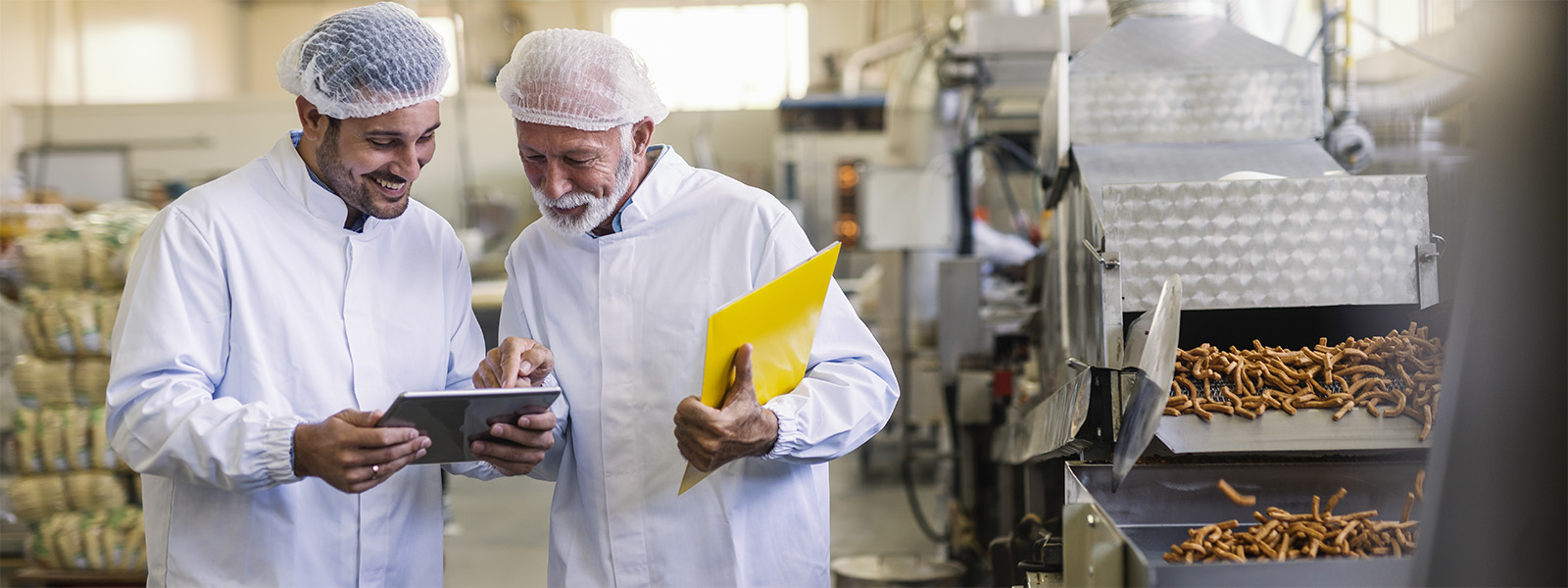
Manufacturers have seen the need to digitize operations for quite some time, but the Covid-19 pandemic has forced the issue to center stage. They’ve had to adapt to sudden, dramatic changes like more remote workers and social distancing across production lines. It didn’t take long to realize the outdated, manual tools they’d been using for years made it difficult to respond.
Where to start with digital quality management
To gain traction and map a path forward, look first at fixing areas especially hampered by outdated, manual processes—such as quality management, process optimization, and compliance checks. It’s time to consider a tactical, quality-led approach to digital transformation.
Now, more than a year after the big disruption, manufacturers know they need to undergo a “digital transformation” to be successful today and in the future. There’s strong demand in the industry to become more flexible, efficient, and cost effective.
But digital transformation isn’t easy. It isn’t cheap. And it can be overwhelming to consider an overhaul of every system across production. So what’s the right approach when digitizing production operations? Where do you start? How can you make lasting change?
Because digital transformation is an enterprisewide initiative, it’s a good idea to take a tactical approach. Look first at fixing areas especially hampered by outdated, manual processes.
Start with quality
Bringing quality and operational data—as well as processes—online is the best place to start a digital transformation.
Why?
Manufacturers found out the hard way that their employees need remote access to critical production and quality data. The pandemic forced quality professionals and other staff deemed “nonessential” to work remotely. Remotely does not just mean from home, but also off the shop floor in socially distanced back-office settings. Because this area of manufacturing still captures and records data using paper-based and manual processes, these workers continue to struggle to get the information they need when they need it. Without easy access to data, upholding product quality and ensuring compliance—without slowing production—can prove challenging. A lack of visibility into where trouble spots or bottlenecks occur weakens efficiency and productivity efforts, just when they are needed the most.
So then how can manufacturers bring this critical information online?
Manufacturers should consider moving processes and data found in legacy statistical process control (SPC) systems to a modern, cloud-based quality intelligence solution.
SPC methodology is the gold-standard for detecting variance in manufacturing processes. SPC enables manufacturing process control and is key to discovering insights necessary for continuous improvement and achieving manufacturing optimization.
When you modernize with cloud-based SPC, it changes how important data are captured, stored, accessed, analyzed, and used. This centralized data-driven capability provides the foundation for a more agile, productive, and cost-effective organization. Once all your information is online and connected, it becomes easier to identify and prioritize other areas of operations that need to be digitized.
Benefits of a cloud-based SPC system
Let’s consider four key benefits of implementing a cloud-based, SPC-driven quality system.
Improve quality
When a company moves all its quality data and processes online via the cloud, this allows them to see manufacturing quality across their entire production process. That makes it easier to identify where they need to focus efforts to improve quality.
A cloud solution also:
• Streamlines and automates data collection
• Stores data in a centralized, unified data warehouse
• Offers a holistic view of operations
• Empowers users to see and respond to issues in real time
Optimize processes
A centralized, cloud environment saves time. That’s imperative to optimizing processes. In a legacy SPC system, workers spend most of thier time collecting, preparing, and importing data. Then they’re often left to perform analysis manually, using complex spreadsheets.
But the cloud is different. In the cloud, data are standardized and live in a central location. That frees workers to focus on important things, like continuous improvement, that propel a company forward.
More process-related benefits of the cloud include:
• Real-time analysis from within the SPC system
• Configurable data-entry validation and automated data collection, ensuring accurate information
• Easier ways to identify and share best practices, leading to improved efficiency across the organization
• Improved collaboration
Reduce costs
Cost is a major reason why cloud-based applications from software as a service (SaaS) companies are popular in almost every industry. There are two main ways the cloud saves money: IT costs and pricing structure.
Information technology (IT) teams desire simplicity. Most likely every department within a company uses several software applications. Managing all those applications can be difficult for IT teams.
These key features let IT teams benefit from cloud-based SPC systems:
• Simple to deploy and manage
• Saves time, freeing up IT resources
• Easy to configure and scale
Pricing structure is another major reason the cloud makes business sense. In the SaaS model, the provider carries the burden of hosting and maintenance. Companies see the value of this model through:
• Reduced hardware costs
• Flexible licensing structures, paying only for what is used
• Reduced software maintenance costs via automated updates
Ensure compliance
Modern-day manufacturing is fast and complex, leaving little room for error. Manufacturers using a legacy SPC system often spend too much time managing their system and training employees to use the system.
But a cloud-based SPC system can help ensure compliance with:
• Data collection and traceability
• Compliance reporting
• Automated employee training
• Easy drill-down capabilities to pinpoint the cause of problems and speed resolution
• Intuitive, web-based user interfaces
• Automated alerts that empower users to identify and correct issues immediately
Compliance shouldn’t slow down manufacturing. With the cloud, it doesn’t have to. When manufacturers become more responsive to quality events, compliance is streamlined.
Cloud technology is the future
It’s now widely known and accepted: Digital transformation is essential to manufacturers’ present and future success. But it’s equally important to grasp the fact that digital transformation in manufacturing doesn’t happen overnight. Companies need to pursue a tactical approach, starting in areas like quality that, when digitized, can be a competitive differentiator. Those who adopt cloud-first strategies will have the greatest opportunity to improve efficiency and maximize output.
Moving from a legacy SPC system to a cloud-based system is easy with the right technology partner. At InfinityQS we have deep, proven experience helping manufacturers realize success with cloud technology. To learn more, visit our InfinityQS cloud solutions page.
Add new comment