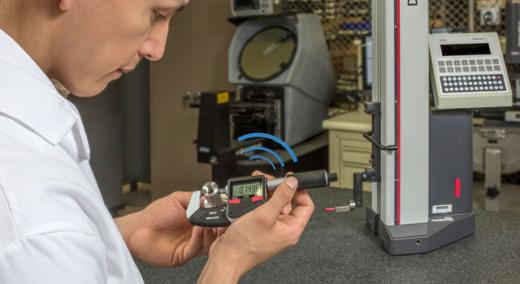
Inspection is often subject to the management team’s efforts at cost control or cost containment, as is the case with most other areas in modern manufacturing operations. Although it’s sound business judgement to maximize the value of every dollar, it also means that hard choices must be made when selecting handheld gauges.
ADVERTISEMENT |
For example, issues as diverse as training, personnel, throughput requirements, manufacturing methods and materials, warranties, the intended end-use of the workpiece, and general company policies on gauging methods and suppliers may influence both the effectiveness and the cost of the inspection process.
Furthermore, many companies have moved inspection out of the lab and onto the shop floor. By having the gauging at the point of manufacture, bad parts can be found immediately, and corrections can be quickly implemented to prevent others from being made.
…
Add new comment