training to help employees assume new job roles, particularly in the aerospace and defense sectors. Even more manufacturers, 62 percent, plan on making investments in technology, such as robotics, digital security, and 3D printing, in anticipation of the post-pandemic recovery.
These statistics—as well as manufacturers’ everyday experiences—point to a sector undergoing widespread change, making it a perfect time to pause and think about how best to train your workforce.
The case for addressing your training programs
This is a great time to improve your manufacturer training prowess for a lot of reasons:
• The skilled-worker shortage is not going away as employees age out and take their tribal knowledge with them.
• Processes will continue to evolve as more equipment is networked and connected for Industry 4.0.
• Job roles continue to evolve as the rate of technology adoption increases for machine learning, artificial intelligence, virtual reality, and augmented reality.
• Pivots are more likely to increase than decrease as supply chain disruptions and emerging opportunities continue to evolve.
• You may be less busy and have time to invest in training.
In fact, the Covid-19 pandemic has already forced many SMMs to improve their training and continuous improvement mindset. Most manufacturers have had to adapt in numerous ways, such as:
• Process changes related to social distancing
• Adapting to more remote staffing, virtual monitoring, and video conferencing
• Adjusting to less staff and how to do the same amount of work but with fewer resources
• Hiring more help due to significant increases in operations
Why legacy manufacturing training hasn’t worked well
Legacy training for SMMs often amounted to a veteran technician teaching a newcomer how to operate a machine in a relatively compressed time period. But good operators don’t always make good instructors, and handing a trainee a 20-page instructional manual and sending him to the production floor will not adequately transfer knowledge on how to perform complex processes, or operate more complicated machines.
In many ways, this historical approach is like smashing your face into a birthday cake. You can’t consume it all at once, let alone enjoy it. However, you can enjoy your birthday cake in pieces and small bites. Training an operator is no different: She might not grasp everything all at once, but she will become proficient if given a series of lessons and practice time.
Nuances and subtleties can be transferred over time. Operating best practices must be understood before troubleshooting makes sense. “How” is imperative, but so is “why.” It might seem odd that many SMMs have processes that vary slightly from first shift to second shift, but the operators involved have preferences and reasons for why they do what they do. That’s the nature of people.
Likewise, when there are breakdowns on the production floor, corrective action often becomes retraining the employee as opposed to retraining the trainer. “Operator error” is a bit of a misnomer; inadequate training may be the root cause of the breakdown. The mantra for the best trainers should always be, “If the worker hasn’t learned, the instructor hasn’t taught.”
How job instruction fits into the training ecosystem
Training Within Industry (TWI) is a program of hands-on learning and practice that teaches essential skills for supervisors, team leaders, and anyone who directs the work of others. TWI, which dates back to World War II and the repositioning of factories and the workforce to help the war effort, is an element of lean and continuous improvement programs.
TWI has three major modules:
Job methods (JM): The emphasis is on how to improve the process for doing the work.
Job instruction (JI): The focus is on what advances the work, defining the key points in doing the work, and understanding why the work has to be done that way.
Job relations (JR): This helps supervisors manage workers effectively and gets people to cooperate and avoid problems.
Although each of these steps plays a key role in training, JI is foundational in manufacturing with its focus on standardization and precision. The goal of JI is to train people to be able to do a job quickly, safely, and conscientiously.
But it is not just about doing the work. Understanding the “whys” of doing a task correctly is a critical component for SMMs. The key points include those tips, tricks, or knacks that often aren’t documented anywhere. It is the essence of how tribal knowledge can be transferred from aging machine operators and technicians to new workers.
People learn through demonstration, repetition, and small steps
Our learning patterns are established at an early age, through showing, telling, and repetition. You also don’t learn everything at once. JI follows a similar methodology for how you may have learned to swim or ride a bicycle.
Here’s how JI works best in a manufacturing setting:
One-to-one demonstration: A hands-on approach allows the trainer to show specifics or nuances of the task and provide direct feedback as the trainee does it.
Repetition: Knowledge of how to do a task does not become a competency until it is practiced.
Small bites: Machine operations often have many variables. You establish competency in one area before taking on others. (Don’t smash their face in the cake!)
Think of JI as like learning to play a musical instrument: A student must learn the technique to play the instrument, and then how to play different notes. Even with that knowledge, he must practice to become competent before being able to play a song.
Looking around the next corner: Who is going to train your cobots?
Here’s another factor to consider for your training: the growing adoption of collaborative robots (cobots). SMMs are increasingly turning to cobots to do physical and repetitive jobs such as machine tending, packing boxes, and moving inventories. Cobots work safely alongside humans; think of them as production-floor assistants that do the dirty, dangerous, or dull work but never call in sick. They come at a significant savings compared to automation systems and help position SMMs for additional technology adoption.
Cobots free up humans to do more knowledge-based and value-add tasks, such as:
• Making decisions on production quality (e.g., at what point does a cosmetic scratch make a part defective?)
• Machine setups
• Monitoring more of the operation
• Training cobots to do additional tasks
The demand for knowledge-based workers increases in manufacturing as technology takes over more of what traditionally was manual labor. This means training people differently.
Connect with experts at your local MEP center to address job instruction needs
There is no doubt that your company’s ability to train will be put to use in the near future. Economic disruptions lead to indirect shifts in the workforce; people retire earlier than planned and are more likely to change industries. Demand will return. Technology rolls on. You will be managing new people, new roles, and new work.
Improving your job instruction prowess can reduce training time by 25 percent, increase production, and reduce scrap, just like it did for the factories that used TWI during World War II. An added benefit is the transfer of tribal knowledge while building a continuous improvement mindset.
To learn more about how job instruction and TWI can benefit your operation, connect with experts at your local MEP Center.
Comments
Lean Six Sigma Yellow Belt Training
For almost 10 years I've offered free Yellow Belt training at www.lssyb.com. Because of the pandemic, I have been offering free certification as well.
Add new comment