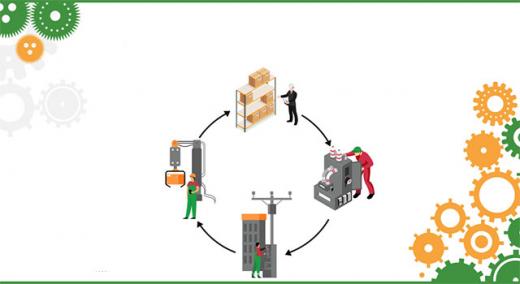
‘Little things make big things happen.” In just a few words, this cliché sums up MRO and its benefits. But what are these “little things,” and what effects do they have on your company’s bigger picture?
ADVERTISEMENT |
In the complex world of maintenance, repair, and operations (MRO), answers to these questions are pretty much company-specific. How your company defines and measures the impact of MRO activities largely depends on the type of business you run.
In manufacturing and other asset-heavy industries, a lack of strategic MRO management can cause huge operational issues. For instance, up to 50 percent of prolonged unscheduled downtime is due to a lack of spare parts or stockouts, which are often the consequence of poor MRO practices.
By the end of this article, you’ll get a better understanding of:
• What MRO stands for and how to define it for your specific operation
• MRO’s meaning in supply chain and procurement
• The four main MRO categories
• How to manage certain aspects of MRO with a computerized maintenance management system (CMMS) such as work, inventory levels, and costs
…
Add new comment